Different nut production companies use different conveyors to transport raw nut material through various processing phases. While some nut processing plants function efficiently enough with their existing conveyor equipment, many don’t realize how much more their operations could improve until they compare their conveyors with a nut conveyor system designed specifically to meet the unique demands of the nut industry.
The Disadvantages of Using the Wrong Nut Conveyor System
It’s also not until a company has used the wrong conveyor system for some time and lost a considerable amount of money that they realize they’ve been moving materials incorrectly. The consequences of an inefficient and incompatible conveyance system include product breakage, degradation, and wastage. Also, a conveyor that wasn’t designed to be hygienic and protect both the raw materials and the facility from contaminants may land you in trouble with consumers and regulating agencies.
Why It’s Important to Consider an Adequate Upgrade
In this complete guide to choosing the right nut conveyor system, we will discuss the benefits of using a conveyor to move your materials. We will also talk about the different types of nut conveyors and what to consider when selecting a conveyor type. And finally, we reveal which nut conveyor is most compatible with the unique demands of the nut industry.
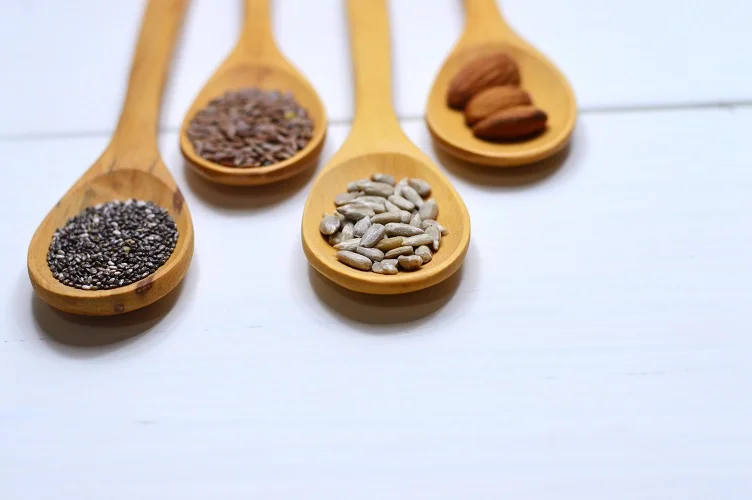
The Benefits of Using a Conveyor System in the Nut Industry
Conveyor systems have been around for centuries. While the first conveyor was developed to move goods onto ships at ports faster, conveyors have evolved and now come in different dimensions and applications. Gravity and powered conveyor systems are used in a wide range of industries to transport products and materials from other points in a facility.
In the nut industry, powered or mechanical conveyors have not only sped up the transfer of materials between long distances in the production plant, but they have provided a wide range of additional benefits.
When you install the right conveyor in your nut production plant or the adequate conveyor belt for a warehouse, you not only reduce labor costs but also increase workplace safety. Fewer workers on the production floor mean less human traffic, resulting in a safer work environment.
The problem with using bulk material handling equipment such as cranes, wheelbarrows, forklifts, or other heavy machinery on wheels is that they increase your risk of workplace accidents. Forklifts and cranes require training and skill to operate. Forklift operators need to learn how to maneuver the machine around corners and narrow spaces and avoid human traffic.
A collision with a forklift can not only result in product breakage and property damage, but in a worst-case scenario, it can cause serious injury or death. Unfortunately, humans are prone to mistakes. And when you combine heavy machinery with human error, the consequences can be disastrous. Forklifts on the production floor can also lower productivity. Even smaller forklifts take up space. For safety, workers need to stay clear of them, which can cause high-traffic areas to become congested.
Mechanical conveyors automate the transport of materials between varying distances and elevations, keeping workers on the production line safe and focused on other tasks. When workers know their employers prioritize their safety and well-being, the result is highly motivated workers who are happier and more productive. This can be achieved by eliminating the need for workers to manually move products and materials around a facility.
When choosing between a power conveyor system or a gravity conveyor, remember that a gravity conveyor still needs an incline or a person’s manual force to push the load. On the other hand, mechanical conveyors eliminate or minimize the need for strenuous, manual labor.
Regulating agencies that set the standards for food safety will expect that your nut production plant complies with its rules and regulations. When you minimize or eliminate the manual handling of materials by using an industrial conveyor belt for food, you help ensure the facility is safe and sanitary.
But while using conveyors is significantly more hygienic than the human handling of materials, it’s important to note that not all conveyors are suitable for the nut industry. Some conveyor systems are considered more hygienic than others and more compatible with the processing of nuts. For example, bucket elevators and traditional conveyor belts have open profiles, which may expose raw materials to contaminants.
