In today’s competitive food processing industry, implementing efficient and hygienic solutions is vital for success. That is precisely why you need tubular conveyor systems for your food processing facility. Our post highlights the importance of these systems in optimizing operations. Tubular conveyors offer unparalleled advantages in terms of product safety, operational efficiency, and maintenance ease, making them an essential component for facilities aiming to enhance productivity while adhering to stringent health standards.
The Best Conveyor Engineering for the Food Processing Industry
When it comes to conveyor systems for the food processing industry, it’s important to choose one that can efficiently and safely handle fragile materials while minimizing contamination risk. Tubular drag cable and disc conveyor systems are conveyor solutions that can provide you with such efficiency. These outstanding conveyor technologies offer:
- Gentle conveying,
- Enclosed design that protects products from dust and debris,
- Flexible and modular design,
- Low energy consumption,
- Varying capacities to meet different production needs.
These unique features make it a superior choice when compared to traditional conveyor belts, pneumatic conveyors, screw augers, and bucket elevators. In the following text, we will dive into how tubular conveyor systems can transform your food processing business.
Gentle Conveying Is Guaranteed With a Tubular Conveying System
Tubular drag conveyor systems utilize a sealed cable that runs inside a tube. Along this cable, solid circular discs are evenly spaced, creating pockets in which the conveyed material sits. The cable is driven by a motor, which pulls the material through the tube by the discs. This design allows for a low-impact, smooth movement of the conveyed material that minimizes product damage.
The pockets formed by the discs also cushion the product, further reducing the chance of damage. This is particularly beneficial for delicate food products such as snack foods, pet food, frozen food, nuts, coffee beans, tea blends, and other bulk materials. These products may be easily broken or damaged by traditional conveyor systems (such as a screw conveyor or a pneumatic conveyor), but the gentle movement provided by the tubular conveyor system keeps them intact. This results in an overall reduction of waste and an increase in product quality.
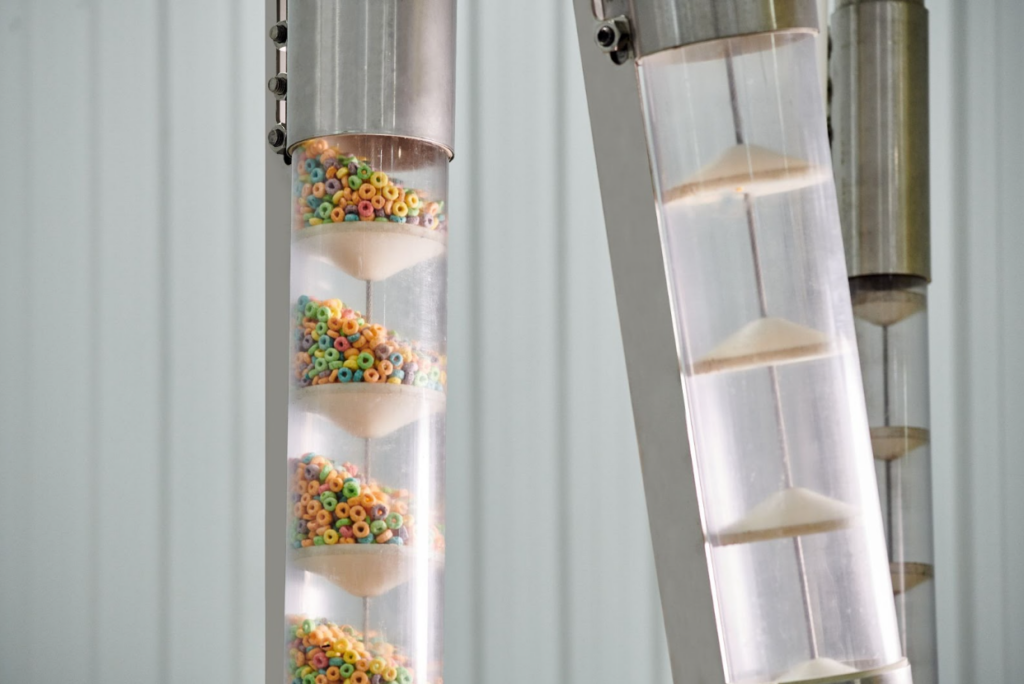
Enclosed Tube Design Is One of the Key Features
One of the best features of a tubular drag cable and disc conveyor system is its enclosed tube design. The design plays a vital role in reducing the risk of contamination and ensuring food safety. Contamination refers to the presence of unwanted substances or microorganisms in food, which can cause food poisoning, product spoilage, and other health hazards.
