In the fast-paced realm of modern manufacturing, understanding advanced conveyor manufacturing works is essential. So, how does an industrial conveyor system work? Cablevey Conveyors not only answers this question but also redefines the landscape with innovative conveyor solutions, such as a tubular conveying system.
How Does an Industrial Conveyor System Work?
An industrial conveyor system works by seamlessly transporting materials from one point to another within a facility. Cablevey Conveyors, a leader in this field, employs innovative solutions like tubular conveying systems. These conveyor technologies utilize various power sources and transfer modes, optimizing efficiency and revolutionizing material handling across industries.
Nowadays, any type of manufacturing process would be unthinkable without an efficient conveyor system. The global conveyors market was valued at $7.73 billion in 2020 and is expected to grow up to $10.07 billion by 2026. The globalization of the economy leads to shorter production cycles, increased international flow of goods, and accelerating advancements in e-commerce – all of which drive the conveyor market forward.
Understanding the Versatility of Industrial Conveyor Systems
Conveyors vary widely in their dimensions, catering to diverse needs, ranging from sizable systems designed for bulk product handling to compact counterparts tailored for the precise sorting of discrete items. Industrial conveyor systems exhibit remarkable versatility, facilitating the transportation of a broad spectrum of products and materials, including metals, plastics, boxes, food items, cosmetics, medical supplies, and more.
Among the commonly used conveyor types are traditional conveyor belt systems, cable conveyors, screw or auger conveyors, roller conveyors, bucket elevators, and their equivalents. But how do industrial conveyor systems work? What do you need to know before you decide to purchase one for your business? Let’s check out all the factors that could influence your decision.
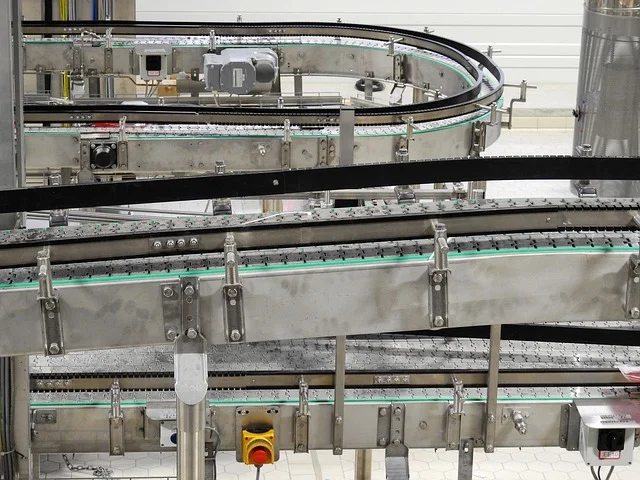
Main Purpose Is Seamless Material Flow Within Facilities
The primary objective of a conveyor system, stemming from its initial invention, is to seamlessly move products, goods, raw materials, or any other materials from one location to another, usually within the confines of the same building or designated area.
Conveyors belong to a business segment called intralogistics – the process of automating, optimizing, and managing the flow of information and material goods within the walls of a single production or distribution facility. Industries that make the most use of this type of equipment are:
- Aerospace,
- Agricultural,
- Automotive,
- Beverage industries,
- Bottling and canning,
- Building materials industry,
- Chemical industry,
- Computer,
- Electronic,
- Food processing,
- Packaging,
- Pharmaceutical industry,
- Printing industry,
- Mining.
Check Out the Most Important Features of an Automatic Conveyor System
Exploring the crucial facets of an automatic conveyor system unveils a world of innovation and efficiency in material handling. As industries evolve, the demand for streamlined processes becomes a must, and manufacturing conveyor systems have changed the traditional conveyor belt system. That’s why you need to check out all the features that will help you make the final decision.
Power – A Triad of Options and Motor Efficiency
Understanding the dynamics of conveyor power not only enhances operational efficiency but also empowers businesses to choose the system that aligns seamlessly with their unique needs. Conveyor systems can be powered in three ways:
- By a motor,
- By gravity,
- Manually.
Manual and gravity-powered conveyor systems typically include rollers. Rollers make it easy to move items from point A to point B with minimal effort on the workers’ part. All an employee needs to do is push the item along a horizontal conveyor or place it at the top and let it slide down an angled system. Manual and gravity roller conveyors do not require any electricity to run.
Large manufacturing businesses will need motor-powered conveyor engineering to handle their material and product transportation more often than not.