Outdated, manual methods of moving materials can cause costly damage to raw materials. The result is product wastage, degradation, or imperfections that make the product inferior. To stay competitive and meet the unique quality standards of the industry, you need a conveyance system that moves raw materials gently and efficiently so that they retain their quality no matter which phase of processing they are going through.
The Common Types of Conveyors for Nuts
Nuts such as almonds, cashews, peanuts, pistachios, walnuts, and pecans are among the most in-demand nuts in the marketplace. While some companies work exclusively with one specific nut, others may be producing snack food like trail mix, which blends different nuts and other ingredients. This means each nut processor will have unique conveyor requirements.
From overhead conveyors and pallet conveyors to belt rollers, there are dozens of types of conveyors used in the food industry. However, there are certain conveyors that dominate the nut industry. Here are the most commonly used conveyors for nut processing:
- Also known as a “rope and disc” conveyor, aeromechanical conveyors consist of several discs that are spaced evenly on a wire rope within a steel tube. An airstream is produced when the rope and discs travel at high speed in a continuous loop. Materials move along the system due to the airstream.
- The belt conveyor system was the first-ever conveyor design, and it is still used today. You’ll most often see them in airports for moving luggage. The system typically consists of two or more pulleys and a conveyor belt system. The powered pulleys move the belt and the materials forward. Belt conveyors have an open profile, which allows workers to reach in and pull out materials from the production line if necessary. The most common belt conveyor types include belt rollers or gravity rollers, flat belts, incline/decline belts, and modular belts.
- Bucket elevators elevate materials vertically. The system consists of a series of plastic buckets attached to a belt. The concept is similar to how a belt conveyor moves materials with a rotating belt or chain and drive pulleys. The difference is that a bucket elevator uses buckets attached to the chain conveyor and moves vertically to carry materials up or down.
- Tubular drag conveyor systems feature a combination of conveyance tubes with cable and discs attached at set intervals. Materials slide gently through stainless steel tubing and are held between the discs in the enclosed tube. The system can be designed with the routing of the tubing at any angle and single or multiple inlets and outlets.
- Chain disc conveyors have multiple inlets and discharges and can move materials in any direction, making them ideal for complex routes. The system consists of a stainless-steel drive unit, drive and tensioning wheels, and control sensors. The material moves by sitting in front of the disc.
- Pneumatic conveyor systems were designed to move materials using air propulsion through enclosed convey lines. The force of air is typically generated by a compressor, vacuum pump, fan, or blower. The air velocity is high enough to effectively move materials to their destination. The basic components of a pneumatic conveyor system include an air mover, conveying line, discharge vessel, filtration system, and control panel.
- Roller conveyors use a series of rollers to move materials by either gravity or propulsion. A powered roller conveyor is powered by an internal motor, while a gravity roller conveyor uses the force of gravity to move materials downward. Each conveyor roller assembly is independently attached and can be removed from the conveyor support structure if it needs to be replaced.
- The screw conveyor, or auger conveyor, has a helical screw blade that rotates to move materials along the conveying line, which typically travels horizontally or inclined slightly. The materials are kept in the conveyor in the helical screw that sits in a tubular housing. The screw, or auger, rotates to move materials up pitches with every revolution or turn.
- The basic components of a vacuum conveyor system involve a vacuum conveyor, product intake, transport line, and control system. Materials are loaded into bins from the top, and a vacuum pump generates a vacuum which causes air to rush through the hose and suction inlet. The material moves by being carried into the air stream.
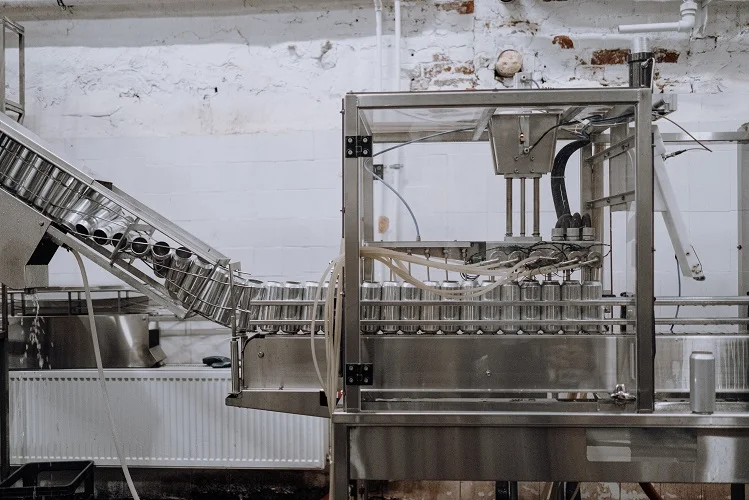
Comparing Nut Conveyors
To recognize which conveyor system is right for your nut processing plant, you must consider the unique demands of the industry, such as product quality and food safety. The biggest issue with belt conveyors is that they are typically open. As with any open profile conveyor system, this means that foreign particles and contaminants can end up in the food stream, potentially tainting the raw materials. To prevent exposure to the elements, it’s best to use an enclosed system.
