The right conveyor choice ensures efficient and safe transportation of ingredients and products. Surely, you also would want to maintain product integrity, comply with industry standards, and enhance overall productivity in food processing facilities. So, what types of conveyors are used in the food industry? Let’s explore the characteristics, applications, and advantages of each automated conveyor system and empower you to make an informed decision for your food processing facility.
What Types of Conveyors Are Used in the Food Industry?
Pneumatic conveyors, belt conveyors, bucket elevators, screw augers, and tubular drag conveyors are the most used types in the food industry. Each type serves specific needs, ensuring seamless and hygienic processes.
Conveyor technologies play a crucial role in the food industry, facilitating the efficient transportation of ingredients, finished products, and packaging materials. If you are operating a facility like this and are considering investing in a new conveyor system, it is important to choose the right type of conveyor for your specific needs. Let’s examine the characteristics and uses of each conveying type, as well as their advantages and disadvantages.
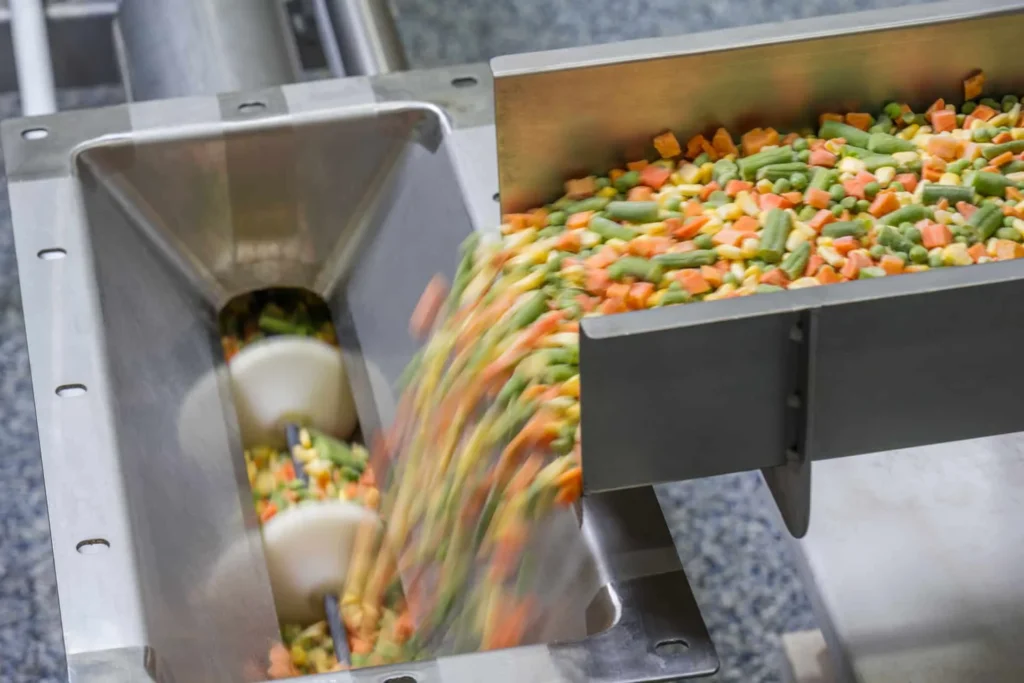
Pneumatic Conveyors Are Ideal for Handling Lightweight and Free-Flowing Materials
Pneumatic conveyor solutions use air pressure to move materials through a pipeline. They are commonly used in the food industry for the transportation of lightweight, dry, and free-flowing materials, such as grains, flour, and sugar. Pneumatic conveying systems can be either positive or negative pressure systems. Positive pressure systems use a blower or fan to push the material through the pipeline, while negative pressure systems use a vacuum to pull the material through the pipeline.
One advantage of pneumatic conveyors is their ability to transport materials over long distances and around obstacles, as they can operate horizontally, vertically, or at any angle in between. They are also relatively easy to clean and maintain, as there are few moving parts that come into contact with the material being conveyed. Pneumatic conveyors are also relatively low-cost and energy-efficient compared to other types of conveyors.
However, pneumatic conveyors are not suitable for all types of materials. They are not able to handle abrasive, sticky, or wet materials and can be prone to material segregation and degradation if the material being conveyed is not uniform in size or shape. Pneumatic food conveying systems also generate noise and can be prone to leaks if not properly designed and maintained.
In the table below, you can find all the pros and cons of these conveying systems.
Pros | Cons |
Long-distance transport | Not suitable for delicate materials |
Operation in any plane – horizontal or vertical | Can be noisy |
Easy to clean and maintain | Can leak |
Conveyor Belt Systems Transport a Wide Range of Materials
Belt conveyors are a type of materials handling system that uses a continuous loop of belt material to transport items from one place to another. They are commonly used as industrial conveyor systems for the transportation of a wide range of products, including raw materials, finished goods, and packaging materials.
