Cleaning & Sanitizing
Maintaining cleanliness and functionality in conveyor systems is crucial for operational efficiency, product quality, and regulatory compliance. Here, we will delve into detail about cable & tube conveyor cleaning when it comes to our industrial conveyor belt systems. Maintenance and cleaning are paramount in the food industry, so to keep your conveyor belt for food operationally efficient, it needs to be in a sanitary condition.
Cable & Tube Conveyor Cleaning
Each facility tailors its own sanitation protocols, taking into account its individual sanitation requirements and the specific challenges presented by its materials. There are several options available for cleaning and sanitizing a tubular drag conveyor, and the choice of method depends on the nature of the material being transported.
The material’s interaction with water will determine whether a wet or dry cleaning method is more suitable. Cablevey provides both wet and dry cleaning options for tube conveyors. Our tube conveyors are designed explicitly for food-grade applications, and we strive to eliminate areas where fines could gather, including:
- Solid discs that lack screws or bolts,
- “Jacketed” cables enclosed in nylon casings,
- Discs that are attached to the cable,
- Stainless steel connectors,
- Detachable equipment to simplify the cleaning process.
What makes Cablevey stand out from the competition when it comes to CIP?
Cablevey Conveyors are designed to be the sanitary solution
for your conveying needs. Product is moved in an enclosed
system to eliminate the mess seen with non enclosed
systems. All conveyors are designed to be cleaned without any
disassembly needed. All conveyors are made out of chemical
resistant materials (stainless steel or CVT). All systems are
easily customizable to be wet or dry cleaned depending on the
needs of the customer.
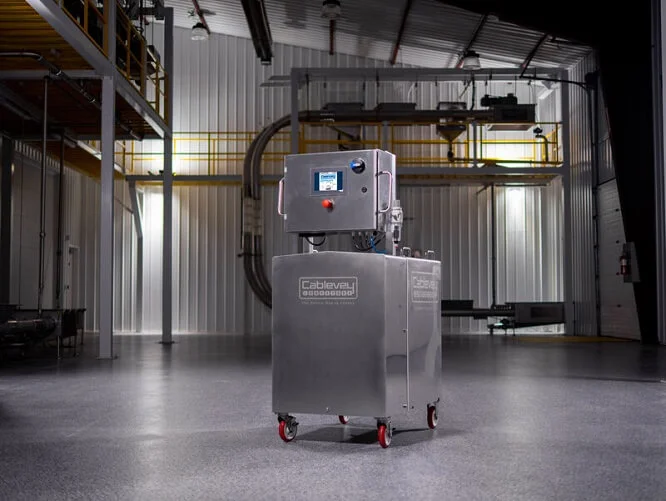
Dry Cleaning
We offer a highly efficient and effective dry cleaning technique for internal maintenance of tube conveyors, particularly suitable for our 4″, 6″, and 8″ diameter systems. This cleaning approach leverages various specially-designed tools, which work in unison to maintain the cleanliness and efficiency of the conveyor system.
The dry cleaning process targets accumulated fines – small dust or particulate matter that can build up over time – removing them from discs, the critical components that move materials through the conveyor system. Each tool in this method plays a vital role in ensuring the smooth running of the conveyor.
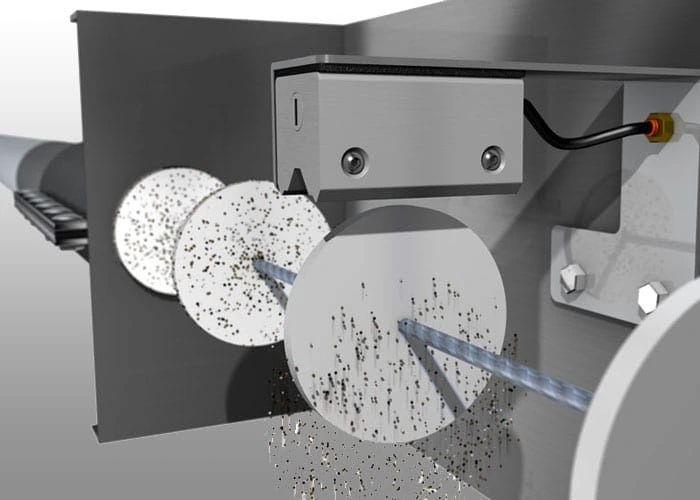
Air Knife
The air knife is a strategically located line insert that uses the force of compressed air to dislodge and blow away fines that have accumulated on the discs, thereby ensuring their optimal functioning.
