How to prevent and control dust explosions is a crucial topic for industries dealing with combustible dust. In many industrial settings, dust might seem like a harmless byproduct of everyday operations. However, under certain conditions, this unassuming dust can lead to catastrophic explosions, posing serious threats to both human safety and property.
How to Prevent and Control Dust Explosions
Dust explosions are severe safety issues affecting process industries that handle materials that generate combustible dust. According to the data collected by the US Chemical Safety Board, explosions of dust are frequent incidents. They may cause fatalities, severe injuries, and catastrophic damages to facilities, leading to considerable economic loss. For this reason, the Occupational Safety and Health Agency joined forces with the National Fire Protection Association and devised a series of safety measures and standards for safety professionals to implement in order to prevent, mitigate, and control explosive dust.
First of all, let’s discuss the difference between “prevention” and “protection.” Prevention focuses on recognizing dust explosion hazards and eliminating them before a dust explosion happens. Once the incident occurs, it is essential to protect people and machinery from potentially devastating flash fires, fires, and combustible dust explosions. The fact that 70% of dust found in a wide variety of process industries is combustible emphasizes the importance of implementing adequate dust explosion prevention, protection, and control measures.
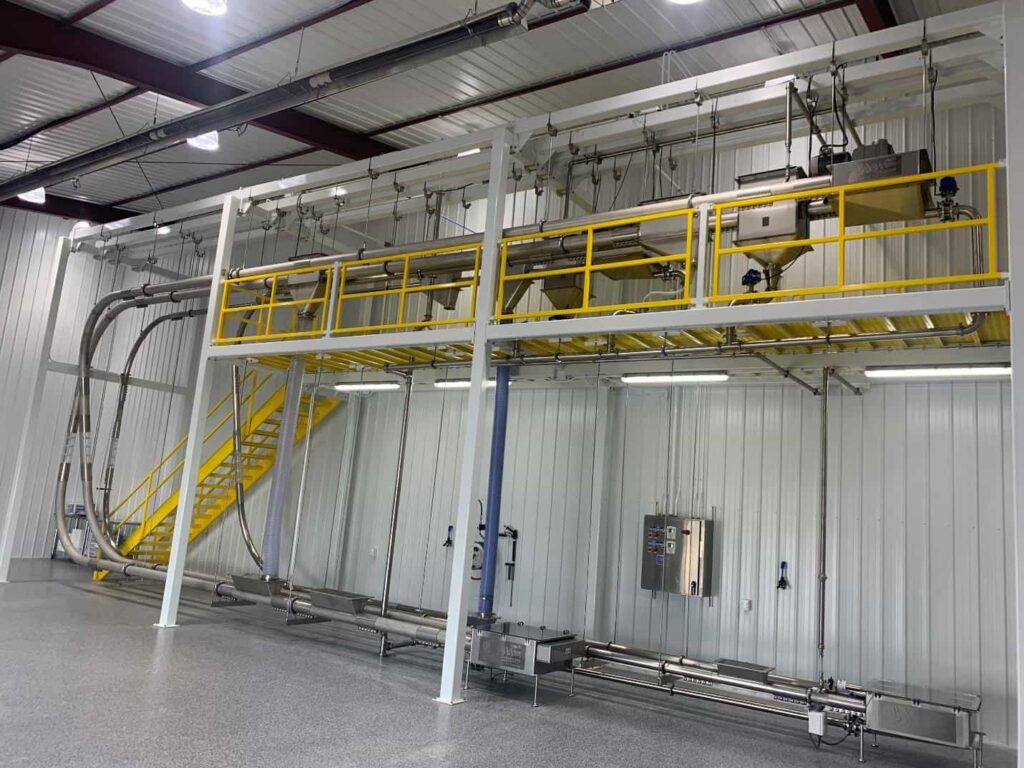
How Dust Explosions Happen and Develop
Dust explosions occur when a specific set of conditions align, forming what is known as the Dust Explosion Pentagon. These conditions include:
- Combustible dust particles – these serve as the fuel for the explosion.
- Oxygen is present – a key component for combustion.
- Dust dispersion – this occurs when dust accumulates and is then suspended in the air, creating an explosive cloud.
- Ignition sources – these are capable of igniting the combustible dust clouds.
- Confined spaces – here, pressure builds up, leading to ruptures, destruction of facilities, and potential structural collapses.
