New Research: Evaluating and Implementing New Conveyor Systems
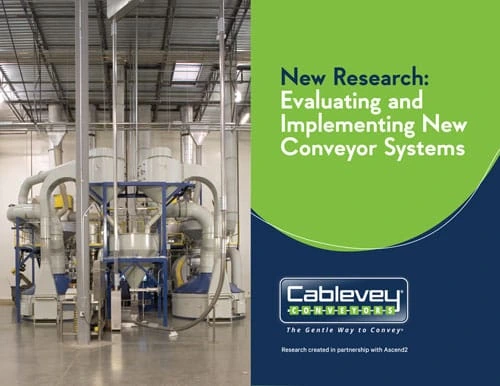
The food processing sector is witnessing a notable expansion, prompting companies to invest more effort in reviewing their current industrial conveyor systems. That’s where evaluating and implementing new conveyor systems comes into play. This standalone research project quantifies the process of selecting food conveyors by gathering insights from 290 experts within the food processing industry on essential factors to consider during a system evaluation.
Download the full report here
Introduction to Modern Conveyor Systems in the Food Processing Industry
The food processing industry is witnessing unprecedented growth, driving organizations to meticulously assess their existing systems, explore the need for new ones, and select the optimal solution tailored to their specific requirements. This surge in demand underscores the importance of bulk material handling equipment, which plays a crucial role in maintaining efficiency and productivity in food processing operations.
The Importance of Conveyor System Selection
Selecting the right conveying system – be it a pneumatic conveyor system, automatic conveyor system, or custom conveyor belt – is vital for ensuring the seamless operation of food processing plants. Systems with belts for warehouses and food-specific applications highlight the move towards more specialized industrial conveying belts. These are designed to handle specific challenges, including hygiene, efficiency, and material integrity.
Critical Considerations in Evaluating a Conveying Solution
Under the spotlight of our investigation are four crucial aspects that significantly impact the decision-making process. Each of them plays a vital role in ensuring that the selected system not only fits the immediate needs but also contributes to long-term efficiency. So, let’s check these considerations out.
Product Integrity
Ensuring the material’s integrity is essential. Systems like Cablevey Conveyors are designed to handle food products gently, minimizing damage and preserving quality.
Facility Requirements
Space constraints require innovative solutions like a tubular conveying system that can navigate complex routes without compromising performance.
Maintenance and Downtime
A conveyor belt system that demands frequent maintenance can significantly disrupt operations. Hence, selecting systems that are easy to clean and maintain is essential.
Energy and Efficiency
The operational cost is greatly influenced by the energy consumption of the conveying system. Efficient automated conveyor systems can lead to substantial savings.
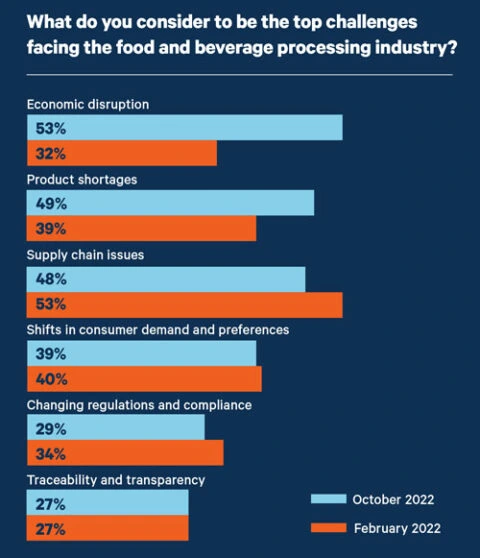
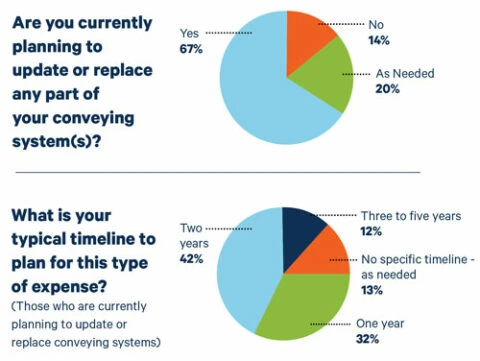
Evaluating Conveyor Technologies for the Food Industry
When delving into the specifics of these technologies, several options stand out for their applicability in the food processing sector. Here are some conveyor manufacturing solutions you should be aware of:
- Tubular Conveyor Systems – These systems offer a hygienic and efficient method for transporting materials through enclosed tubes, reducing contamination risks.
- Pneumatic Systems – Ideal for handling bulk materials, pneumatic systems transport products through air pressure, offering flexibility in routing and reducing physical footprint.
- Screw Augers – These systems are essential for moving granular or liquid materials, especially useful in tight spaces where precision is key.
- Automation Conveyor Systems – The integration of automation in conveyors enhances efficiency, reduces manual labor, and improves overall productivity.
- Bucket Elevators – Perfect for vertically transporting bulk materials, bucket elevators are a staple in handling a wide variety of products, from grains to processed foods, with efficiency and care.
How to Choose the Right Conveyor Belt for Food Processing
An automated conveyor system has become an integral component of modern food processing facilities. Selecting a conveying system with a belt for food involves considering factors like material compatibility, ease of cleaning, and compliance with food safety standards. It’s essential to choose materials like food-grade plastic, stainless steel, or certain synthetic fabrics that are resistant to corrosion and safe for direct food contact.
The conveying system should have a smooth surface to facilitate straightforward cleaning and sanitation, thereby preventing bacterial growth and cross-contamination. It should also comply with relevant food safety standards, such as those set by the FDA or EFSA. This is crucial to its suitability for food processing, emphasizing the need for high-quality equipment that meets stringent industry requirements.
Planning and Implementing Conveying Solutions
Before finalizing a conveying solution, it’s critical to engage in thorough planning and consultation with conveyor systems manufacturers. This ensures that the chosen system aligns with operational goals and facility requirements. That being said, here are some important questions to ask providers:
- What are the steps to managing an optimal layout for your conveying solution?
- How do you compare with similar conveyors for energy usage?
- How do I contact you if I have difficulty during a self-install? On the weekend?
- How much time does it take to clean your system?
- How can I tell if your conveying system is clean to the standard used in our facility?
- Will we have a dedicated account rep available to us? What days? What hours?
- Can we test our materials in your system before we buy one?
- How do we prevent downtime?
- Do you offer an ongoing maintenance agreement?
- Are replacement parts easily available? How long does it take for you to ship them once ordered?
Ensuring Seamless Operation and Maintenance
Conveyor engineering goes hand in hand with ensuring minimal downtime and efficient operation. Opting for systems with easy-to-source replacement parts and offering ongoing maintenance agreements can significantly mitigate operational risks.
The Role of Conveyor Installation Supervision
Professional installation supervision can streamline the setup process, ensuring that the system is installed correctly and operates at peak efficiency from the outset. This is a crucial step in avoiding future issues that could lead to costly downtime and repairs.
The Future of Conveyor Systems in Food Processing
As the food processing industry continues to evolve, so too do the conveyor technologies. From tubular systems to sophisticated automated solutions, the focus remains on enhancing efficiency, maintaining product integrity, and ensuring hygiene. Cablevey Conveyors is at the forefront of this evolution, offering specialized solutions that meet the complex needs of the industry.
By considering the critical factors outlined in this research and asking the right questions, food processing professionals can make informed decisions. Contact us, download the full report, and choose the right conveyor solutions. Look forward to improved productivity, reduced operational costs, and a stronger bottom line.