The most common type of motor used for conveyor systems is a three-phase AC. AC motors are ideal for conveyors that continuously operate in one direction. Three-phase is also more efficient than single-phase because there is no capacitor delay and no starting windings. Most production facilities use 440V motors, double the amount used in homes. Higher voltage is more efficient for a manufacturing setting because there are lower transmission losses over the grid.
Mode of Transfer – Choose the Most Suitable for Your Materials
Depending on several factors, material handling systems can use different modes of transfer. When choosing the right conveyor for your production or distribution centers, you need to consider the floor plan, the type of material you’re transporting, the system’s throughput, and more. Here are the most common modes of transfer for industrial conveyor systems:
- Aero-mechanical – In these conveyor systems, evenly spaced discs move the material at high speed. Sometimes, the pace needs to be reduced to prevent the breakage of material.
- Belts – One of the most prevalent and simplest forms of conveyors. Moving conveyor belt systems rest on a steel frame that has the purpose of supporting the belts and the materials they’re moving.
- Buckets – Multi-sided containers are attached to chains, belts, or cables to move the material along. The containers (buckets) of the bucket conveyor remain in an upright position during transport and are tipped over to release the material in the right place.
- Chains – This conveyor type utilizes an endless chain for material transport. The chain moves thanks to sprockets at either end of the trough. Chain conveyors can be drag, plain chain, scraper, apron, flight, or en-masse chain conveyors.
- Pneumatic – In pneumatic conveyors, the bulk material is conveyed with the help of a vacuum or compressed air.
- Screw or auger – Screw or auger conveyors are great for liquid or granular materials. They use a rotating helical blade called a flighting to move the material. Typically, the flighting is placed inside a tube. Screw conveyors are one of the oldest ones ever invented, dating back to ancient times to pump irrigation water.
- Cable – Utilizing a completely enclosed system, cable conveyors are great for specialty materials, such as small and powdered materials, and clean, toxic, or delicate materials. A Cablevey tubular conveyor, in particular, offers a modular design for maximum flexibility and a wide range of applications.
Support – Explore Mechanisms and Maintenance Features
In addition to the power source and material transfer methods, the efficiency of a conveyor system is bolstered by a suite of support mechanisms. These essential frames maintain the stability of buckets, belts, chains, or rollers, ensuring the smooth flow of materials throughout the entire system. When it comes to a belt conveyor system, these frames play a crucial role in supporting and guiding the moving conveyor belts.
Alongside these support structures, the conveyor system is equipped with cleaning conveyor belts and maintenance features, underscoring the importance of regular upkeep for optimal performance. For businesses seeking reliability and precision, choosing reputable tubular and belt conveyor manufacturers becomes paramount, as they contribute to the overall functionality and longevity of the conveyor system.
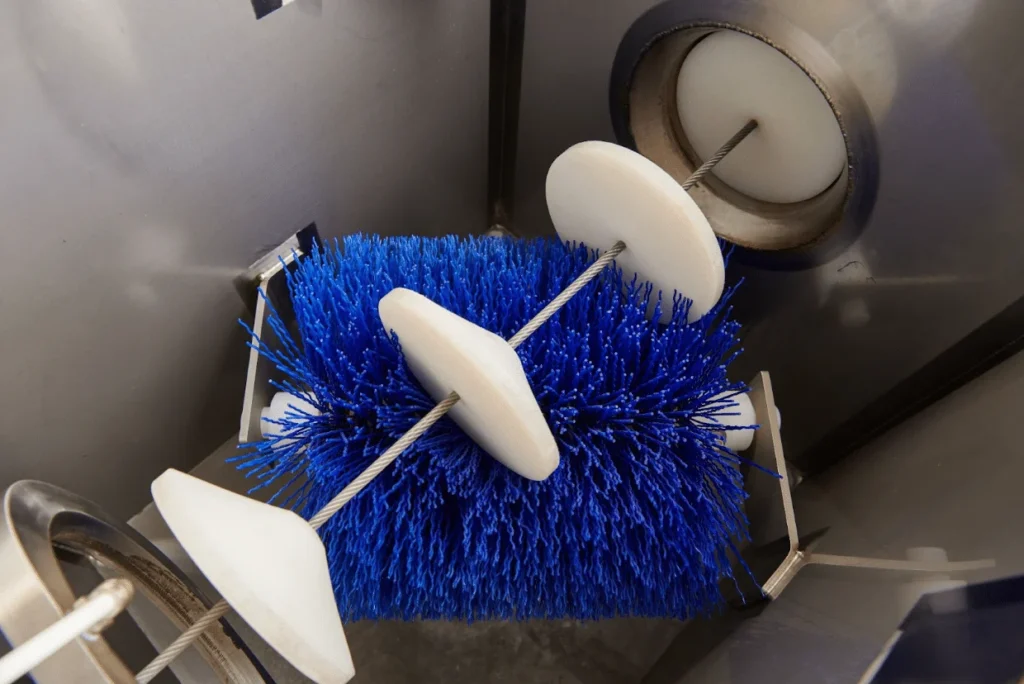
Take the Decision – Making Process Seriously
Although all conveyor systems have a standard framework, each has a different set of advantages and disadvantages. Not all conveyor systems are suitable for all industries. A car assembly center will require a vastly different design than a coffee manufacturer.
