Have you ever wondered how popular favorite snacks are made so quickly yet with consistent quality? Enter the world of conveyor systems – the backstage pass to the food production process. But what is the benefit of using a conveyor system in the food industry exactly? Stick around to learn more about these automated allies and how they minimize the risk of errors and contamination on various production lines.
What Are Conveyor Systems?
The conveyor system is a mechanical material handling equipment that moves a wide range of products from one part of the facility to the other. While conveyor systems were first invented to transport goods onto ships at ports, they are now used in various industries, including mining, agriculture, automotive, and the beverages and food production industry.
Conveyor systems have revolutionized the food industry by speeding up the transportation of materials between long distances, cutting down on human labor, and minimizing manual handling. Conveyor technologies allow for a more sanitary environment with less dirt getting into production areas that can lead to illness or contamination, which also helps increase product safety. To fully appreciate the benefits of food processing conveyor systems, we need to understand why they were invented and their role in food production.
History of Conveyor Solutions
The first mentions of conveyor technologies date back to 1795. A leather belt and wooden bed were used to make the first conveyor system. This technology was powered by hand cranks and pulleys. As The Industrial Revolution and steam power came into play, improvements in the primitive design of the first conveyor systems became noticeable. The British Navy started using steam-powered conveyors to load their ships in 1804.
Over the next 100 years, machine-powered conveyors started appearing in many different industries. Manufacturers began using different fabrics or a combination of synthetic materials for the belts. In 1901, Swedish engineering company Sandvik started making the first steel conveyor belt systems.
Conveyor systems have improved a lot over the years – these systems are no longer powered manually or by gravity. Nowadays, automated conveyor systems are commonly used in the food industry to improve the quality of food, efficiency of operation, productivity, and safety. Mechanical conveyors have a power mechanism that controls the conveying speed, a motor controller, and a structure that supports the conveyor. Of course, there are also the means to handle the material, such as a belt, tube, tray, or screw.
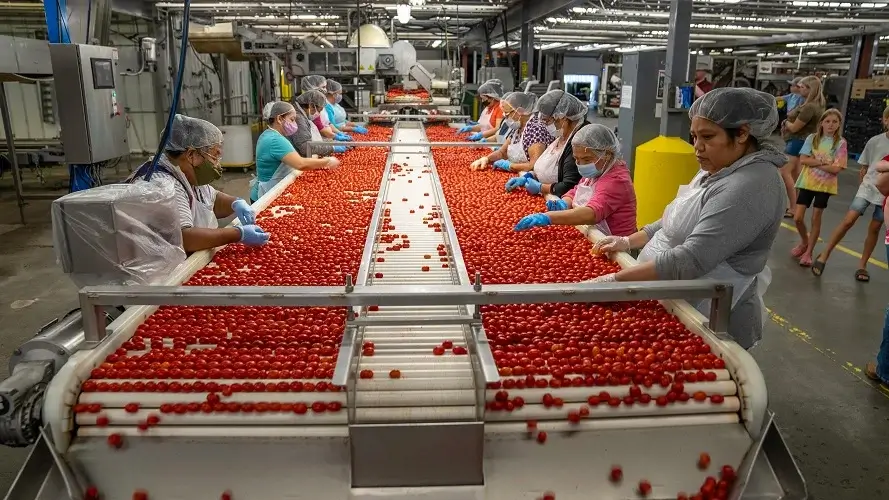
Conveyor Systems Today – What Are They Like?
The Conveyor Equipment Manufacturers Association (CEMA), the association that provides the conveyor industry with design, conveyor engineering, application, and safety standards, has defined over 80 types of conveyors. There are flatbed conveyors, chain conveyors, pallet conveyors, overhead conveyors, stainless steel conveyors, table-to-chain conveyors, custom conveyor systems, and more. Conveyor systems can be specified by load capacity, rated speed, throughput, frame configuration, and drive location.