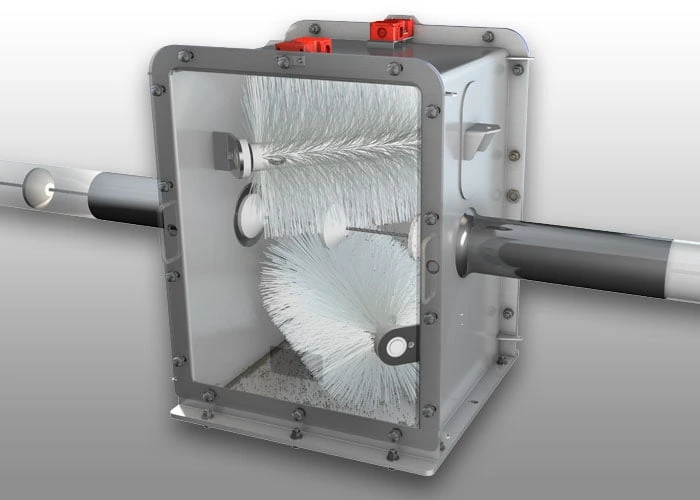
Brush Box
The brush box, another line insert, contributes to the cleaning process through mechanical means. It actively brushes off the gathered fines from the discs, allowing them to continue their role unhindered.
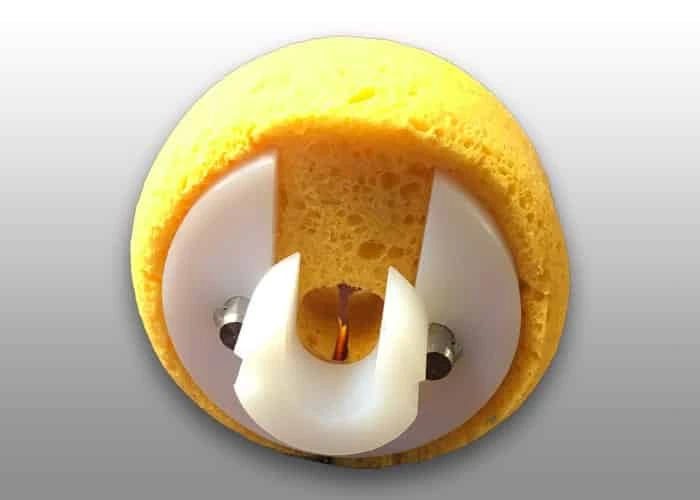
Sponge Disc & Sanitizing Cleaner
The sponge disc is a disposable item that’s saturated with a cleaning agent and then introduced into the system. As it traverses the conveyor, it effectively removes residue and sanitizes the internal surfaces.
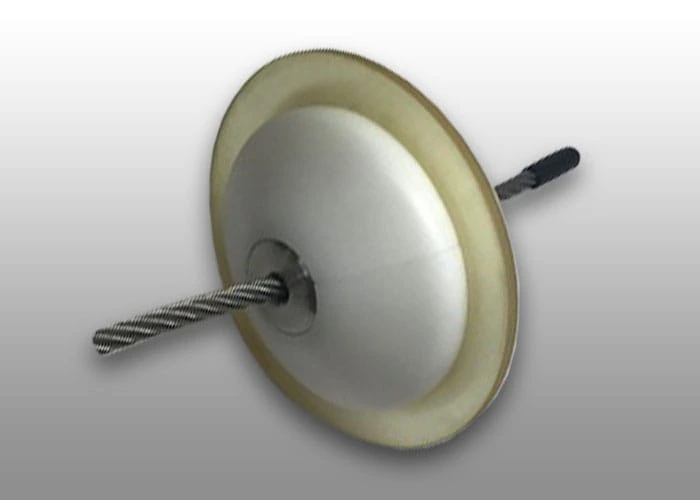
Urethane Wiper Disc
A urethane wiper disc is a disc insert that works like a squeegee, sweeping away any lingering fines and particles, ensuring a thoroughly clean system that’s ready for efficient operation.
Wet Cleaning
Our commitment to maintaining the integrity and efficiency of our conveyor systems includes offering a rigorous and comprehensive wet cleaning option. This wet cleaning process is specifically designed for our 4″, 6″, and 8″ diameter systems.
It’s an advanced 3-step procedure that cleans the interior of tube conveyors thoroughly and efficiently. Its primary advantage is its simplicity and speed, ensuring minimal downtime for your operation while guaranteeing optimal cleanliness. The method is particularly ideal for situations where materials being conveyed may have higher moisture content or when the substance has the potential to stick to the interior parts of the system.
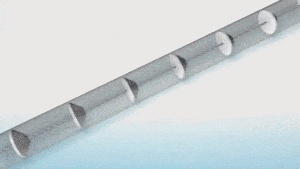
Water Rinse
Once the conveyor system has completed a cycle of material transportation and is empty, water is introduced to wash away residual material from the interior surfaces of the tube, discs, and cable. This initial rinse acts as a first line of cleaning action, prepping the conveyor for a more thorough cleansing.