The concentration of dust is also a crucial factor in determining the likelihood of an explosion. Only certain concentrations of combustible dust can cause a deflagration. Insufficient dust concentrations won’t sustain an explosion, while high concentrations can reduce oxygen levels, inhibiting combustion. A dangerous explosion happens when the minimum explosive level of dust is dispersed in the air near an ignition source within an enclosed space.
The Phases of Explosions
These explosions occur in two phases. Initially, a primary explosion occurs within a piece of equipment, which is typically less intense than the subsequent wave. The rapid combustion of dust particles increases air pressure, creating a wave that can disturb accumulated dust on surfaces, leading to a secondary, more dangerous, and devastating explosion. These secondary explosions, occurring shortly after the primary ones, can cause catastrophic damage and loss of life.
The size of dust particles also plays a role in the speed of flame propagation during a dust explosion. Finer particles are more hazardous as they disperse more easily in the air and have a larger surface area. Research by the NFPA has shown that a layer of dust as thick as an average paper clip can lead to devastating explosions.
In industrial settings, especially those involving conveyor systems like conveyor belts, tubular conveyor, disc conveyors, and automated conveyor systems, the risk of dust accumulation and explosions is significant. Conveyor manufacturers and those involved in conveyor engineering and manufacturing should prioritize NFPA recommendations to prevent such explosion sequences.
Regular cleaning of conveyor belts, proper installation and supervision, and adopting conveyor solutions that minimize dust accumulation are essential in keeping these events under control. Conveyor technologies and manufacturing conveyor systems need to incorporate safety measures to mitigate dust explosion risks in industries utilizing belt conveyor systems, tubular conveying systems, and automatic conveyor systems.
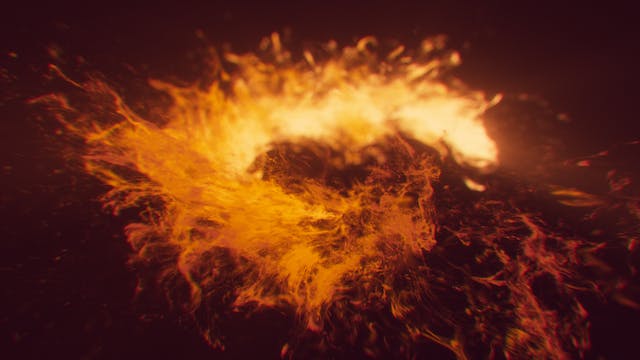
How to Avoid Second Dust Explosion Escalation
According to the NFPA, you need to take the following steps to avoid dust explosion escalation that may leave irreparable damage and endanger people’s lives. To enhance safety in industrial settings, it’s crucial to isolate each piece of equipment from others. This isolation is vital to prevent the spread of flames through ductwork in the event of an explosion.
Specifically, in scenarios where an explosion might occur in an outdoor dust collector, measures should be taken to ensure that flames do not travel back through the ductwork into the main processing facility, thereby posing a risk to workers. This strategy of containment is key in managing risks associated with conveyor belt systems, belt conveyor manufacturers, and automated conveyor system environments. By implementing these safeguards, facilities can better protect against the spread of fires and explosions, particularly in areas with extensive conveyor installation or conveyor belt systems.
Second, safety professionals need to be aware of the “fugitive” dust particles hazard. These are particles that escape the processing and conveying equipment, settling on visible or hidden horizontal surfaces. Implement the following measures to avoid fugitive dust accumulation. Check whether all ducts are airtight and make sure the dust cannot escape when the machine starts working. Select a hood that captures dust properly and diverts it into the dust collector. Finally, effective and regular cleaning plays a crucial part in keeping the accumulated fugitive dust below the minimum explosible levels.
