Industry Outlook and Challenges
The food processing industry faces a dynamic landscape marked by
both promising opportunities and significant challenges. The 2nd year
of The State of Conveying highlights some of the trends so that you
can better plan for the future.
Industry Growth Continues
The food processing industry is rapidly growing, with 63% having
grown 10%+ in the past year (20% grew 20%+). This mirrors the
growth from 2022 and indicates a long-term trend for the industry. As
the industry grows, it is now more important than ever for industry
decision-makers to ensure their operations are optimized to handle
current and future growth.
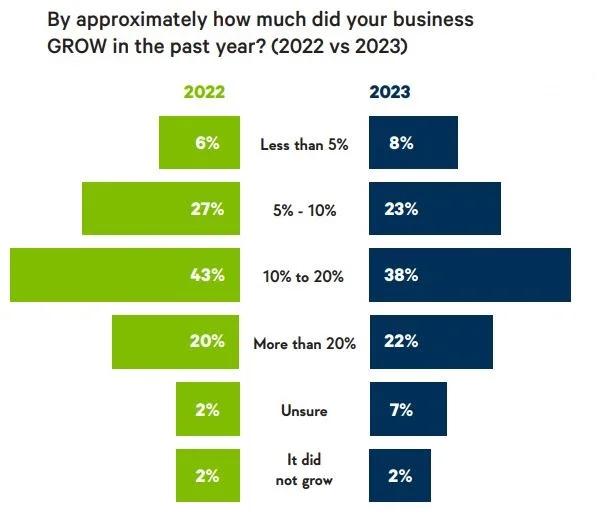
Supply chain issues (49%) continue to be the top challenge in the food processing industry and shifts in consumer demand and preferences (46%) are a close second. Shifts in consumer demand and preferences experienced a significant jump from 2022, indicating the need for organizations to be agile with their ability to adjust production lines to meet demand.
Industry Challenges by Region
Supply chain issues: 52%
Economic disruption: 46%
Shifts in consumer demand and preferences: 45%
Supply chain issues: 55%
Economic disruption: 49%
Shifts in consumer demand and preferences: 38%
Supply chain issues: 45%
Economic disruption: 44%
Shifts in consumer demand and preferences: 38%
Supply chain issues: 62%
Economic disruption: 45%
Shifts in consumer demand and preferences: 42%
What do you consider to be the TOP CHALLENGES facing the food and beverage processing industry?
- 2022
- 2023
Cleaning and Maintenance of Systems
Cleaning and maintenance is the primary challenge for food processing professionals, so this section takes an in-depth look at the topic.
Facilities Update Conveying Systems to Improve Maintenance Issues
Maintenance issues are the most commonly reported reason behind updating
conveying processes according to those surveyed (59%), above overall cost to operate and energy consumption (both at 45%). This highlights the importance of minimizing maintenance issues as well as the long-term cost of maintenance.
Budgets for Maintenance are Increasing
Budgets reflect the importance of maintenance to food professions, as 81% of budgets dedicated to conveying equipment and maintenance will be increasing in the coming year. About one-quarter (24%) describe this increase as significant.
Budget growth by region
Increasing significantly in order are Brazil 27%, Mexico 25%, U.S. 24%, and UK 15%
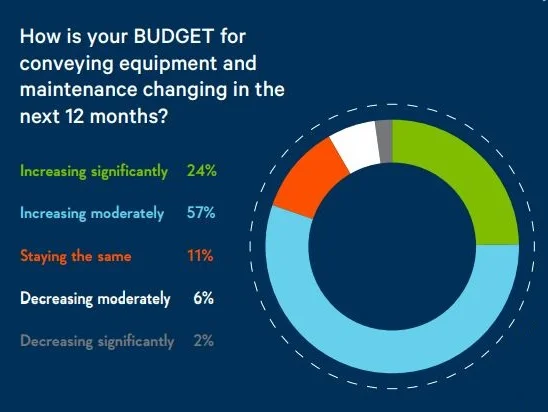
Cleanvey – A New CIP
(Clean-in-Place) Solution
- Automate the wet cleaning process. Getting rid of some manual labor and reducing the risk of improper cleaning.
- Data logging all critical information. Easily and hassle-free store cleaning times and key cleaning measurements (temperature, water used, chemicals used, etc)
- Store and use cleaning recipes for multiple systems that can be implemented with the touch of a button
Reasons for Cleaning Your System
The goal is to minimize the time spent on maintenance but
maintenance cannot be eliminated. What are the most common reasons for cleaning a system?
Routine maintenance, material build-up, and FDA sanitary compliance are the top reported reasons for cleaning according to 63%, 62%, and 61% of those surveyed, respectively.
Cleaning and maintenance are the top reasons why companies
evaluate their systems and begin the purchase process, but there
are a lot of steps to consider when making a critical and long-term
purchase decision. The food processing professionals surveyed
revealed interesting insights into the purchase process
Always Evaluate Your System
The purchase process starts with companies evaluating their current conveying system. Conveying systems are getting evaluated frequently. 43% say they evaluate every month and another 46% say they evaluate every 3 – 6 months.
Every Month Evaluations: Brazil (58%) and Mexico (53%) have the most frequency with their system evaluations.
How frequently do you EVALUATE
the performance of your conveying system(s)?
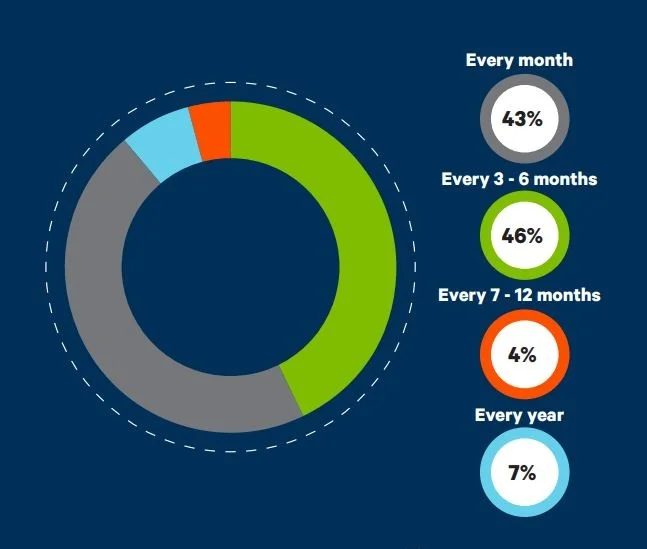
Ranking the Types of Systems
What systems are most effective at gently conveying food? In 2022, cable and disc conveyors were the clear top choice with food processing professionals when it comes to the system that is the most effective at gently conveying materials like coffee, nuts, and snack foods.
This year we looked at the 38% of those surveyed that have cable and disc conveyors in their facility.
This group is more likely than those who do not have cable and disc
conveyors in their facility:
- Are extremely satisfied with their current conveying systems (50% with cable and disc are extremely satisfied vs 36% of those with no cable and disc conveyors).
- Report that cable and disc conveyors are the most effective at gently conveying materials like coffee, nuts, and snack foods (45% vs 27% of those that do not have cable and disc conveyors).
- Report that cable and disc conveyors are the most energy efficient (41% vs 25% of those that do not have cable and disc conveyors).
Which of the following is MOST EFFECTIVE at gently conveying materials like coffee, nuts, and snack foods? (2022 data)
Fill out this simple form to download the full 21-page PDF report on State Of Conveying 2023.