Although similar in functionality for food processors, tubular chain and cable disc drag conveyors have distinct differences in components and operation. A closer look at cable vs. chain systems will help food manufacturers better understand which system would best support their dry food processing requirements. Here’s how to decide which industrial conveyor belt system aligns best with your industry needs.
What Are Tubular Drag Conveyors?
Tubular drag conveyors are a type of mechanically driven conveyors designed to drag material along the inside of a tube. They are essentially transferring flowable bulk materials to discharge points from in-feed points through an enclosed conduit. Using either a cable or a chain, with close-running discs spaced along its length, the ends of the tubular drag conveyor are connected to form an endless loop, which is pulled by a motor-driven sprocket within an enclosed tube.
Tubular drag conveyors are flexible and designed for versatility in gentle material handling operations. Bends facilitate changes in direction in the tubing or by corner housings for tighter turns. Discharge of the product is achieved through outlet boxes and discharge funnels. Modular components allow changes in conveyor routing, length, and the number and position of inlets and outlets. They can move material vertically, horizontally, around corners, and at an angle.
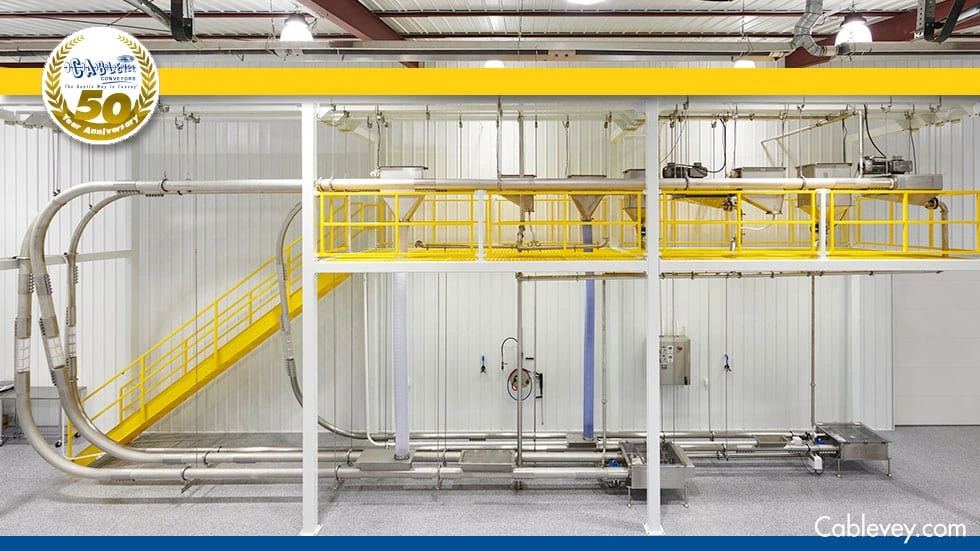
Effortless Movements With Chain And Disc Conveyors
Tubular drag chain conveyors carefully transport food items within a sealed tube using a chain that circulates in a continuous loop. This chain carries solid round plates (known as flights) that facilitate the movement of food inside the tube.
There are two predominant chain varieties for these conveyors: link chains and roller chains. The link chain boasts a design that lets it function akin to a universal joint, allowing it to navigate multiple direction changes within the tube.
On the other hand, roller chains are composed of linked plates secured with pins and bushings, and they generally move in a straight line. Both types are commonly crafted from 316 stainless steel, known for its corrosion and acid resistance, though carbon steel variants are available.
How Can You Ensure the Utmost Performance of the Conveyor Belt System?
Friction often arises at chain contact points, especially during initial system operations, and this is more pronounced in food processing setups where lubricants aren’t applied. This can lead to wear and tear at these interaction zones along the chain.
For optimal performance of tubular drag conveyors, it’s imperative to regularly adjust the chain-drive elements. This ensures the longevity of the conveying discs, chain, and tube. A tensioning mechanism ensures the chain maintains the correct tension.