An enclosed tube provides a barrier that protects food products from external contaminants such as dust, debris, and other particles. Additionally, the sealed cable inside the tube ensures that the conveyed material doesn’t come in direct contact with the steel. The use of an enclosed tube design not only improves the overall safety of the food products but also enhances their quality. The enclosed design also reduces the need for cleaning and maintenance, which can save time and money.
The Tubular Conveying System’s Design Is Quite Flexible as Well
A tubular drag cable and disc conveyor system boasts a flexible design that can easily accommodate facilities with small floor spaces. The system is designed with modular components that can be assembled and disassembled in a variety of configurations, allowing for easy conveyor installation. This makes it an ideal solution for facilities with limited space or changing production requirements.
The tubular conveyor system can fit into tight spaces such as corners or under existing equipment without sacrificing performance or efficiency. Additionally, this flexibility ensures that the conveyor system can grow with the production facility and adapt to changing needs. In case of any breakdown, the modular design enables fast and straightforward replacement of individual components, minimizing downtime and maximizing productivity. This flexibility also makes it easy to upgrade the system with new features as they become available.
Easy Cleaning and Maintenance Compared to Traditional Conveyor Technologies
One of many great things about a tubular drag cable conveyor designed by Cablevey Conveyors is its ability to be cleaned in place, which allows for quick and easy cleaning without the need to disassemble the system. This is achieved through the use of specialized cleaning equipment (both dry and wet) that can reach all parts of the conveyor. This drastically reduces the cleaning time and effort needed compared to traditional conveyors.
Furthermore, the maintenance of a tubular drag cable and disc conveyor system does not require a lot of downtime. The system is designed with modular components that can be quickly and easily replaced in case of any breakdown. This means that repairs and maintenance can be done promptly, minimizing downtime and maximizing productivity.
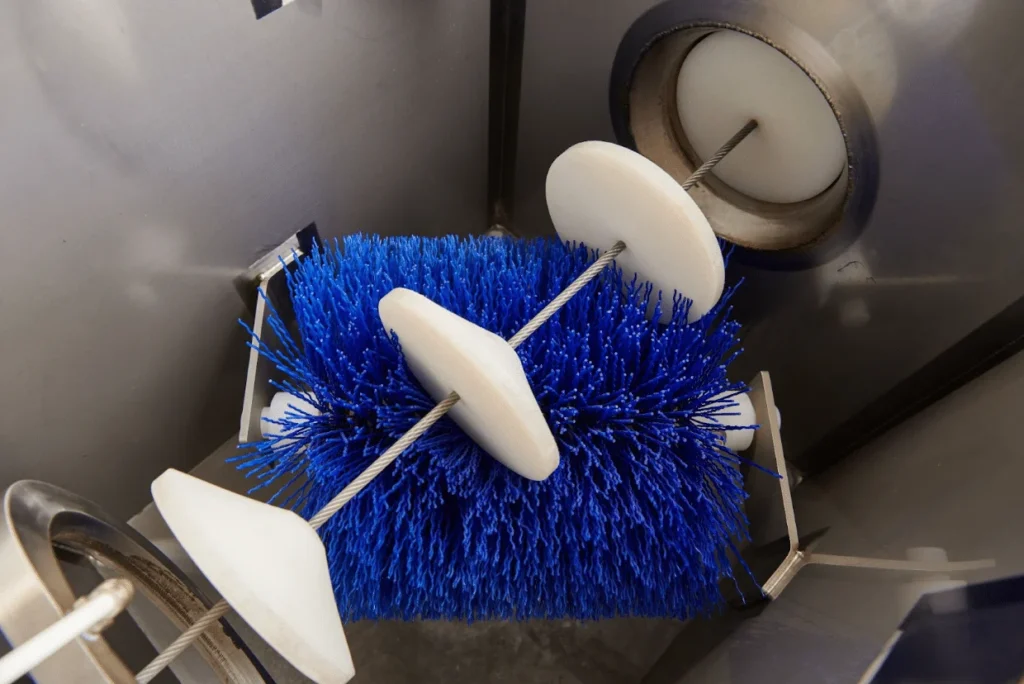
Low Energy Consumption Leads to Costs Savings
Tubular drag conveyors are designed with energy efficiency in mind, making them a smart investment for food processors looking to save on energy costs. The system’s enclosed design and low-friction movement allow it to consume less energy than traditional conveyors. It’s not all about cost savings, though – this also helps reduce the facility’s carbon footprint.
