In the 21st century, conveyor systems are found in a wide range of industries, such as mining, agriculture, logistics, automotive, food processing, and, of course, pet food production. Regardless of their type, process equipment, or component materials, mechanical conveyors – including the pet food conveying system, have helped the modern world in terms of streamlining and optimizing production as well as cutting down costs.
The History Behind Bulk Material Handling Equipment
Even before the appearance of the steam engine and the onset of the Industrial Revolution during the mid-18th century, engineers developed rudimentary conveying systems in an attempt to streamline the process of moving different types of material from one place to another. These early product handling systems were made out of wood and powered by hand via a network of pulleys and hand cranks. With industrialization, machine-powered conveyors began appearing in different configurations across a multitude of industries.
It was at the start of the 20th century when Sandvik, a Swedish engineering company, began producing the first-ever steel conveyor systems. Instead of materials such as leather, rubber, or canvas, synthetic and plastic belting was also introduced over the coming years.
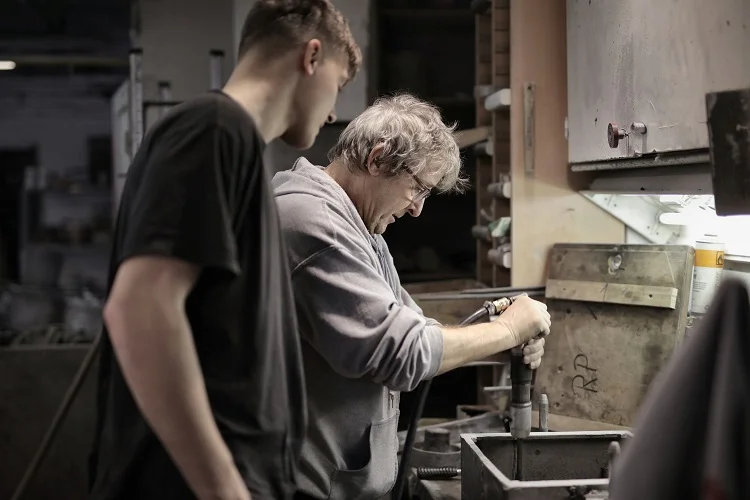
Pet Food Market Trends
The global pet care industry has surpassed $125 billion as of 2018. By 2025, it’s expected to grow at about three times the pace of that of the packaged food industry, at a compound annual growth rate (CAGR) of 6%. However, in light of the recent COVID-19 pandemic, US retail sales of pet products and services are expected to fall by 17% in 2020, as compared to the 5% growth anticipated prior to the pandemic. Nevertheless, pet food sales are still expected to grow by 4% in 2020, albeit at a slower pace than the original forecast of 6% anticipated prior to the pandemic.
Still, the global pet food market has increased significantly. North America and Europe make up the majority of the market share of the pet food industry, with $33 billion and $23 billion, respectively. The United States is, by far, the largest consumer of pet food in the world, followed in a distant second place by the United Kingdom. A fast up-and-comer, however, is Brazil in third place. The South American nation has an annual growth rate of 5.5% and a market share of $4.3 billion.
The Factors That Have Influenced the Trends
Among the major factors influencing this pet food trends and market growth are the increase of nuclear families around the world, the adoption of more pets per family, rapid pet humanization, premiumization, as well as an increase in owners’ awareness regarding their pets’ overall health. Over the past three decades in the US, pet ownership has risen from 56 to 68%.
Currently, there are an estimated 85 million households with at least one pet. Millennials and GenZers account for about 62% of nationwide pets, whereas Baby Boomers make up 32%. Modern pet owners hold less interest in traditional pet foods and seek healthier ingredients while also demanding higher transparency when it comes to nutritional labels. The main concerns that can put a dent in this growth include pet obesity, as well as the occasional pet food recalls heard in industry news.
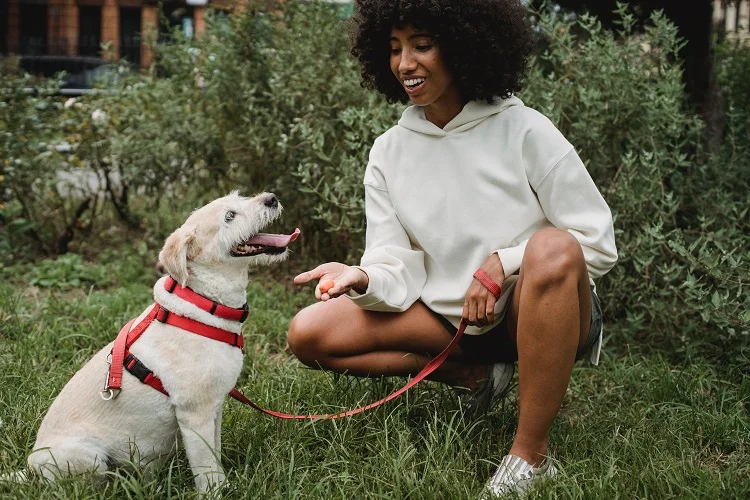
Pet Food Safety and Sanitary Compliance
Regarding the human and pet food manufacturing industries, the potential liabilities concerning failure to comply with safety and sanitary regulations will often go beyond just product recalls and subsequent costs. Material accumulation in food conveyors can result in cross-contamination as well as allow for microorganisms to develop. Neither case is easily detectable with the naked eye, significantly increasing the likelihood of tainting the entire production line.