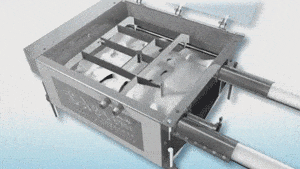
Foam Agent
The foam cleaning agent is introduced into the tube environment to cleanse all system’s internal parts. This cleaning solution is inserted into the conveyor’s environment where it expands and moves along the length of the system, effectively interacting with all the internal components and surfaces.
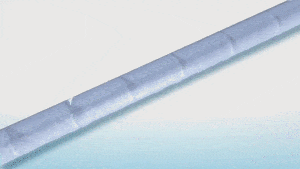
Water Rinse
A second rinse of hot water flushes out sanitizing rinse rendering the tube environment production ready. It ensures the complete removal of the foam agent, prepping the system for a sanitizing rinse.
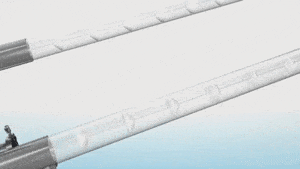
Sanitizing Rinse
The sanitizing rinse is the final cleanse of the wet cleaning process, and it runs a sanitizing solution through the system to completely eliminate any remaining debris and foam agent residues, ensuring an ultra-clean, ready-to-go system.
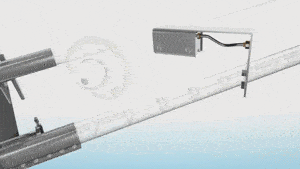
Drying
The duration of the drying phase depends on the particular length and layout of your tubular system. This step ensures that no residual moisture remains within the system, protecting against potential moisture-related operational issues and ensuring the peak performance of the system for the subsequent operational cycle.
Advanced Cleaning Solutions for a Belt Conveyor System With Cablevey Conveyors
Our commitment to maintaining the integrity and efficiency of our conveyor systems includes offering a rigorous and comprehensive wet cleaning option. This wet cleaning process is specifically designed for our 4″, 6″, and 8″ diameter systems.
It’s an advanced 3-step procedure that cleans the interior of tube conveyors thoroughly and efficiently. Its primary advantage is its simplicity and speed, ensuring minimal downtime for your operation while guaranteeing optimal cleanliness. The method is particularly ideal for situations where materials being conveyed may have higher moisture content or when the substance has the potential to stick to the interior parts of the system.
Learn More About Our Systems
FAQ
Why Is Cleaning Important for Cable and Tube Conveyors?
Cleaning is vital for cable and tube conveyors to maintain operational efficiency, prevent build-up of materials, ensure the quality of products, and comply with sanitation regulations, particularly in industries such as food processing and pharmaceuticals.
How Often Should Cable and Tube Conveyors Be Cleaned?
The frequency of cleaning cable and tube conveyors depends on several factors, including the type of material being transported and specific industry regulations. However, it’s generally recommended to clean these systems after each major production run or at least once a day in high-use environments.
What Are the Potential Consequences of Inadequate Cleaning?
Inadequate cleaning can result in the build-up of materials, leading to blockages or reduced efficiency. This can negatively impact the quality of products and may even lead to equipment damage. Moreover, it can result in non-compliance with hygiene standards, particularly in industries where cleanliness is paramount.
What Cleaning Methods Are Recommended for Cable and Tube Conveyors?
Both wet and dry cleaning methods are typically recommended for cable and tube conveyors. The choice between these methods depends on the nature of the material being transported and its interaction with water.
Can Cleaning Chemicals or Detergents Be Used on Cable and Tube Conveyors?
Yes, cleaning chemicals or detergents can be used, but they should be selected carefully based on the material of the conveyor and compatibility with the product being conveyed. Food-grade cleaners are recommended for systems used in food processing industries.
Are There Any Specific Safety Precautions to Consider During Conveyor Cleaning?
Safety precautions during conveyor cleaning include isolating the system from power sources, using appropriate personal protective equipment, and using approved cleaning agents to prevent damage to the conveyor materials.
What Are the Common Challenges Faced When Cleaning Cable and Tube Conveyors?
Some common challenges when cleaning cable and tube conveyors include the accessibility of certain parts, the potential for water damage in certain systems, and removing stubborn or sticky material residues.
Are There Any Specialized Tools or Equipment Required for Conveyor Cleaning?
Specialized tools may be required for cleaning, including brushes, air knives for dry cleaning, and specific agents like foam cleaners or sanitizing rinses for wet cleaning.
How Can Conveyor Cleaning Contribute to Overall System Efficiency?
Regular conveyor cleaning can contribute to overall system efficiency by preventing build-ups that could lead to blockages or slow down the operation. It also extends the lifespan of the equipment and ensures consistent quality of the products being conveyed.
Can Cleaning Intervals Be Adjusted Based on the Type of Material Being Transported?
Yes, cleaning intervals can be adjusted based on the type of material being transported. Materials that are more likely to stick or leave residue may require more frequent cleaning, while others might not.