The low-friction movement of the conveyor system also contributes to its energy efficiency. Unlike traditional conveyors that require more energy to move materials, the tubular conveyor system’s smooth movement means it uses less energy to convey the same amount of materials. In today’s world, where energy costs are constantly on the rise and companies are looking for ways to reduce their carbon footprint, the low energy consumption of tubular drag conveyor systems makes them highly desirable food conveyors.
Varying Capacities Thanks to Varying Tube Diameters
A tubular drag cable and disc conveyor system offer the ability to accommodate different capacities through its varying tube diameters. The diameter of the tube can be adjusted to match the needs of the facility’s production. Smaller diameter tubes are well-suited for handling smaller quantities of material, while larger diameter tubes are better suited for larger quantities. Cablevey Conveyors offers the following tube diameters:
- 2″ systems – convey up to 3,000 lbs per hour,
- 4″ systems – convey up to 21,000 lbs per hour,
- 6″ systems – convey up to 49,420 lbs per hour,
- 8″ systems – convey up to 80,000 lbs per hour.
This feature allows food processing facilities to customize their conveyor system to their specific needs, whether it’s for a small batch of products or large-scale production. Furthermore, the varying tube diameters also allow the system to handle different types of products. For example, a small diameter tube can be used to convey small, delicate products such as berries, while a larger diameter tube can be used to convey bulkier items such as frozen vegetables.
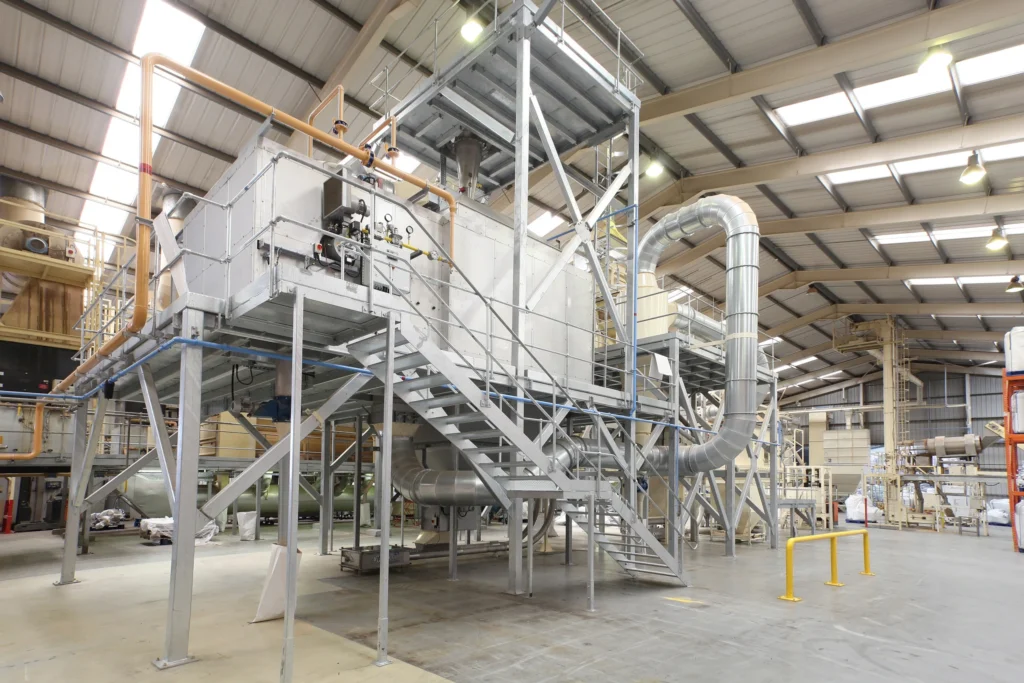
Additional Features You Should Know About
Tubular drag cable and disc conveyor systems can be customized with additional features to meet specific application needs. Two such features that can be added to the system are an internal minicam and a pneumatic tensioning air device.
