The prevention of dust explosions is a crucial consideration in the context of traditional belt conveyor manufacturers and automated conveyor systems. But why are dust explosions dangerous? Can a revolutionized automated conveyor system help you prevent any potential hazard? Let’s explore preventative measures and consider the role of innovative conveyor solutions, such as a cutting-edge tubular conveying system provided by Cablevey Conveyors, in ensuring not just efficiency but paramount safety in industrial operations.
Why Are Dust Explosions Dangerous?
As per OSHA’s description of combustible dust explosions, any material with combustible properties can undergo rapid combustion when finely divided. When this dust is present in the air at an optimal concentration and specific conditions are met, it has the potential to turn explosive.
When we know that 70% of material handled in the various process industries contains combustible dust, it is clear why it presents a major safety hazard for process plants. According to the data gathered by the Safety Chemical Board, combustible dust explosions have become more frequent over the past 14 years, causing severe damage to facilities and process industry equipment, as well as taking numerous lives.
Learnings from Catastrophes – Insights into Preventable Tragedies
Some of the most recent dust explosions in America have called regulatory bodies to action. One of these was the titanium explosion in West Virginia, where three employees lost their lives. The other one was a notorious sugar explosion in Georgia that completely devastated the facility, causing the death of fourteen people.
The fact about the latter incident is that it was “entirely preventable,” according to the Chemical Safety Investigation Board’s report. This report also stated that this catastrophic incident would have been avoided if safety management had applied measures to control dust explosion hazards.
This devastating sugar explosion prompted the OSHA and the National Fire Protection Association to devise a series of policies and combustible dust safety standards. Process industries need to comply with these regulations to protect their employees and equipment from severe explosions.
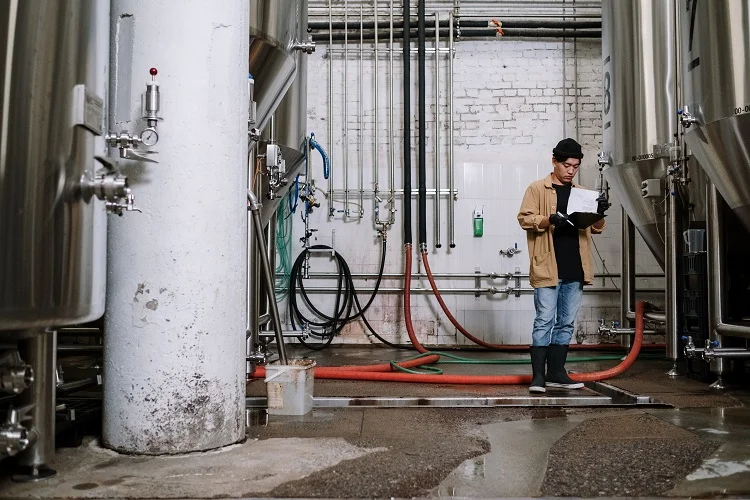
Explore the Five Factors That Lead to a Dust Explosion
Dust explosions occur when five crucial elements that form a Dust Explosion Pentagon coincide within the processing facility. The factors that facilitate such explosions are:
- Combustible dust particles (the explosion’s fuel),
- Oxygen,
- Dispersion of dust particles – when accumulated dust is lifted in the air, forming an explosive dust cloud,
- Ignition sources capable of igniting combustible dust clouds,
- Confined spaces where the pressure builds up, usually leading to damaged equipment, destroyed facilities, and potential structural collapse.
The concentration of dust plays a crucial role in the potential for an explosion. Dust deflagration, a combustion phenomenon, is only triggered at specific concentrations of combustible dust. When the minimum explosive concentration of dust is dispersed in the air within an enclosed space, particularly in proximity to an ignition source, it can result in a hazardous explosion.
Understanding the Critical Role of Dust Concentration in Explosive Events
The dust explosion progresses through two distinct phases. In the first stage, a primary dust explosion occurs within equipment such as grain elevators and dust collectors. This initial explosion is less intense compared to the subsequent wave. The swift combustion of dust particles elevates air pressure, generating a pressure wave that has the potential to disperse dust deposits into the air, ultimately leading to the ignition and occurrence of a secondary explosion.
Following the initial explosion, these subsequent explosions occur rapidly and exhibit increased violence and destructiveness, resulting in catastrophic damage and loss of life. The size of dust particles plays a role in the rapid spread of fire during the explosion.
Finer dust particles pose a higher risk as they can easily disperse through the air, possessing a larger surface area that enhances their flammability. An NFPA study demonstrated that even an accumulation of dust as thick as an average paper clip is adequate to trigger devastating explosions.