Shelled nuts can be delicate and prone to breakage when mishandled. Your nut company’s success will rely on the ability to convey raw materials in a safe and efficient manner that results in high-quality nuts with no imperfections. Therefore, the best conveyor system is one designed to move materials gently.
Breakage Challenges in Pneumatic Conveying for Nuts
For example, dense phase and dilute phase pneumatic conveying control the transit of materials within an enclosed tubular “blowing” environment. While the enclosed system keeps the nut material free of contaminants, the method of conveyance can cause breakage, particularly when the materials have to move up, down, or around sweeps. The materials can get battered at these turning points.
Challenges with Vacuums and Aero Mechanical Conveyors
Breakage can also happen with vacuums and aero-mechanical conveyors. Materials are fine as long as they are moving in a straight line. However, making the turns through the conveyance elbows can prove to be too rough on fragile materials, which can break due to the force and impact. Vacuums can be especially harsh on nuts because of the lack of control once the materials are in the air vortex. The nuts get bumped around and battered, causing the delicate skin to become chipped or scratched.
Limitations of Screw Augers in Nut Conveyance
Screw augers are most commonly used to move semi-solid materials, such as wood chips, food waste, animal feed, and others. However, the problem with using them to convey nuts is how the system pulls materials upwards. Because screw augers use a screw to elevate materials, they can get caught in the screw threads and break. Especially fragile nuts can end up being ground up in screw augers, resulting in wastage.
The Pitfalls of Bucket Elevators for Fragile and High-Moisture Nuts
Bucket elevators have posed some of the biggest problems in the nut industry due to health and safety reasons. While bucket elevators are relatively gentle on materials and do not cause breakage like other conveyors, the buckets in these systems tend to accumulate debris or fines on both the inside and outside.
Some bucket systems are enclosed with “cowling.” While this conveyor design keeps the fines inside the machine, it still means the buckets have to be cleaned regularly. And when buckets need to be cleaned, you need to stop the entire machine because each bucket is attached with nuts and bolts. Removal or replacement of the buckets is time-consuming. Your operational timelines will suffer because the machine needs regular cleaning and maintenance due to its tendency to accumulate debris.
Bucket elevators are especially incompatible with nuts with high-moisture content or undergo a flotation process like pecans do when the meat is separated from the shell. The process involves a water-filled vessel that causes the pecan shell to fall off through the combination of hydration and vacuum pressure. The problem begins when the wet pecans need to be conveyed to the dryer inlet to remove the excess water. The pecans can end up sticking to the sides and bottoms of the buckets. And if they dry there and harden, they become difficult to clean off.
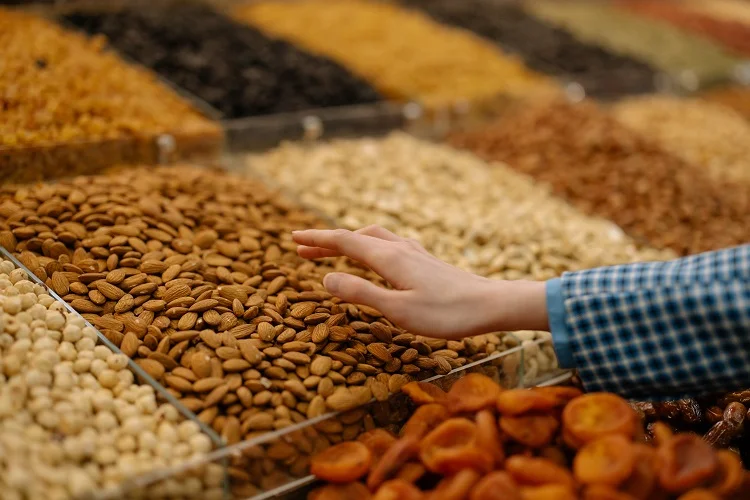
The Importance of Gentle Conveyance and a Contamination-Free Environment
Nuts need to be conveyed with care to not spoil their integrity. They also need to be kept in a clean environment to ensure the product is safe and complies with food safety regulations. These can be achieved by choosing a conveyor that was designed for gentle, clean, and efficient conveyance. In the nut industry, cable and tubular drag conveyor systems are replacing bucket elevators to relieve companies from the constant cleaning of individual buckets, which is not only laborious but also slows down operations because the whole machine needs to be shut off during cleaning.