An internal minicam is like a secret spy camera for your conveyor. It helps detect any potential weak spots in the construction, easily inspect cleaning and maintenance levels, and even diagnose issues remotely, keeping your conveyor running smoothly. This feature allows for easy monitoring to ensure the system is running at peak performance and can help identify issues before they become major problems, consequently saving you time and money on repairs and maintenance.
A tubular drag cable and disc conveyor system can be equipped with a pneumatic tensioning device that manages the tightness of the cable. This is crucial for the proper functioning, reliability, longevity, and performance of the conveyor. This device allows adjusting cable tension to the optimal level, ensuring that it is not too loose or too tight. If the cable is too loose, it could cause a malfunction, and if it’s too tight, it could cause excessive wear and energy consumption.
Contact Cablevey Conveyors to Learn More About Tubular Conveyor Systems and Get Them for Your Facility
If you’re seeking advanced, efficient solutions for material handling in your facility, Cablevey Conveyors is your go-to expert for manufacturing conveyor systems. Specializing in state-of-the-art tubular conveyor systems, Cablevey Conveyors offers a range of innovative designs tailored to meet the unique needs of your operation. Whether you’re in the food processing, pharmaceutical, or any bulk material industry, our team is ready to assist.
By choosing Cablevey Conveyors, you’ll benefit from systems that prioritize product integrity, hygiene, and energy efficiency. Contact us today to explore how our tubular conveyor systems can transform your facility’s operations. Our experienced professionals will guide you through the selection process, ensuring you get a system that aligns perfectly with your production goals and requirements. Don’t miss the opportunity to elevate your facility with Cablevey Conveyors’ advanced tubular conveyor solutions.
FAQ
What Are the Key Benefits of Using Tubular Conveyor Systems in Food Processing Facilities?
Tubular conveyor systems offer significant benefits in food processing, including the gentle conveying of delicate products like nuts and frozen foods, reducing product damage and waste. The enclosed tube design minimizes contamination risks, enhancing product safety and quality. Tubular conveyors also boast flexible and modular designs, fitting into various spaces and adapting to changing needs.
How Does the Enclosed Design of Tubular Conveyors Contribute to Food Safety?
The enclosed design plays a crucial role in ensuring food safety by protecting products from external contaminants like dust and debris. This barrier also reduces cleaning and maintenance needs, further supporting hygiene standards in food processing facilities.
Can Tubular Conveyor Systems Be Adapted to Different Facility Sizes and Production Changes?
Yes, tubular conveyor systems are highly adaptable due to their modular design. They can be assembled in various configurations, making them ideal for facilities with limited space or evolving production requirements. This flexibility also enables easy upgrading and component replacement.
What Makes Tubular Conveyor Systems Energy-Efficient and Cost-Effective?
Tubular conveyors are designed for low-energy consumption, which translates into cost savings and a reduced carbon footprint. Their low-friction movement requires less energy compared to traditional conveyors, making them an economically and environmentally sustainable choice for food processors.
What Additional Features Enhance the Functionality of Tubular Conveyor Systems?
Tubular conveyor systems can include features like an internal minicam for monitoring and troubleshooting and a pneumatic tensioning device for optimal cable tension. These additions improve system reliability, performance, and longevity while also reducing the need for extensive maintenance and repairs.