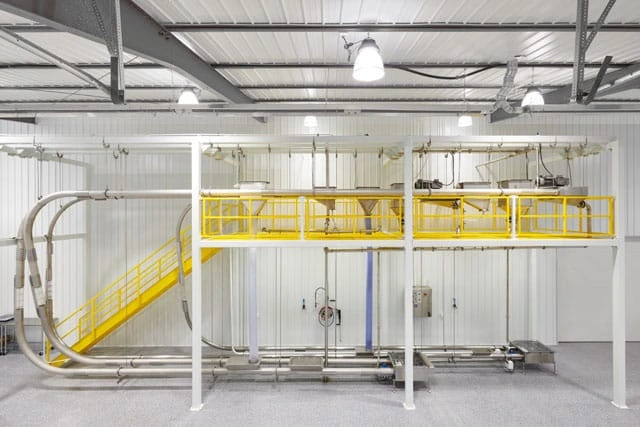
The Impressive Power of Cable And Disc Conveyors
Similar to tubular drag chain conveyors, tubular cable and disc systems safely transport food items within a closed tube. But instead of a chain, these systems utilize a coated, flexible stainless steel cable that moves in a continuous loop. This cable has solid round plates (referred to as flights) attached, facilitating the movement of food inside the tube.
These tubular drag cable systems can shift up to 80,000 pounds of product each hour at a gentle pace, closely resembling the efficiency of chain and disc conveyors, with the added advantage of virtually preventing product damage.
The predominant cable for these conveyors is the WSC (wire strand core), commonly associated with aircraft control functions, hence its nickname, “aircraft cable.” These durable aircraft cables, crafted with high-tensile strength, are unlikely to snap under normal circumstances. The core is made from type 316 stainless steel.
Around this core, you’ll find stainless steel ropes woven in a helical pattern, consisting of several strands. The impressive strength of these rope wires allows the cables to handle substantial tensile loads despite their slender appearance.
Here is what you need to know about these systems:
Compensation for Minor Failures in the Short Run
Historically, wire rope evolved from wrought iron chains, which had a record of mechanical failure. While flaws in contemporary chain links can lead to catastrophic failure, defects in the wires making up a steel cable are less critical, as the other wires easily take up the load.
Low Horsepower
The tubular cable and disc conveyor operates on low horsepower, utilizing energy-efficient variable-speed motors of 1-5 HP each, effectively consuming minimal power compared to other conveyor systems used in food processing.
Production Flow Can Be Adjusted
The system’s production flow can be adjusted to variable speeds to modify throughput. A drive unit provides power to move the cable and disc assembly through the conveying tubes. The system components are connected with compression couplers and gaskets, making the system totally enclosed and dust-free.
A Tension Turnaround Unit
Like tubular drag chain conveyors, maintaining the required cable tension by the installer and operator is necessary for the system’s proper function and to eliminate the remote possibility of strand breaks at connection points.
A tension turnaround unit maintains the proper cable tension while the system is in operation. The entire cable is nylon sealed, ensuring that no food directly comes in contact with it and that no potential strand breaks come in contact with the conveyed food products.
The System’s Flexibility
The conveyor system’s flexibility allows it to connect with any food production process, from receiving raw materials to weighing and filling, grinding, and packaging. They are critically applicable where food components can become damaged, where contamination is prevalent, or dust accumulation can be excessive, such as in filling and packaging.
How Does Food Safety Change Using One or Another System?
Product contamination is a key issue in food production conveying. It’s crucial to keep foreign matter from entering the process stream, maintain system sanitation, and keep the system free from unwanted allergens.
The importance of preventing product contamination is magnified with increasingly stringent government and industry product track and trace mandates, and consumer demands maintaining product integrity and safety. So, you understand how choosing the right conveyor belt for food is the crucial step you need to take.
Line Changeovers Have Become a Real Issue
Line changeovers have become a focal issue in food production relative to cleanliness and the speed of conversions. Companies often have to run different product lines within a single day or even within the same shift, and every minute spent disassembling a conveyor belt for a warehouse for cleaning consumes valuable production time.
Yet, if not cleaned properly, a batch of conveyed food products needs to be discarded because of contamination, which leads to lost profit. Or worse, consumers could be negatively impacted, resulting in potential injury, illness, costly recalls, and impacted brand reputation.