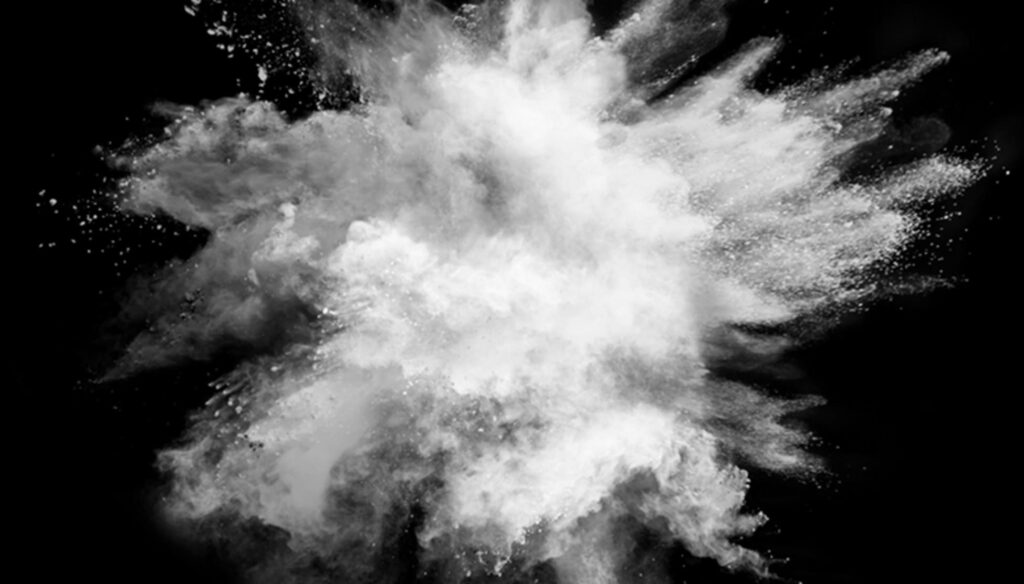
The National Fire Protection Agency Combustible Dust Safety Standards
The NFPA devised this standard, which became effective in September 2015, focusing on the measures required to control combustible dust hazards. This standard emphasizes the dust combustibility guidelines and the importance of fire or dust explosion prevention and protection in the process industry.
One of the reasons such explosions are so dangerous is that combustible dust exists in a variety of process industries, presenting a significant safety hazard. Some of these process industries are:
- Agriculture, fertilizer, grain, tobacco, food processing industries,
- Wood and paper processing, furniture, textiles, and dyes manufacturing facilities,
- The petrochemical industry, pharmaceutical components manufacturing,
- Plastic processing and recycling facilities,
- Coal mining.
As stated above, approximately 70% of dust is explosive. Also, even non-explosive materials can become explosive when mixed with sufficient organic or metal dust concentrations.
Implementing NFPA Standards for Combustible Dust Control
Understanding the practical steps necessary to adhere to NFPA standards is a must if you want to ensure the effective control and removal of combustible dust, safeguarding both personnel and infrastructure. Below are some of the NFPA standards concerning the control of combustible dust hazards:
- Minimize fugitive explosive dust to prevent its escape from processing equipment and ventilation systems. Enclosed tubular drag cable and disc conveying systems, such as Cablevey conveyors featuring fully enclosed tubes, can play a significant role in controlling and removing dust.
- Install a dust collection system and regularly monitor its proper operation.
- Identify and detect all concealed surfaces containing hazardous dust deposits within the facility.
- Establish and adhere to a cleaning schedule for all areas prone to the accumulation of combustible dust.
- Utilize cleaning methods that avoid the generation of dust clouds near ignition sources, steering clear of compressed air cleaning techniques.
- Place pressure relief valves away from areas prone to combustible dust hazards.
- Maintain a comprehensive dust control program involving frequent inspections, testing, housekeeping, and control initiatives to mitigate potential hazards.
- Isolate equipment from one another to prevent flame propagation through ductwork into other sections of the equipment in the event of an explosion. This isolation is crucial to prevent flames from spreading to adjacent equipment.
- In cases where an explosion occurs in an outdoor dust collector, ensure that it does not propagate through the ductwork into the processing facility, posing a danger to workers.
Additionally, operations that generate dust, such as abrasive blasting, grinding, or cutting, must comply with OSHA requirements.
Ignition Sources Control Is One of the Key Strategies Mitigating Ignition Risks
Ensure you explore key measures aimed at eliminating potential ignition risks and disrupting the Dust Explosion Pentagon. Understand the significance of these strategies and foster a secure workplace environment. Here are the steps you need to take:
- Employ proper installation, classification, and maintenance of all electrical equipment and wiring,
- Make sure that the equipment complies with the latest electrical safety technology standards,
- Control static electricity by implementing grounding wires or rods,
- Forbid or limit smoking and open flames inside the workplace,
- Limit or isolate sparks or friction sources,
- Limit contact between hot surfaces or heating systems and combustible dust,
- Incorporate spark arrestors or spark traps into all dust collector ductwork.
