Established following the federal legalization of hemp through the Hemp Farming Act of 2018, the US cannabis and hemp industry is relatively new. With growing interest in legal hemp production, it’s important to highlight the best processing environment for hemp products. Find out all about this topic and boost your manufacturing processes.
What Is the Best Processing Environment for Hemp Products?
The ideal processing environment for hemp products involves a climate-controlled facility with proper ventilation, protection from direct sunlight, and modern equipment such as a tubular conveying system to ensure cleanliness, prevent contamination, and maintain product integrity.
The hemp plant is grown for fiber production, seed production, wholesale hemp biomass, and hemp oil for use in a wide variety of products. From textiles and rope to building materials, industrial hemp can be incorporated into thousands of products.
Because hemp varieties like hemp seeds are categorized as food, this means that food and drug administrations have enforced rules and regulations on hemp and hemp-derived products, particularly CBD hemp.
Navigating Regulatory Challenges in Hemp Cultivation and Processing
As already mentioned, only after the Hemp Farming Act of 2018 did the plant become legalized. This means that many of those that grow industrial hemp and hemp processing facilities in operation today are still in the learning process.
Best practices are still being established as hemp cultivators and processors understand more about the different factors and conditions. It’s because these may enhance or weaken the integrity of the product. Beyond streamlining processes, the equipment for processing continues to evolve to reduce wastage and product loss while improving efficiency and product quality.
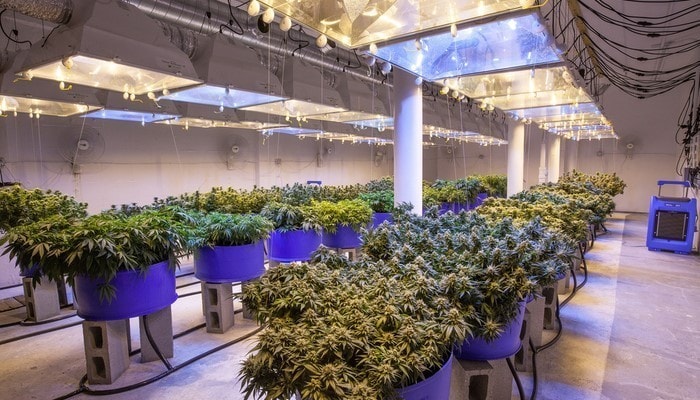
Preparing Hemp Materials for Storage or Processing With Conveyor Technologies
Traditionally, industrial material is grown outdoors, while hemp cultivated for the purposes of producing medical hemp or CBD products like CBD oils, CBD extracts, CBD distillate, or hemp seed oil are grown indoors in greenhouses.
To understand the best processing environment for hemp products, belt conveyor manufacturers must also consider the environment the crop is coming from and where it’s being stored. The climatic difference between geographic locations can mean that crops in one state will suffer from too much humidity and rainfall, while hemp farmers in another state will worry their harvest is not getting enough moisture.
Conveyor Systems Manufacturers Tailor Harvesting and Drying Protocols for Optimal Hemp Quality
Each processing facility will likely have its own processes and controls when it comes to harvesting, drying the plant material, and storage. Drying hemp thoroughly before storage or moving it to a processing facility with a tubular conveyor is a crucial first step to reducing the risk of mold growth and maintaining the integrity of the plant material.
Hemp harvesters and processing facilities do this with approaches like environmentally controlled barns, aeration, and heated air dryers. If the harvested plant is not dried quickly enough, moisture will not only encourage mold to spread but also become contaminated with fungi and bacteria. The same can happen when the hemp is harvested too wet.
The Characteristics of a High-Level Hemp Processing Facility and Conveyor Solutions
As the industry grows and evolves, we learn more about hemp cultivation, processing, and manufacturing practices. However, there are hemp processing facilities in operation today that have set the bar high by investing in the best technology and equipment and implementing strict processes and controls (such as cleaning conveyor belts). Here are the characteristics of a high-performing hemp processing plant.
Climate-Controlled Storage
Adequate moisture content is crucial when growing hemp crops. However, in storage or during processing, too much moisture can threaten all your stored products. Mold loves to grow in damp places. And because of the way mold reproduces, it will send more airborne spores to find more places to grow and spread, potentially ruining hundreds of thousands, if not millions of dollars worth of products.