In the food industry, the most common conveyor used today is the belt conveyor system. Other popular choices include screw conveyors, aero-mechanical conveyors, vibrating conveyors, flexible screw conveyors, and tubular cable drag conveyor systems. Today’s conveyor technologies allow for customized designs based on the client’s needs, including how far they need materials moved or at what speed these items will be traveling through the plant.
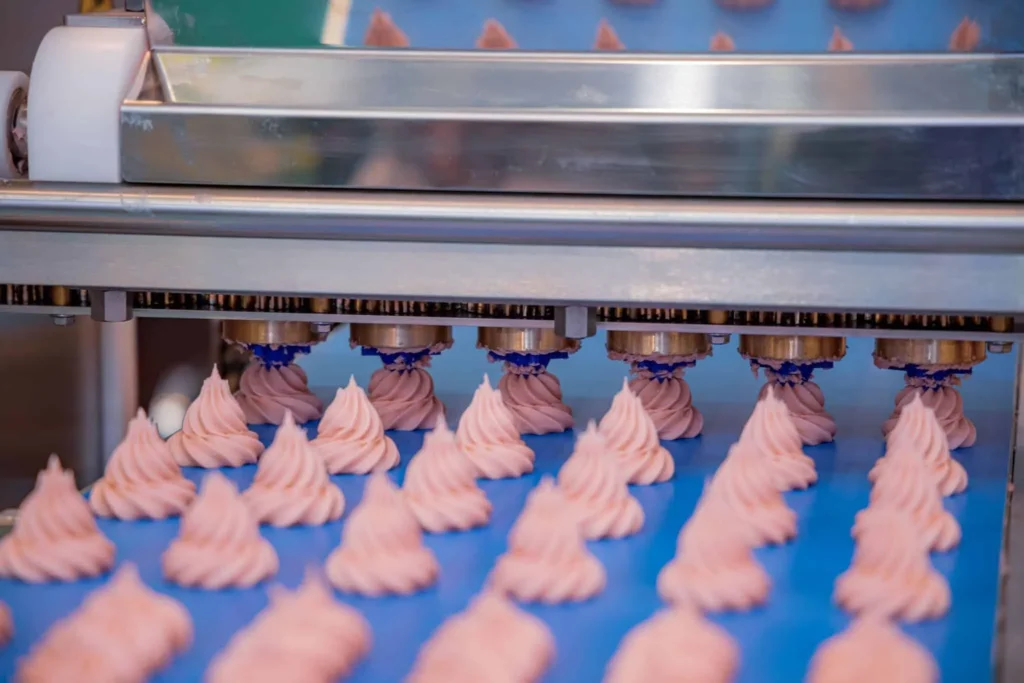
What Is the Benefit of Using a Conveyor System in the Food Industry?
When conveyors are designed, constructed, and installed to meet food production regulations, the result is a conveyance system that is safe, sanitary, and efficient. Here are the top benefits of using conveyor systems in the food industry.
Eliminating or Minimizing Manual Labor
Before conveyor systems, transporting materials from one level to another was done with human labor. It was strenuous and slow, forcing companies to spend a lot of money on labor costs. With the right conveyor system, food manufacturers can reduce employment costs, such as recruitment, wages, training, benefits, and retention.
Conveyor systems allow the automated transportation of materials between long distances that may be on varying elevations. Conveyors can be used to transport raw materials out of storage and into the production line, move products into other storage devices, move the finished product into the packaging line, or transport packaged products to shipping.
Reducing the Risk of Accidents
Food plants become safer and more productive with the right conveyor system. Installing a conveyor system means needing fewer workers, which in turn reduces the number of workplace accidents. Thanks to automation, employees can do their jobs without being exposed to risks that could get them injured or damage fragile materials. There is less demand (if any) for carrying heavy loads, repeating specific movements, and a significantly reduced chance of injury or disease.