Food processors are charged with administering line changeovers as quickly as possible to resolve these issues while maintaining 100% system cleanliness.
Explore Why You Should Consider Bulk Material Handling Equipment
Still not sure what to look for in food systems like these? Tubular drag conveyors chain and cable systems transport dry bulk food products gently to discharge points in totally enclosed, dust-free conveying tubes.
This prevents foreign substances from contaminating the product stream and keeps dust from the transported product from escaping into the production environment, reducing both the incidence of health hazards and the potential for dust explosions.
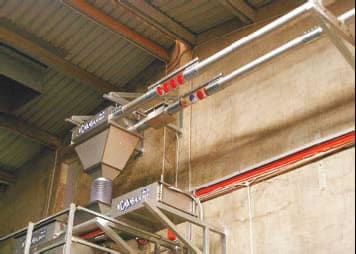
Chain and Disc Systems Sanitation Meets the FDA Requirements
Tubular chain and disc conveyor systems are designed to meet sanitation specifications as mandated by FDA regulations. These systems’ core is the polished stainless steel conveyor link chain or roller chain, rated acid and corrosion-resistant.
Because the entire chain is directly immersed within the food being conveyed, cleaning the chain, in addition to the tubing itself, requires more care than what is needed for the cable. This is particularly true with a roller chain, where food particles can pack into spaces between plates, pins, and bushings and where water can remain trapped after cleaning, resulting in potential product contamination.
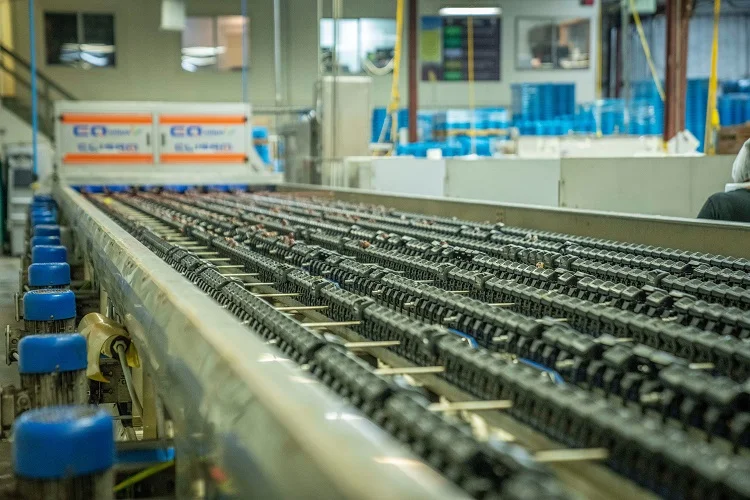
Chain and Disc Conveyor Cleaning Mechanisms
Cleaning mechanisms minimize or eliminate the build-up of food particles from the chain, conveying tubes, and associated equipment. These mechanisms include brush boxes, chain knockers, and wet clean-in-place (CIP) systems.
Dry cleaning mechanisms are available for tubular chain conveyors. The brush box is a line insert that mechanically brushes accumulated fines off discs. The chain knocker is a line insert that dislodges particles from the chain.
The wet cleaning CIP (self-cleaning) mechanism available for tubular chain conveyors consists of a 3-step internal tube cleaning process:
- Foam cleaning/sanitizing – foam cleaning agent is introduced into the tube environment to cleanse and sanitize all internal parts of the system.
- Rinse – a water rinse is run through the system to flush out debris and the foam cleaning/sanitation agent.
- Dry air – warm, dry air is pumped throughout to dry the system and make it ready for the resumption of operation.
Cable and Disc Systems Sanitation
Tubular cable and disc conveyors for food-grade applications are better designed to eliminate places for fines to accumulate. Solid discs are used, with no screws or bolts, and they are attached directly to the cable. Stainless steel connectors are used throughout the custom conveyor belt system, and the equipment is removable for easy cleaning.