Effortless Cleaning with Tubular Drag Conveyors
Compared to most conveyor systems, tubular drag conveyors are also easier to clean. Firstly, you don’t need to shut down the entire system and disrupt operations. Instead, polyurethane wiper discs are attached to the cable and left on to constantly keep the stainless conveyor tube clean of residual material and free of material buildup. This makes the system “self-cleaning.” Alternatively, and for extra measure, washdown systems can also be installed where water lines are attached to an outlet and inlet. Because the conveyor is enclosed, the washdown cycle is self-contained and doesn’t cause water to spray everywhere and make a mess.
Gentle and Contamination-Free Conveyance
Tubular drag systems were also engineered to move materials gently, making them ideal for the conveyance of fragile nut material. Materials glide into the system by entering the conveying tube gradually without using air or force.
Tubular drag conveyors are designed to prevent attrition by ensuring the nuts stay intact during transport while also keeping the materials contamination-free. Unlike open conveyor systems, the enclosed nature of tubular drag systems means no dust can escape during transport and leave an unsanitary and potentially dangerous coating of dust on the floor and process equipment. The result is a safer, cleaner, and dust-free work environment.
Unrivaled Energy Efficiency and Versatility
Cable and tubular drag conveyors are also ten times more energy-efficient than pneumatic conveyors because they operate on variable speed motors, which consume minimal power. They are also highly customizable and can be designed with conveying tubes that are straight or curved and laid out in various configurations. This means having the ability to maximize overhead space with a custom conveyor belt.
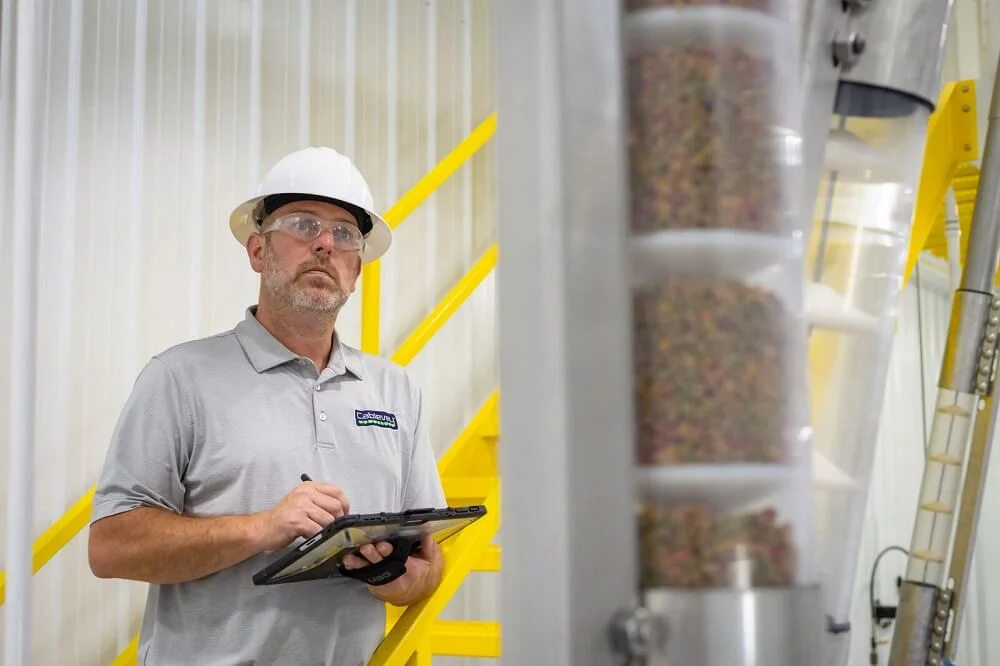
Choosing the Right Conveyor for Nut Processing Operations Means Enhancing Safety and Efficiency
To increase workplace safety and productivity, you need to modernize your operations through automation conveyor systems and minimize the manual handling of raw materials. You can achieve this by investing in the right conveyors for your application.
Because product loss is incredibly costly, choose the correct conveyor for your operations as early as possible. It is better to spend on the right system now than suffer the consequences and pay for it later. Settling for a cost-effective or unsuitable conveyor could result in costly product wastage, injury or accidents, and low-quality products, but it could cost you your company when you fail food safety inspections.
