The conveyor system is the silent workhorse in many industries, efficiently moving products and materials and ensuring operations run smoothly. But like all equipment, it isn’t immune to wear and tear. So, when is the right time to upgrade your conveyor system? No matter if it’s a chain or belt conveyor system, be sure you’ll discover the signs that your equipment needs a revamp and the advantages of making that timely switch.
In this blog post, we’ll explore these paths in more detail and help you decide which is the best option for your facility.
When Is the Right Time to Upgrade Your Conveyor System?
How satisfied are you with the conveyor belt system in your production facility? According to our State of Conveying survey, over half of respondents (62 percent) are not completely satisfied with their current system. That’s a big number, especially when you consider that well-functioning equipment is crucial to keeping your production line moving.
What goals does a conveyor need to achieve for it to be successful? Aside from the very basic goal of transporting materials from Point A to Point B, these systems also need to be:
- Reliable,
- Flexible,
- Efficient,
- Safe,
- Sanitary.
If your conveyors aren’t ticking all of these boxes, it shouldn’t be a surprise that you may not be entirely happy with their performance. So how can a material handling system be improved? There are two main paths to go about this: making changes to the existing systems or getting a new one altogether.
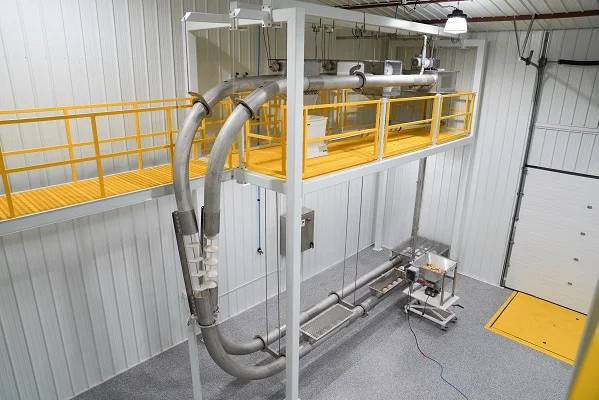
Is Improving Your Existing Conveyor System a Good Choice?
There are many reasons why you may not want or have the option to get brand-new equipment. Maybe you’ve only recently installed the system, and it’s still under warranty, or you may not have the budget for a completely new installation.
In these cases, you might be wondering how your existing conveyor system can be improved. Let’s take a look at five steps to improve your material handling setup without starting from scratch.
Evaluate Your Existing System
The first step is to closely examine your current conveyor system and identify areas that could use some improvement. Are there certain sections that are consistently causing problems? Do you need to transport different or larger products than before? Are there points in the line where materials tend to get held up?
Be precise as possible in your assessment. Collect numerical data, such as how often a line needs to be stopped for maintenance, how much time is lost due to downtime, and how much of the product is damaged during transport. These numbers will provide a solid starting point for measuring the effectiveness of any changes you make.
Consider the Design Changes You Can Make
Even when you can’t afford to replace an entire conveyor belt for a warehouse, there may be some room for design changes. These could include:
- Altering the shape or width of the belt, tube, or other parts of the system,
- Changing the angle of incline or decline,
- Redesigning how products are loaded onto or taken off the conveyors,
- Adding or removing curves.
These are just a few examples, but even small changes in the conveyor design can have a big impact on performance. Refer to the starting data you gathered in Step 1 to see which areas might benefit most from these design changes.
Be precise as possible in your assessment. Collect numerical data, such as how often a line needs to be stopped for maintenance, how much time is lost due to downtime, and how much of the product is damaged during transport. These numbers wi
Introduce a Preventive Maintenance Program
Preventive maintenance is key to keeping any machinery, including conveyor systems, running smoothly. By catching small issues before they become big problems, you can avoid unplanned downtime and save a lot of money in the long run.
A preventive maintenance program for your conveyors should include:
- Regular inspections,
- Belt or chain tensioning,
- Lubrication,
- Belt tracking.
And remember – the main goal of this type of maintenance is to prevent problems before they happen, so don’t wait until something goes wrong to start your program!
