Total Preventative Maintenance
By implementing total preventative maintenance strategies, businesses can significantly reduce downtime, enhance operational reliability, and improve the overall productivity of their industrial conveyor systems. A comprehensive maintenance regimen involves regular inspections, timely repairs, and systematic upgrades, ensuring that every component of the conveyor system functions optimally.
What Does Total Preventative Maintenance Mean for Conveyor Systems?
Total Preventative Maintenance (TPM) for conveyor engineering represents a holistic approach that emphasizes the importance of preventive measures to ensure the continuous, efficient operation of conveyor belts and tubular conveyor systems within industrial settings. Unlike reactive maintenance strategies that address issues after they occur, TPM focuses on preventing problems before they happen.
These measures involve routine inspections, scheduled maintenance, and the active involvement of all employees, from operators to management, in maintaining equipment health. By adopting TPM, organizations can significantly reduce the likelihood of unexpected downtime caused by equipment failure, thereby maintaining productivity and reducing repair costs. TPM also extends the lifespan of conveyor solutions by identifying and rectifying wear and tear before it leads to major breakdowns.
Additionally, TPM fosters a safer work environment by minimizing the risks associated with equipment failure. Overall, TPM transforms maintenance into a valuable component of the production process, ensuring that conveyor technologies are always in peak condition and ready to support business operations.
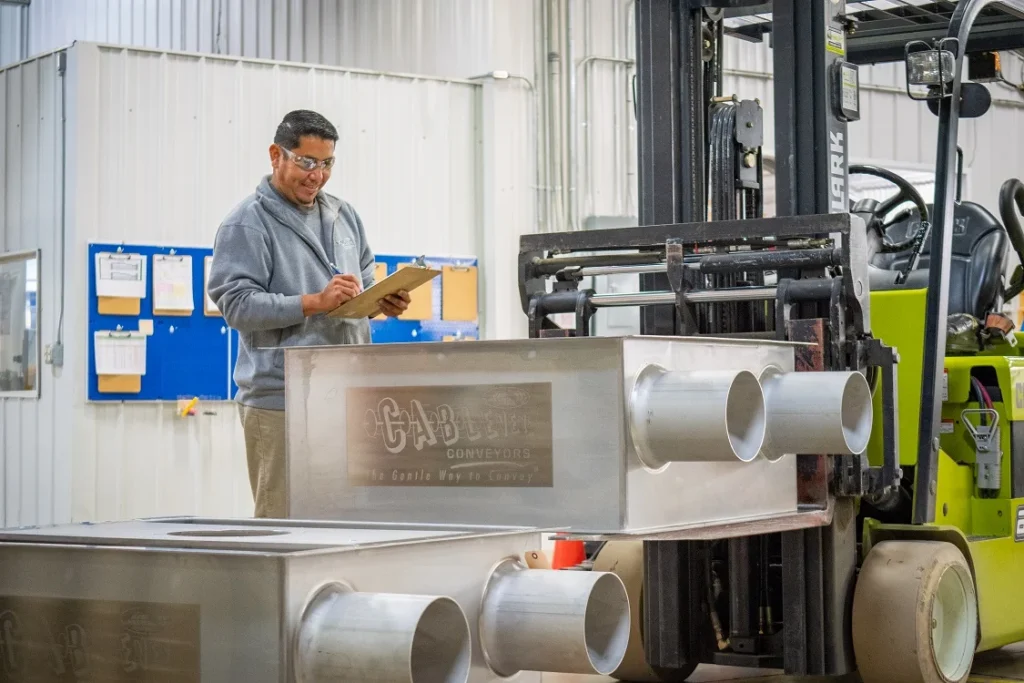
Scope of Work Done as a Part of Total Preventative Maintenance
What services are included in TPM? This extensive maintenance will include annual service inspection, replacement, and calibration of any components outside the specification of the conveyor system or systems, such as:
- Cable & connector kit,
- Sprockets,
- Cleaning accessories.
In addition, the AHS Field Service Technician will work with AHS Engineering to evaluate the condition of your conveyor system and provide recommendations on new advancement or retrofit kits available to maximize output.
What Is the End Goal of This Preventative Method?
The ultimate objective of adopting this preventative method is to transform the maintenance strategy within a production facility from a “break-fix” model to a proactive “preventative maintenance” approach. By collaborating closely with site personnel, the AHS Field Service Technician aims to implement an annual preventative maintenance schedule.
The transition towards preventive maintenance is designed to ensure that machinery is always operating at peak efficiency, thereby enhancing overall productivity and reducing long-term operational costs. Through this methodical approach, facilities can anticipate and mitigate potential issues before they escalate, fostering a culture of continuous improvement and operational excellence.
Duration of TPM
Implementing TPM on High-Value Hardware (HVH) systems takes a while. The standard duration of TPM is typically 8 hours. This period is dedicated to conducting thorough inspections, maintenance, and any necessary repairs to ensure that these critical systems operate efficiently and without interruption.
After Maintenance Is Done, You Will Get a Report
Upon completion of the maintenance work, clients will receive a comprehensive report crafted by the AHS Field Service Technician. This document will detail the scope of work performed, highlighting the specific maintenance tasks undertaken.