While there are a lot of conveyor manufacturers making conveyor systems that can be used in nut processing plants, remember that not all of them are safe, gentle, or efficient. Recognize the unique requirements of the nuts you process to determine which conveyor equipment will help ensure you produce only the highest quality products.
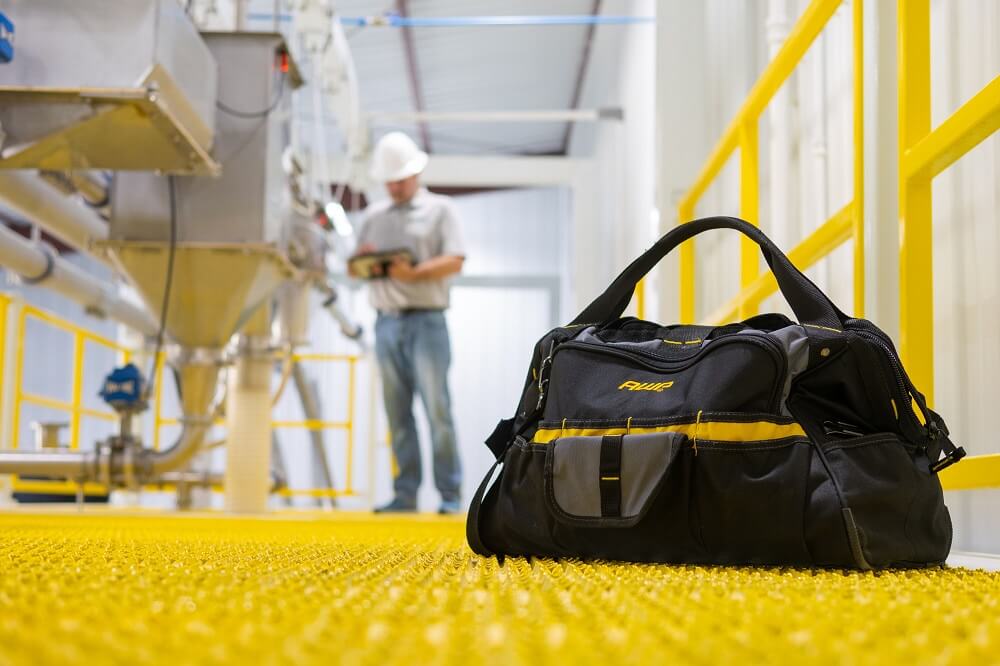
Cablevey Conveyors Is Your Trusted Partner for Optimal Nut Conveyor Solutions
What sets Cablevey apart is our commitment to delivering personalized solutions. We take the time to comprehend your nut processing facility’s layout, unique challenges, and operational requirements. Our team of experts collaborates closely with you to design a customized conveyor system that maximizes efficiency, optimizes available space, and enhances workplace safety.
If you’re interested in learning more about choosing the right conveyor system for transporting nuts in a food processing facility, contact Cablevey today. We offer a wide range of tubular drag and cable conveyor systems that are specifically designed to meet your needs and exceed industry standards.
FAQ
What Are Nut Conveyor Systems?
Nut conveyor systems are specialized equipment used to transport nuts within food processing facilities. These systems are designed to handle nuts gently, ensuring minimal breakage and maintaining product integrity.
Why Are Nut Conveyor Systems Important for Food Processing Facilities?
Nut conveyor systems play a crucial role in enhancing workplace safety and productivity while minimizing manual handling of raw materials. They help prevent product wastage, reduce the risk of accidents, and ensure high-quality products. Additionally, these systems are vital for complying with food safety regulations.
What Types of Conveyor Systems Are Suitable for Transporting Nuts?
Tubular drag conveyors and cable conveyors are highly recommended for transporting nuts. These systems provide a self-cleaning feature and gentle material handling, making them ideal for fragile nuts and minimizing contamination risks.
How Do I Choose the Right Conveyor System for My Nut Processing Operations?
When selecting a conveyor system, consider the specific requirements of the nuts you process. Look for equipment that is safe, efficient, and designed to meet the industry’s unique challenges. Cablevey offers a wide range of conveyor solutions tailored to nut processing needs.
What Benefits Do Tubular Drag and Cable Conveyors Offer for Nut Transportation?
Tubular drag and cable conveyors offer numerous advantages, such as energy efficiency, enclosed systems to prevent dust and contamination, and the ability to navigate turns gently. They also minimize breakage and ensure the highest quality of nut products.