So, when the processing facility is climate-controlled with minimal to non-existent temperature shifts, the threat of mold is reduced significantly. It’s important to note that too little moisture can also threaten the integrity of the product. Therefore, mitigating degradation of the harvest also means checking humidity levels constantly to ensure the hemp’s moisture content is stable and not too high, which can allow the growth of mold.
Well-Ventilated With a Quality Filter System
Whether it’s an extraction facility or processing plant, air movement and carbon filtration are paramount. Ventilation ensures the air doesn’t become stagnant, which results in pathogens like mildew. As mentioned, mold spreads through airborne spores that seek damp places to grow and reproduce. This is why processing facilities shouldn’t just be climate-controlled but should also take special precautions to maintain the quality of the product.
Well-ventilated hemp processing facilities help reduce the risk of uneven distribution of heat and humidity. They also prevent pest infestations, like spider mites, and the spread of bacteria. Proper ventilation is also important for the health and safety of the people working in the hemp processing plant.
Protection From Direct Sunlight and the Elements
Exposure to extreme temperatures and ultraviolet light can cause a healthy harvest to degrade. So, not only is the best environment for hemp processing climate-controlled with high-quality filters and ventilation systems, but it should also be in an enclosed space that protects the product from direct sunlight, extreme heat or cold from the outdoors, and elements that may break down the delicate parts of the hemp plant like its buds and seeds.
Consider Modern Equipment Like an Automatic Conveyor System
Beyond a highly controlled facility with a state-of-the-art filter and ventilation system, the equipment being used for processing should also be designed to be dust- and contamination-free. This is why it’s not ideal to use traditional equipment like conveyor belt systems, screw augers, bucket elevators, and pneumatic and vacuum conveyors when moving industrial hemp materials around the facility.
These types of conveying systems either have poor inlet designs or speeds that are so high that they cause the materials to separate or break, leading to degradation. They are also prone to temperature changes, which may cause the fragile parts of the hemp plant to break down due to heat and friction.
Choose the Top Conveyor Engineering Option on the Market
Automatic tubular drag conveyor systems don’t only work more efficiently at moving delicate materials such as hemp seeds, pellets, and biomass – they were also designed to keep dust and contaminants out. Modern tubular drag conveyors have stainless-steel tubes made with either nylon or UHMW discs that have no screws or bolts where particles may accumulate. To maintain the utmost cleanliness, even its connectors are made of stainless steel. The system will likely have removable parts for easy cleaning or can be cleaned in place (CIP).
Because the tubular drag conveyor system has an enclosed tube for moving materials, hemp material is kept clean and safe, no matter where they are conveyed within the facility. This not only maintains the integrity of the product but ensures there is no spillage or product loss.
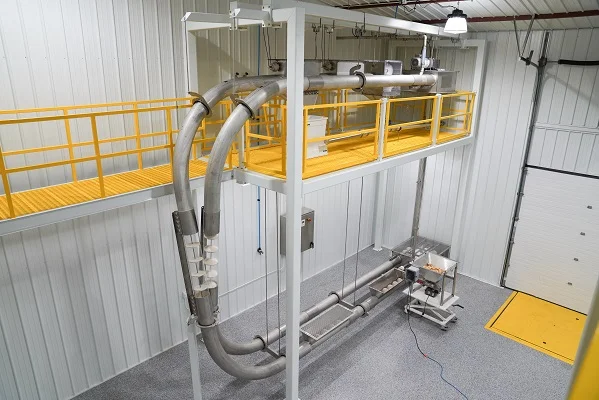
Cablevey Automated Conveyor System Is Your Top Choice for Hemp Processing
As the stigma surrounding cannabis and hemp decreases, more entrepreneurs perceive hemp as an economic crop and want a piece of the multi-billion dollar industry. However, as industrial hemp programs are still in their infancy in most states, the industry still needs some time to grow and establish whether or not the processes and controls they’ve put in place are enough.
To compete in the hemp marketplace, business owners need to be prepared to invest in advanced technology and equipment to ensure they are processing hemp appropriately. This requires the best environment for processing and reliable industrial conveyor systems.
Contact Cablevey Conveyors and check out why we’re the number one choice in the hemp conveying industry. We’ll ensure your products are safely transported from point A to point B without risking their integrity.