Additionally, the report will include proactive recommendations aimed at enhancing the system’s performance and reliability as part of a forward-thinking maintenance plan. This meticulous approach ensures that clients are well-informed about their system’s condition and equipped with strategic advice to prevent future issues, thereby promoting longevity and efficiency.
Continuous Improvement Is the Key to Quality Production
Embracing the philosophy of continuous improvement, the AHS Field Service Technician collaborates closely with site personnel and AHS Engineering to significantly enhance your operation’s efficiency and productivity. Through the TPM program, this partnership focuses on proactive and preventative measures designed to achieve several key objectives. By emphasizing routine maintenance and timely interventions, the initiative aims to:
- Reduce downtime,
- Maximize production performance,
- Extend the lifespan of critical capital equipment.
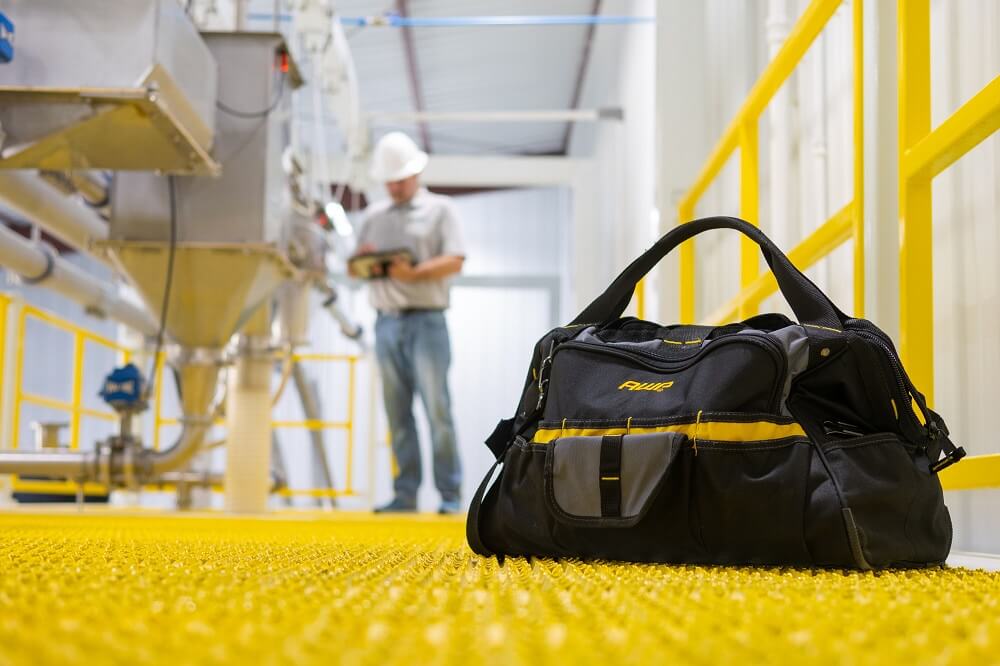
Download the Total Preventative Maintenance Brochure
Unlock the full potential of your conveyor technologies with Cablevey Conveyors’ Total Preventative Maintenance brochure. Gain access to expert insights and strategies designed to minimize downtime and boost efficiency. Click to download now and take the first step towards optimizing your operation with Cablevey’s proven maintenance solutions.
On the Quest to Find the Best Conveyor Solutions for Your Processing Facility? Contact Cablevey Conveyors
Embarking on the quest to find the optimal conveyor solutions tailored to your processing facility’s specific needs? Look no further than Cablevey Conveyors. With a legacy of excellence and innovation, Cablevey is dedicated to providing state-of-the-art conveying systems that cater to a wide range of industries.
Our team of experts is equipped to design and deliver solutions that enhance your operational productivity and sustainability. Whether you’re processing food or any bulk materials, our commitment to quality and customer satisfaction stands unparalleled. Don’t settle for less. Contact us today to explore how we can transform your processing facility with our cutting-edge conveyor engineering.
FAQ
What Exactly Is Total Preventative Maintenance (TPM) for Conveyor Systems?
Total preventative maintenance for conveyor systems is a comprehensive approach focused on preventing mechanical issues before they occur. It includes routine inspections, scheduled maintenance, and the involvement of all employees to enhance operational reliability and productivity.
How Does TPM Benefit My Production Facility?
Implementing TPM in your facility can significantly reduce downtime, maximize production performance, and extend the lifespan of critical capital equipment. This proactive strategy ensures continuous, efficient operation and reduces repair costs.
What Services Are Included in a TPM Program?
TPM programs typically include annual service inspections, replacement, and calibration of components like cable and connector kits, sprockets, and cleaning accessories. Additionally, evaluations for new advancements or retrofit kits are provided to maximize output.
How Long Does the TPM Process Take?
The standard duration for implementing TPM on High-Value Hardware (HVH) systems is typically 8 hours. This time is dedicated to conducting thorough inspections, maintenance, and any necessary repairs to ensure efficient operation.
What Happens After TPM Is Completed?
Upon completing maintenance, you’ll receive a detailed report from the AHS Field Service Technician. This report outlines the work and specific maintenance tasks performed and includes proactive recommendations for enhancing system performance as part of a forward-thinking maintenance plan.