Mitigating the Aftermath – Dust Explosion Damage Control
Proactive measures aimed at alleviating the aftermath of these serious safety incidents are also a must. In case such explosions happen, make sure you have a pre-prepared strategy to alleviate negative effects and control damage caused by this serious safety incident.
- Separate the dust explosion hazard in the most efficient way possible,
- Distance it from the work environment and isolate it by placing barriers where possible,
- Install deflagration venting,
- Install pressure relief vents on applicable equipment,
- Apply ignition sources detection systems and extinguishing equipment,
- Install a dust explosion protection system, if possible.
Ensure Appropriate Workers’ Protection
While these strategies and standards for preventing dust explosions may mitigate the hazards, they are not entirely adequate in safeguarding workers from combustible dust flash fires and explosions. While certain employers may believe that providing workers with helmets, protective gloves, and ear and eye protection is satisfactory personal protective equipment (PPE) for those dealing with hazardous materials, it is crucial to recognize the insufficiency of such measures.
In contrast, the utilization of personal protective equipment like flame-resistant garments and ARC flashing clothing proves to be essential for ensuring adequate protection, particularly in the event of perilous dust explosions. Since workers are closest to hazards, they need to have adequate explosion safety training to recognize explosion risks and prevent them from happening. Employees should also be encouraged to report possibly risky working conditions.
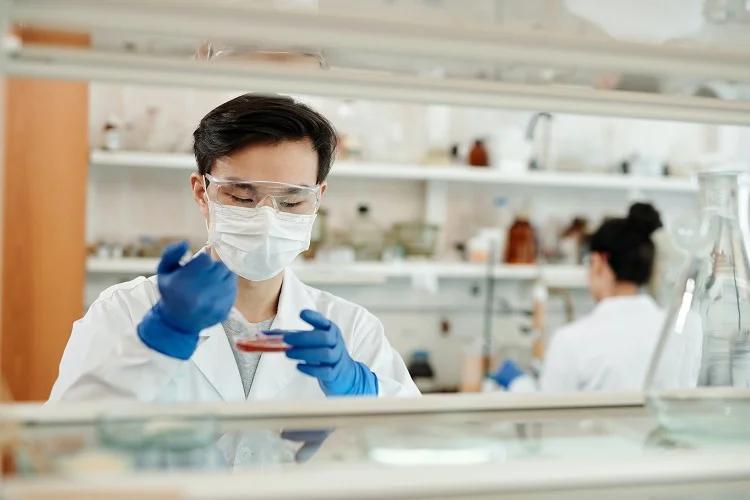
Dust Explosion Prevention – Tubular Conveyor Solutions for Dust Control
To minimize the risk of combustible dust explosions, it’s essential to focus on effective dust control measures. An automatic conveyor system, like Cablevey conveyor manufacturing with its completely enclosed tubes, proves invaluable in controlling and removing dust. Unlike a traditional conveyor belt system, these systems contribute to minimizing fugitive explosive dust and preventing its escape from processing equipment and ventilation systems.
Ensuring Conveyor Safety and Compliance
Manufacturers and operators of industrial conveyor systems must adhere to NFPA standards to protect their employees and equipment from severe explosions. This includes measures such as minimizing explosive dust, installing dust collection systems, and maintaining a comprehensive dust control program. Tubular conveying systems align with these standards, offering a safe and efficient solution for material handling while reducing the risk of combustible dust incidents.
Combustible dust explosions are dangerous safety incidents that may destroy process plants, resulting in significant loss of human lives and economic consequences. By complying with the described safety standards, you will manage the ignition sources and dust control, ensuring your employees have adequate dust explosion protection. We are proud to be leaders in gentle conveyance methods, and our dust conveyor engineering is your best choice to reduce the chances of a dust explosion when moving friable material.
Cablevey Conveyors Is One of the Conveyor Systems Manufacturers That Provides Utmost Safety
In the intricate landscape of dust explosion prevention and workplace safety, selecting the right conveyor system is paramount. Cablevey Conveyors specializes in manufacturing conveyor systems (tubular or belt conveyor system) and offering meticulous conveyor installation supervision. That way, we ensure a comprehensive approach to dust control.Our commitment to safety extends to the cleaning of conveyor belts, an essential aspect often overlooked. With state-of-the-art solutions and adherence to the highest standards, including traditional conveyor belt systems, Cablevey Conveyors stands out as a trusted name in the industry. Contact us today to elevate your workplace safety with cutting-edge conveyor systems.