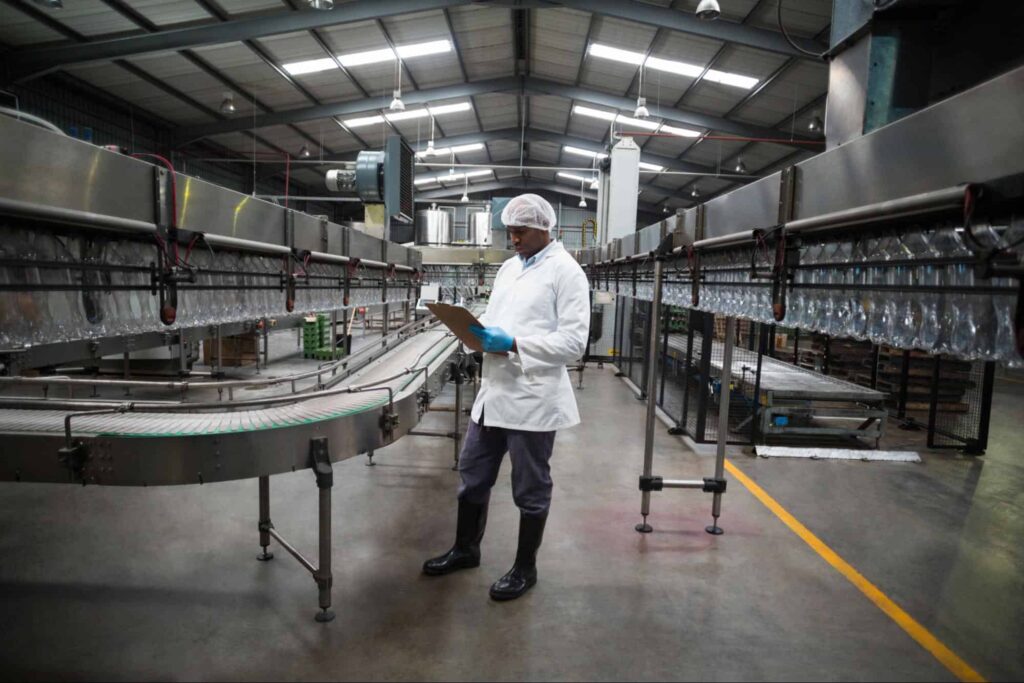
How to Comply with the NFPA Combustible Dust Standard
Apart from these recommendations, the NFPA has devised a 9-step plan you need to implement to further ensure explosion prevention, protection, and control.
- Identify the combustibility and the explosibility level of the materials you are handling.
- Detect and assess fire, flash fire, and explosion hazards.
- Pay attention to the safety of building and equipment design, housekeeping, personal protective equipment (PPE), dust control, explosion prevention, protection, and explosion isolation when managing these combustible dust hazards.
- Enhance housekeeping procedures and do not apply cleaning methods that involve compressed air.
- Try using effective dust collection systems.
- Use venting systems that comply with the NFPA 68 standard and direct exhaust air outside.
- Make sure that all central vacuum systems are grounded and contain attachments made of static dissipative materials.
- Devise MOC (Management of Change) procedures you should implement before changing the materials, equipment, technology, or work tasks.
- Educate all employees about hazards and train them on protective measures
How to Ensure Explosion Prevention
To effectively prevent hazardous dust explosions, it’s essential to remove at least one element of the Dust Explosion Pentagon. Here are some strategies that can be implemented in the process industry to mitigate explosion risks:
- By transferring combustible dust storage outside of the processing facility, you can remove a primary explosion hazard.
- Maintaining dust levels below the minimum explosible concentration is key. This can be achieved through regular cleaning or using equipment designed to prevent dust accumulation, like advanced industrial conveyor systems, automated conveyor system solutions, or specialized cleaning conveyor belts.
- Introducing an inert gas such as nitrogen into confined spaces can effectively reduce oxygen levels, thwarting the possibility of an initial dust explosion. This approach is particularly crucial in environments with a tubular conveying system or an enclosed belt conveyor system.
- Identifying, controlling, and eliminating potential ignition sources is critical. These sources can range from overheated machinery parts to embers entering dust collectors. Monitoring for heat, radiation, or smoke can help identify these risks. Upon detection, implementing control measures like an abort gate in the conveyor belt system or a suppression system can prevent the ignition source from triggering a flash fire or a primary dust explosion.
- Activities like welding and cutting can generate sparks, posing significant risks in dusty environments. Therefore, it’s imperative to either clean up dust accumulations or relocate the equipment away from these areas before commencing hot work. This precaution is vital in facilities with conveyor installation, conveyor engineering, or where manufacturing conveyor systems are present.
Incorporating these strategies, especially in settings with various conveyor systems, such as tubular conveyor, disc conveyors, and automatic conveyor systems, is crucial. Conveyor manufacturers and those involved in conveyor installation supervision must prioritize these safety measures to ensure a safer industrial environment.