A conveyor belt system can operate horizontally and at a slight incline. However, it’s not the best choice if you need vertical or steep angle conveying. One advantage of the conveyor belt is its versatility and adaptability to different environments and materials. They can be made of a variety of materials, including rubber, PVC, or polyurethane, to suit the needs of the specific product being conveyed.
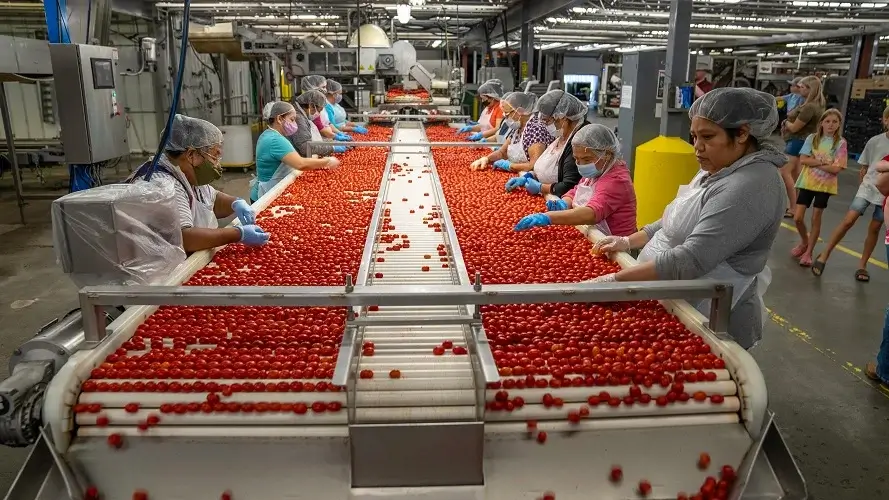
Customization Options for Belt Conveying Systems
Belt conveyor manufacturers offer various customizable features, including cleats, side walls, and v-guides, to prevent product spillage or slippage. They are also relatively low-maintenance and easy to clean, as they can be easily accessed for cleaning.
However, a belt conveyor system is not suitable for extremely hot or cold food handling and can be prone to wear and tear if the belt material is not properly maintained. Conveyor belts also require a certain amount of tension to operate correctly, which can be challenging to achieve in some environments.
Let’s check the table below with all the pros and cons.
Pros | Cons |
Highly adaptable to different environments and different materials for conveying | Not suitable for extremely hot or cold materials |
Can be customized with additional features | Not for tight floor spaces |
Easy to clean and maintain | Not for vertical or steep-angle conveying |
Bucket Elevators Are Quiet and Customizable
Bucket elevators consist of buckets attached to a moving belt or chain to lift materials vertically. They are commonly used for industrial purposes for the transportation of a wide range of bulk solids, including grains, flour, sugar, and similar. Bucket elevators can be either centrifugal or continuous, depending on the type of material being conveyed.
One advantage of bucket elevators is their ability to handle a wide range of materials and capacities, as they can be customized with different bucket sizes and shapes, belt or chain speeds, and discharge heights. Bucket elevators are also relatively quiet and can operate in a small footprint, making them a good choice for facilities with limited space (though they are best used as a vertical conveyor).
However, bucket elevators have some limitations. They consist of a large number of moving parts and are notoriously difficult to clean and maintain as they require quite a bit of downtime for disassembly. They are also not ideal for conveying blends. The way the material is “thrown” from the buckets into the next machine in the process can compromise blends and lead to poor final product quality.
Let’s take a look at the table below with the pros and cons of this conveying system.
Pros | Cons |
Energy efficient | Extremely difficult to clean and maintain |
Can be adapted to a wide range of materials and capacities | Can compromise blends |
Ideal for vertical conveying | Not the best choice for horizontal conveying |
Screw Augers Are Manufacturing Conveyor Systems Suitable for Operating in a Single Plane
Screw augers are a type of automatic conveyor system that uses a helical screw blade, or an auger, to move materials through a trough or tube. They are commonly used in the food manufacturing industry for the transportation of semi-solid materials, such as meat, animal feed, aggregates, and similar.
However, there are some limitations to using a screw conveyor. One limitation is that they are not suitable for spaces where the conveyor needs to operate in multiple planes, such as around corners or curves. Screw augers are generally limited to operating in a single plane, as the screw blade is not designed to bend or flex.
Another limitation of screw augers is that they can cause a high level of material degradation, particularly if the material is fragile or easily crushed. The screw blade can apply a significant amount of force to the material as it moves through the trough or tube, which can result in breakage or damage.