One of the key advantages of tubular cable and disc conveyors over the tubular chain and disc conveyors is the significantly reduced possibility of trapping food residue. As with both the link chain and roller chain, the cable is fully immersed within the food being transported through the tube. But the chain has significantly more surface area exposed to the food.
Further, the cable is completely uniform and smooth throughout its entire route within the tube. However, the chain itself has many 90-degree turns and connections link to link, where food residue can more easily collect. The most hygienic food processing equipment designs minimize or eliminate 90-degree angles where food contact is present.
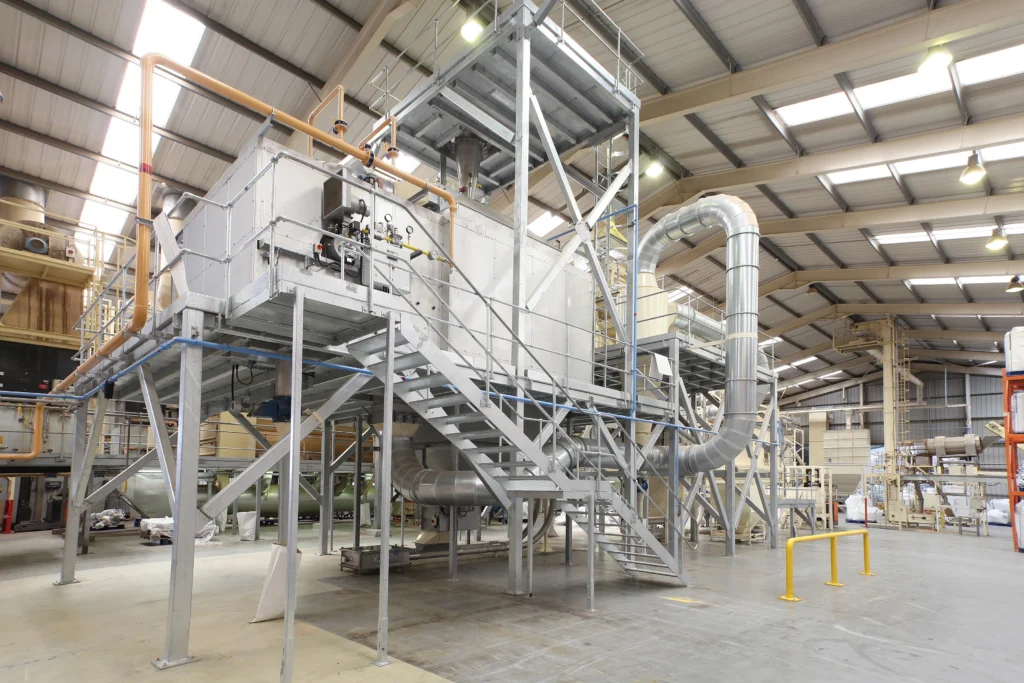
Cable and Disc Conveyor Cleaning Mechanisms
Compared to tubular chain and disc conveyors, tubular drag cable and disc conveyor systems offer more wet and dry cleaning options. These include urethane wipers, brush boxes, air knives, bristle brushes, inline sponges, and multi-step CIP (self-cleaning) wet cleaning.
Dry cleaning mechanisms available for tubular cable conveyors:
- Brush box – a line insert that mechanically brushes accumulated fines off discs.
- Urethane wiper disc – a disc insert that wipes away accumulated fines and particles while the system is in progress.
- Air knife – strategically located at product discharge locations in the line, air knife inserts use compressed air to blow accumulating fines off discs and the cable.
- Sponge disc and sanitizing cleaner – a disposable sponge disc that is run through the system with an applied cleaning agent.
- Bristle brushes – a brush that is run through the system to remove accumulated fines off the tubing.
The wet cleaning CIP (self-cleaning) mechanism available for tubular cable conveyors consists of a 3-step internal tube cleaning process:
- Foam agent – foam cleaning agent is introduced into the tube environment to cleanse all internal parts of the system.
- Sanitizing rinse – A sanitizing rinse is run through the system to flush out debris and the foaming agent.
- Water rinse – a second rinse of hot water flushes out sanitizing rinse, rendering the tube environment-production ready.