If you wish to install a brand new conveyor in your production facility, there are several crucial questions you need to ask to land on the correct type of conveyor:
- How much floor space does your facility have available? What is the ceiling height?
- Is energy efficiency an important factor for you?
- At what speed will the material be transported?
- What is the actual capacity of the conveyor system?
- How fragile is the conveyed material? Do you need to sacrifice integrity for throughput or vice versa?
- How can you minimize degradation during transport?
- How abrasive, flowable, and moist is the conveyed material?
- Will the transported product change in the future?
- How easy is it to clean the system? Does it need to be dismantled for maintenance?
- Are there any parts of the conveyor that are particularly difficult to clean? (Such as chains or ropes.)
- Does it require downtime for regular maintenance?
- How often do particular parts need to be replaced? Are they expensive and/or difficult to obtain?
- Is the system you’re considering financially feasible for your business?
The decision-making process of choosing the right industrial conveyor system is the most critical step. Before making a purchase, you and your team should answer all of these questions and more to make sure your business will thrive with the new material conveyor.
Benefits of Implementing an Industrial Conveyor System Into Your Manufacturing
It is not an easy task to select the right conveyor system for your business. You need to consider many factors and plan everything out in advance. But the benefits of installing a conveyor in your facilities are undeniable – you are looking at a drastic decrease in costs and an increase in efficiency, throughput, and overall performance.
Implementing an automated conveyor system into your manufacturing facility comes with a host of advantages. Here are the most important ones:
- Increased safety – Conveyors are one of the safest methods for moving materials across the production floor. They can have emergency stop switches, speed adjustments, and many more safeguards. These systems are the only ones that can improve productivity and efficiency while at the same time not increasing the number of worker accidents or injuries.
- High volume – A manufacturer can never hope to transport as much material with their workers as they can with a conveyor system. If your business has reached its peak, it’s time to invest in conveyor systems manufacturers who will offer you a system that allows you even faster production times.
- Continuous operation – Unlike people who need to rest and recover from their work, machines can operate for far longer before stopping. Regular maintenance is obligatory, but conveyor systems and conveyor installation supervision are infinitely more efficient than human labor.
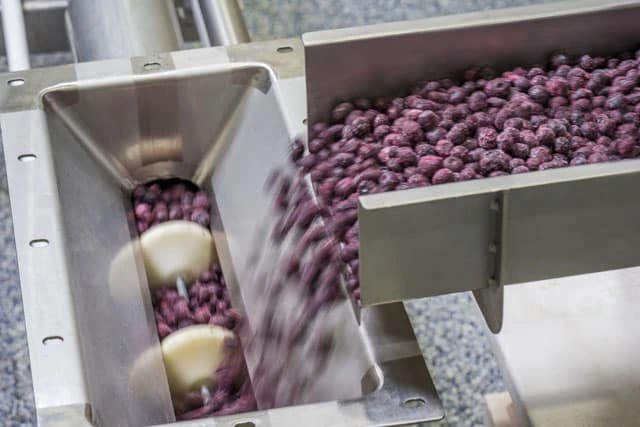
Cablevey Conveyors Offer Seamless Material Handling
The primary purpose of a conveyor system in any industry is to transport bulk materials from one spot in the production area to another. Even though there are dozens of conveyors, the basic conveyor components include a source of power, a system of transport, a support system, and controls. Depending on the type of conveyor you’re considering, it may come with various additional features.Curious about acquiring a conveyor system? Reach out to Cablevey Conveyors for assistance. We will be more than happy to answer any questions you may have and help you get the best product for your business goals.