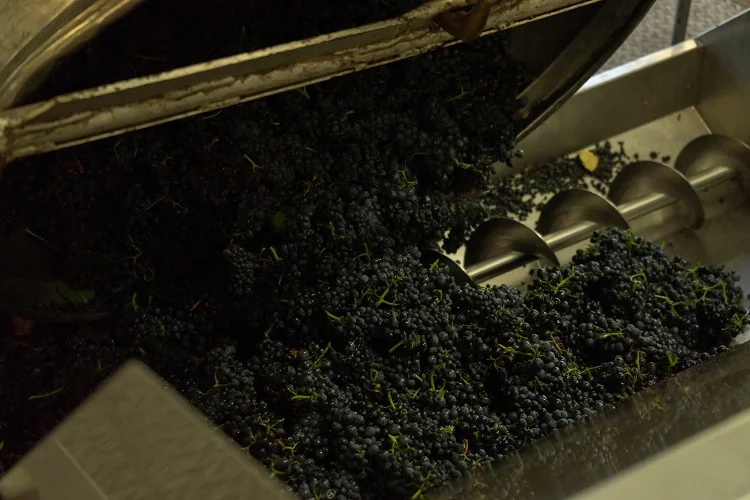
Energy Efficiency Challenges With Increasing Incline
In terms of energy efficiency, a screw auger conveyor is most efficient when operating at a low incline. As the incline increases, the energy efficiency of the food conveying system decreases due to the increased resistance of the material being conveyed. This can make screw augers less cost-effective for applications that require a high incline.
In the table below, you can find some of the most important pros and cons.
Pros | Cons |
Energy efficient at low inclines | Causes high material degradation |
Good for conveying semi-solid materials | Not flexible – unsuitable for conveying in multiple planes |
Energy efficiency decreases as the conveying incline increases |
Tubular Drag Conveyors Ensure Gentle Converting
Tubular drag cable and disc conveyors (a type of tubular drag conveyors) use a sealed cable and a series of circular discs spaced along that cable to move materials through an enclosed tube. They are ideal for transporting fragile materials, such as coffee beans, nuts, snack food, breakfast cereal, frozen food, and similar.
One advantage of a tubular conveyor is its ability to gently convey delicate materials without causing damage or breakage. There is no crushing, throwing, or even jostling of the material as it flows through the conveying system. The enclosed tube protects both the conveyed material from outside contamination and the facility environment from getting dusty or dirty from the conveyed material.
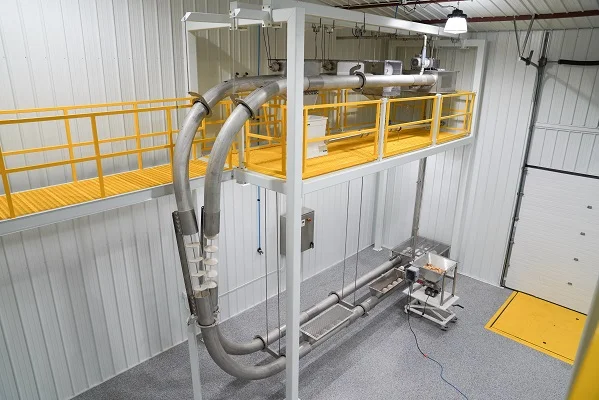
Advantages of a Tubular Conveying System for Space Efficiency and Maintenance
These conveying systems are also great for tight floor spaces, tight sweeps, and high inclines, as they can operate in a small footprint and can handle steep inclines without causing material spillage or segregation. They are also easy to clean and maintain, especially if they come with a clean-in-place (CIP) mechanism. In terms of energy efficiency, tubular drag cable and disc conveyors are a good choice, as they require minimal power to run. They are also relatively quiet.
Here’s the table with the pros and cons of this conveying system.
Pros | Cons |
Gentle conveying of fragile materials | Not good for sticky materials |
Energy efficient | |
The enclosed tube reduces the risk of contamination | |
Great for tight floor spaces – extremely flexible design | |
Easy to clean and maintain |
Choosing the Optimal Conveyor System for Your Food Processing Needs
There are several types of conveying solutions to choose from, each with its unique characteristics and applications. If you work in a food processing facility and are considering investing in a conveyor engineering system, it is important to choose one of the right conveyor systems manufacturers for your specific food product and needs.If you handle delicate materials, such as coffee beans, nuts, snack food, breakfast cereal, or frozen food, consider purchasing a tubular drag cable and disc conveyor to gently convey your materials without causing damage or breakage. Contact Cablevey Conveyors today to learn more about tubular cable and disc conveyors and how you can make the best use of them in your production facility.