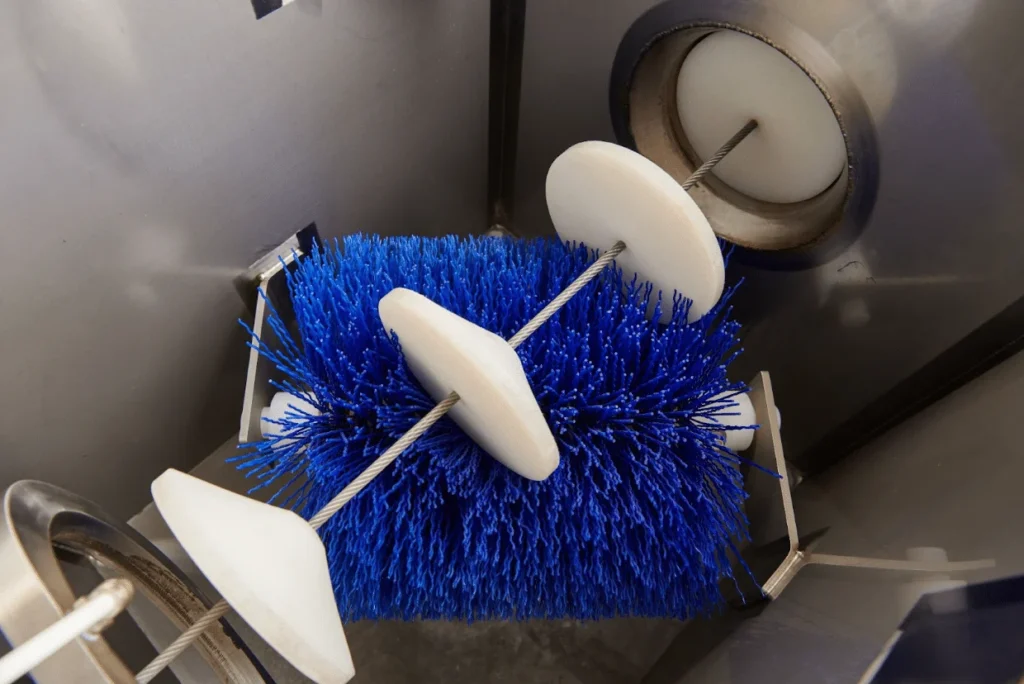
How to Protect Workers
Unfortunately, combustible explosions of dust and fire have become common safety incidents in the processing industry over the years, taking numerous lives and leaving many workers with severe injuries. For example, 14 workers lost their lives, while 36 were injured, in a devastating explosion in a sugar refinery in Georgia in 2007.
Even though these explosion prevention strategies may reduce dust explosion hazards, they cannot sufficiently protect workers exposed to combustible dust flash fires and explosions. On the other hand, personal protective equipment, like flame-resistant garments and ARC flashing clothing, will offer adequate protection in case of dangerous explosions.
Another way to protect the workforce in process plants is to eliminate the risk of static electricity. Static electricity can be a dangerous ignition source for fine dust in grain elevators or coal dust explosions that can regularly occur. You can eliminate this explosion risk by applying grounding devices devised to prevent static electricity from building up and control static charges in dusty environments.
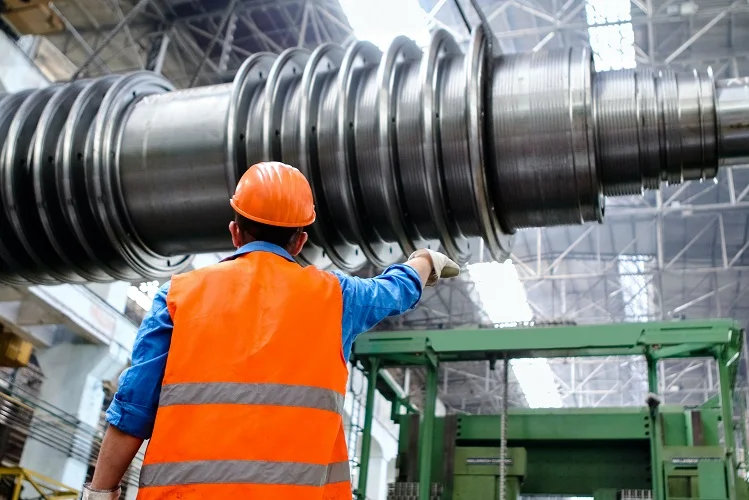
How to Protect Facilities
Once the explosion has started, you can try to increase the confinement. You will achieve this by applying explosion-proof drum kits to a dust collector bottom because these do not need an isolation channel between them. In cases of explosions in hammer mills, the equipment is durable enough to withstand the explosion inside.