Keep Things Clean
One often-overlooked aspect of conveyor maintenance is cleanliness. A buildup of dust, dirt, and other debris can cause all sorts of problems, from clogged bearings to misaligned pulleys. Not to mention, it can also be a safety hazard for your employees. Make sure that your conveyor system is regularly cleaned to keep it running smoothly and safely.
Just as you would implement a preventive maintenance program, you should also have a cleaning schedule in place to keep things clean and tidy. This is especially significant if your business is in an industry where sanitation is a top priority, such as food processing.
Improve Environmental Conditions
Sometimes it is not the industrial conveyor belt system itself that needs to be improved but the conditions in which it is operating. Excessive dust or fumes and extreme temperatures and humidity can all take a toll on your system – and your product.
If you suspect that poor environmental conditions are causing problems, there are a few things you can do:
- Install air filtration or ventilation systems,
- Keep the area around your conveyors clean and free of debris,
- Use enclosures or covers to protect your system from the elements,
- Monitor temperature and humidity levels, and make changes as necessary,
- Making even small changes to the environment in which your conveyor operates can have a big impact on its performance.
Invest in High-Quality Conveyor Components
Lastly, one of the best ways to improve your equipment is to invest in high-quality components. This includes everything from the belt, chain, cable, or rollers to the bearings, motors, and pulleys.
When you use high-quality components, you can be sure that your system will run more smoothly and with fewer issues. Not to mention, it will also last longer – saving you money in the long run.
When Is Upgrading Your System a Must?
Sometimes, even when you do everything right, your system might still need an upgrade. Our research report states that 46% of production facilities are planning on upgrading or replacing their conveyor systems in the next one to two years.
An additional 34% plan to upgrade or replace their conveyors in the next three to four years. Here are some undeniable signs that it’s time to invest in your system:
Capacity and Energy Efficiency Issues
If your conveyors are often overloaded or idle, they may be misaligned with your business’s current demands, indicating a potential need for an upgrade. Whether you’re handling more products than before or wasting funds on excess capacity, a properly sized system can streamline your operations. Examine your system against production needs to identify discrepancies.
Two key motivations for upgrading to a more energy-efficient conveyor are cost savings and environmental considerations. Modern systems incorporate features like variable speed drives, automation conveyor systems, and energy-efficient motors to minimize energy use. An upgrade can reduce energy expenses and your company’s carbon footprint.
High Maintenance, Repair, and Overall Costs
Excessive maintenance and repair costs can be indicative of pneumatic conveyor systems’ need for replacement. While periodic upkeep is expected, constant breakdowns and accumulating downtime expenses signal inefficiency. Investing in a new system not only enhances reliability but often includes a warranty, providing added assurance.
Although the initial cost of the new conveyors might be significant, it can lead to long-term savings by reducing energy, operational, and maintenance expenses. If your system’s overall expenses outweigh its benefits, it’s worth considering an upgrade for better long-term value.
High Levels of Material Degradation
Keeping your raw materials and intermediary and finished products intact is crucial to maintaining a high level of quality in your production process. Unfortunately, custom conveyor belt systems can sometimes contribute to material degradation. If your system is causing too much wear and tear on your products, it’s time to upgrade it.
There are a few different ways to tell if the conveyors are damaging your materials:
- You regularly have to replace damaged products,
- Your product quality is suffering,
- There is an increase in customer complaints.
If any of these sound familiar, it’s time to take a closer look at your conveyor system. You might need to switch to a different type of equipment or add additional features to prevent further damage.
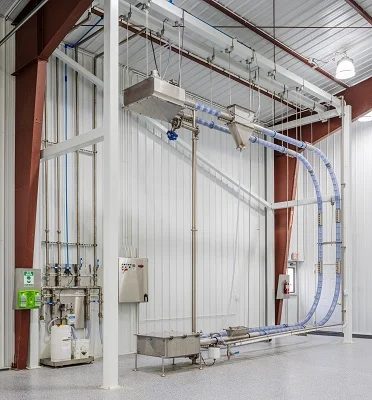
Getting a New Conveyor – What to Consider?