Increasing Efficiency and Productivity
Industrial conveyor systems help save time by allowing materials to be moved between multiple levels quickly. Materials can move in different directions, which is useful when moving them between opposite ends of a processing plant. Because modern conveyor solutions eliminate manual unloading, there’s also no need to waste time monitoring unloads and workers. Conveyors have speed controls, which means materials are moved at optimal speed, reducing wastage or material loss.
Famously, Henry Ford was one of the first business owners to install a moving assembly line to mass-produce a vehicle way back in 1913. With this innovation, he reduced the time it took to build a car from over 12 hours to a mere one and a half hours! Imagine just what kind of productivity levels you can achieve with conveyor systems of the modern age.
Ensuring Food Safety and Maintaining Quality Standards
There are certain conveyors that are better for the food industry than others. For example, tubular drag conveyor systems are explicitly designed to be dust-free and contamination-free and to move food materials safely and efficiently. Product and material handling equipment must be easy to clean and kept free of contaminants when it comes to foods and beverages.
From small and powdered materials to sanitary or delicate materials, a cable tubular conveying system can move just about any food material that fits into a tube. What makes tubular drag cable and disc conveyor systems different is the technology that holds materials between discs within an enclosed tube. This design keeps breakage to a minimum and maintains a sanitary environment. Ensuring the plant environment is safe and hygienic helps the company comply with regulatory agencies like the FDA and USDA.
Contact Cablevey Conveyors to Learn More About Using Conveyor Engineering in the Food Processing Industry
Conveyors are excellent investments that help food production companies save on labor costs, improve processes and productivity, and maintain food quality standards. If you have any questions about using a conveyor system in your food production facility, please reach out to Cablevey Conveyors. We specialize in outfitting various food processing plants with top-of-the-line conveyors that help grow the business. Let us help you take your production process to the next level – contact us to learn more about our services and request a quote.
FAQ
How Do Conveyor Systems Enhance Food Production Efficiency?
Conveyor systems streamline the food production process, enabling rapid, precise movement of products along the production line. They reduce manual labor, mitigating errors and contamination risks. By automating complex and repetitive tasks, these systems ensure consistency in product quality, boost throughput, and allow workers to focus on more intricate, value-added tasks. This amplifies operational efficiency, ensuring that consumers receive quality products in a timely manner.
Are Conveyor Systems in the Food Industry Safe and Hygienic?
Conveyor systems are designed with safety and hygiene at their core. In the food industry, they minimize human contact with the products, drastically reducing contamination risks. Features like easy cleaning and maintenance, dust-free operations, and advanced materials ensure that the highest hygiene standards are maintained. They are compliant with regulatory standards, ensuring that food products are processed and packaged in a clean, safe environment.
How Have Conveyor Systems Evolved Over the Years?
Originating with wooden beds and leather belts, conveyor systems have come a long way. The Industrial Revolution introduced machine-powered systems, which evolved into today’s automated, efficient models. Modern conveyors, governed by associations like CEMA, boast over 80 types with varied load capacities, speeds, and configurations. Adaptations like flatbed, chain, and custom systems cater to diverse industrial needs, marking a significant evolution in design, functionality, and efficiency.
Can Conveyor Systems Be Customized for Specific Food Processing Needs?
Yes, customization is a hallmark of modern conveyor systems. They can be tailored to meet the specific requirements of different food processing tasks. With options like belts, vibrating, screws, and aero-mechanical conveyors, industries can select and customize systems based on load capacity, speed, and material handling needs. This ensures optimal efficiency, safety, and quality in the food production process, aligning with individual operational goals.
What Role Do Conveyor Systems Play in Ensuring Food Safety and Quality?
Conveyor systems are instrumental in upholding food safety and quality. In the food industry, designs like tubular drag conveyors ensure a contamination-free environment. These systems hold materials within enclosed tubes, minimizing breakage and maintaining hygiene. Compliance with regulatory standards like FDA and USDA is facilitated, as conveyor systems ensure that food materials are handled, processed, and packaged with the utmost care, maintaining their quality from production to packaging.