Check Out All the Benefits of Cable vs. Chain Systems
While chains are often lauded for their ruggedness and reliability, cables present a fresh approach with unparalleled flexibility and efficiency. Delving into the benefits of cable versus chain not only offers insights into their individual merits but also guides industries in making an informed choice tailored to their specific needs.
Decreased System Downtime
The cable has no moving components like links, plates, pins, and bushings integral to chains that cause friction and wear. With chain and disc systems, if just one part breaks, a complete system shutdown occurs.
However, excessive system stress on cables results in localized strain breaks – loads are redistributed, maintaining the cable’s integrity and system uptime.
Minimized Direct Contact With Food
A nylon coating prevents direct contact of the stainless steel cable with transported food. The nylon’s smooth surface is void of crevices or sharp-angled components where food particles could be collected, such as is the case with chain links, plates, pins, and bushings where food particles can gather in chains.
Improved Performance for Food Safety, Sanitation, and Changeovers
In addition to a 3-step, the clean-in-place wet-cleaning process for internal tubing, cable, and disc systems provides a considerably more comprehensive set of five mechanisms for inner tube dry cleaning than chain and disc systems.
These processes ensure sanitation and enable faster changeovers than chain systems, which must contend with trapped water deposits within components after cleaning.
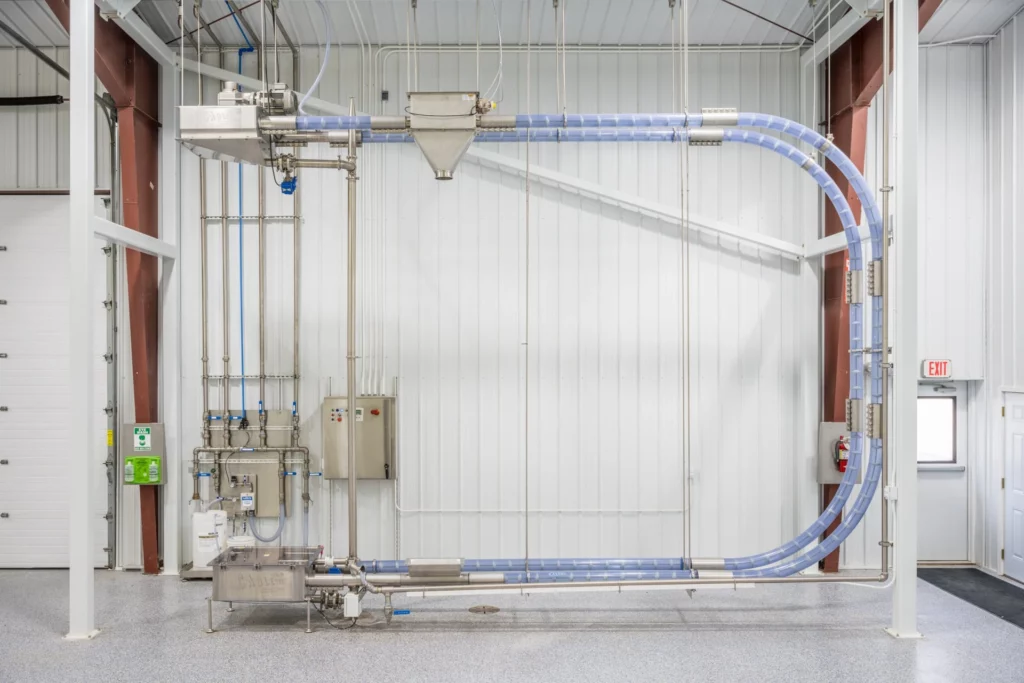
Check How Modern Technology Can Help Your Brand
Tubular drag conveyor systems installed in facilities 10 to 15 years ago may have been adequate at that time. Still, better technology in conveying system design, controls, and automation has brought a whole new generation of conveyors for use in food processing.If you are looking for the next conveyor for your food processing facilities, Cablevey Conveyors offers state-of-the-art tubular cable and disc conveyor systems. Contact us to learn more about how we can help you choose the best type of tubular conveyor system for your brand.