Maybe you’ve already tried some of our recommended ways to fix common conveyor problems. Maybe despite your best efforts, your conveyor system is still struggling. If it’s time for new equipment, there are a few things you should keep in mind during the selection process.
Conveyor Type
First and foremost, you need to decide on the type of conveyor system that will work best for your needs. Too often, businesses choose equipment based on what they already use or what they think is the most popular option.
But, there is no one-size-fits-all when it comes to conveyors. The type of system you need will depend on many factors – including the products you’re conveying, the production process, the environment, and bulk material handling equipment.
Here are some of the questions to ask when choosing conveyors:
- What type of product will you be conveying?
- How heavy is the product? What is its size, weight or bulk density, flowability, abrasiveness, and moisture content?
- Is the product fragile?
- How fast does it need to move?
These are just a few of the things you need to consider. Once you have a better understanding of what type of product you’ll be conveying and the required speed, you can narrow down your options.
Conveying or Feeding
Conveyors can perform two basic functions – conveying or feeding. As the name suggests, conveyors are primarily used for moving products from one point to another. But in some cases, they can also be used for feeding products into other machines or processes. Conveying includes moving products at a fixed rate that is not process-critical, meaning the equipment has a maximum and minimum range but can operate anywhere within that range.
Feeding, on the other hand, is used to meter product into another process at a controlled rate. This might be done with a variable-speed conveyor or by adding an indexing feature. Feeding makes it possible to control the product’s arrival at the next process, which is critical in some cases. Depending on your needs, you might use conveying or feeding conveyors – or a combination of both
Conveyor Cleaning and Maintenance
We’ve already established that one of the main reasons to upgrade your tubular drag systems is to reduce maintenance and cleaning costs. But it’s worth mentioning again because it’s such an important factor in the decision-making process. In fact, our State Of Conveying survey revealed that 34% of respondents said that ease of cleaning is one of the top priorities when choosing a new system. 28% mentioned minimizing maintenance costs.
Cleaning and maintenance costs can be reduced in a number of ways – by choosing a conveyor with fewer parts, using corrosion-resistant materials, or adding features that make cleaning easier. For example, some conveyors come with clean-in-place (CIP) mechanisms that allow for cleaning without disassembly.
Others might have an open-frame design that gives operators better access to the product-contact parts of the conveyors. When considering a new system, be sure to ask about the cleaning and maintenance requirements. This will help you compare the true cost of ownership for each option.
Safety and Sanitary Guidelines
Regardless of the industry you’re working in, there’s always a risk of injury when operating machinery. That’s why it’s important to consider safety when choosing new equipment. The good news is that there are many ways to make conveyors safer – from adding guarding to using sensors and other safety features.
If you’re using a conveyor belt for food, you’ll also need to consider sanitary guidelines. The U.S. Food and Drug Administration (FDA) and the USDA have established strict regulations for conveyors used in food processing facilities.
To ensure your equipment meets these guidelines, look for a system made of stainless steel or other non-corrosive materials. The tubular systems should also have smooth surfaces designed to minimize the risk of product contamination and cross-contamination.
Budget Limits
Lastly, you’ll need to consider your budget when choosing a new tubular system. Conveyor systems can vary vastly in price. The cost will depend on the type of equipment, the material it’s made of, its features, and more.
To get an accurate estimate of the cost of a new conveyor system, be sure to get quotes from multiple suppliers. And don’t forget to factor in installation, training, and ongoing maintenance costs. Calculate your return on investment (ROI) to make sure upgrading is a wise decision for your business. If the ROI is positive, upgrading your conveyors is a sound decision.
The Future of Your Tubular Drag Conveyors
Making a decision to upgrade your conveyors is not always easy. However, if you take the time to consider all of the factors, such as whether your existing system is at capacity, how easy it is to clean and maintain, and whether it meets safety and sanitary guidelines, you’ll be able to make the best decision for your business.Before taking the leap, reflect on the conveyor type you need, maintenance requirements, budget, and safety compliance. The right choice, made with foresight, can stand as a steadfast ally in your business journey for the long haul. And if the path feels overwhelming, remember, we at Cablevey Conveyors are just a call away, ready to guide you to perfect tubular drag conveyors for your enterprise.