Use a Dust Explosion Venting System
The pressure relief venting system is designed to open at a set pressure. When an explosion happens, building up pressure to the predetermined level, the vents open, releasing the pressure into the surrounding area. Bear in mind that the location is essential when applying these traditional venting systems. They should never be directed towards areas where workers are present. You should never place venting systems close to walls where the pressure cannot escape the confinement. Flameless venting is similar to removing the confinement process. Here, you apply mass to quench the flame and prevent it from escaping through the vent panel. This way, flameless venting simultaneously quenches and diverts the fire.
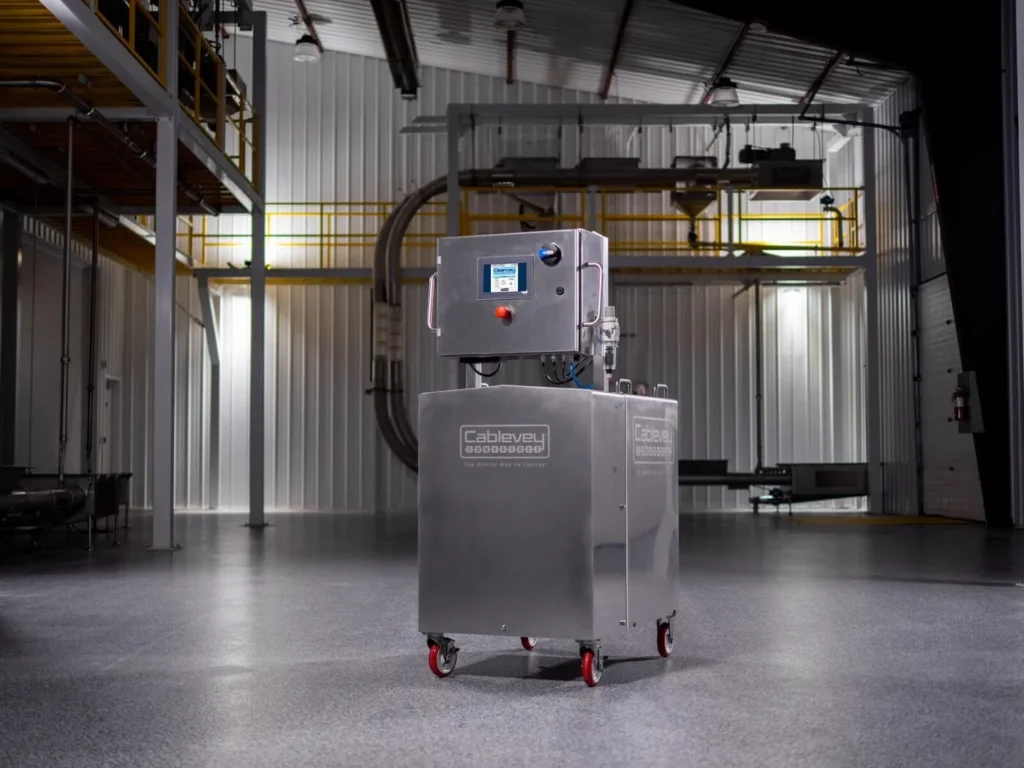
Ensuring Safety Through Compliance and Advanced Conveyor Solutions
Combustible explosions are severe safety incidents that may have devastating consequences. Suppose you implement and comply with the dust explosion standards devised by NFPA and OSHA. In that case, you may conduct a dust hazard analysis to control, prevent, and protect workers and processing facilities. Handling combustible material is a demanding task, and tubular drag cable conveying systems can prevent fugitive dust from escaping the equipment and accumulating on surrounding surfaces.For example, Cablevey Conveyors systems, with their completely enclosed tubing, prevent dust from escaping the system and settling in the working environment while ensuring a high level of dust removal due to the variety of cleaning methods. If you want to upgrade your facility’s safety and efficiency with Cablevey Conveyors, contact us today to explore our range of advanced, dust-minimizing conveyor solutions tailored to your specific industrial needs.