The Importance of Safety and Sanitary Procedures
Today’s technology is, however, able to quickly trace any form of human or pet food contamination back to its source, resulting in product recalls, negative press, or even worse. The Peanut Corporation of America’s (PCA) 2008 tragedy is a stark reminder of what can happen when safety and sanitary procedures are not strictly followed and enforced. As a result of salmonella contamination of a particular batch of peanuts, over 700 people developed food poisoning, and nine people died.
The silver lining of this unfortunate event was the 2011 enactment of the Food Safety Modernization Act (FSMA), the largest and most comprehensive food safety reform in the United States over the past 70 years. With it, far stricter regulations were put in place, minimizing the risk of a similar PCA incident. The pet food industry is not exempt from its own share of similar events either. Cases of cross-contamination or wrong ingredient mixes ended up on the market and killed several pets.
The US Food and Drug Administration (FDA) Response
In response to this, as well as the increasing concerns about pet well-being, the US Food and Drug Administration (FDA) has set stricter regulations regarding pet food labeling and ingredient use. All of this said, there’s mounting pressure on the pet food manufacturer to shift their attention away from reacting to issues regarding contamination and focus more on prevention. An effective way of doing this is by choosing the most sanitary conveyor system that’s able to keep any contamination issues at an absolute minimum.
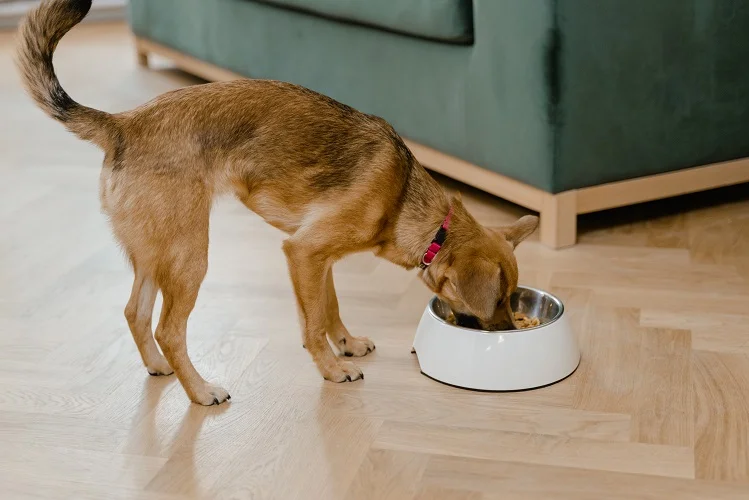
Common Types of Conveyor Systems in the Pet Food Industry
There are numerous types of conveyor systems currently available on the market. Each of them has its special uses and type of material handled. Below, we will be focusing on some of each type of industrial conveyor belt for food used for pet food product processing.
- Bucket elevators – traditionally, bucket elevators were the most common pet food conveyors. They consist of a series of buckets attached to a belt conveyor system and a series of pulleys at the top and bottom of the installation.
- Chain disc conveyors – this type of conveyor system has several design features to keep materials safe during transport. These can also move materials in any direction, either in a vertical or horizontal motion, and typically have multiple inlets and discharges.
- Screw conveyors – also known as auger conveyors, screw conveyors shouldn’t be confused with spiral conveyors. An auger conveyor uses a helical screw element that rotates around a central shaft, moving one pitch with every revolution.
- Pneumatic conveyor systems – they work by transmitting a propulsion force of air from a blower, fan, or compressor and moving the materials through an enclosed tube.
- Gravity roller conveyors – such conveyors transport materials with sufficient weight on an inclined runway. These systems are unpowered and move prepared foods on a downward path.
- Cable and disc tubular drag conveyors – these conveyors are specifically designed to handle different types of materials to maintain food safety. They hold materials between discs located in an enclosed tube. Pet foods of different granularities and densities are handled gently, gliding through the system without the need for air or force to propel them forward.
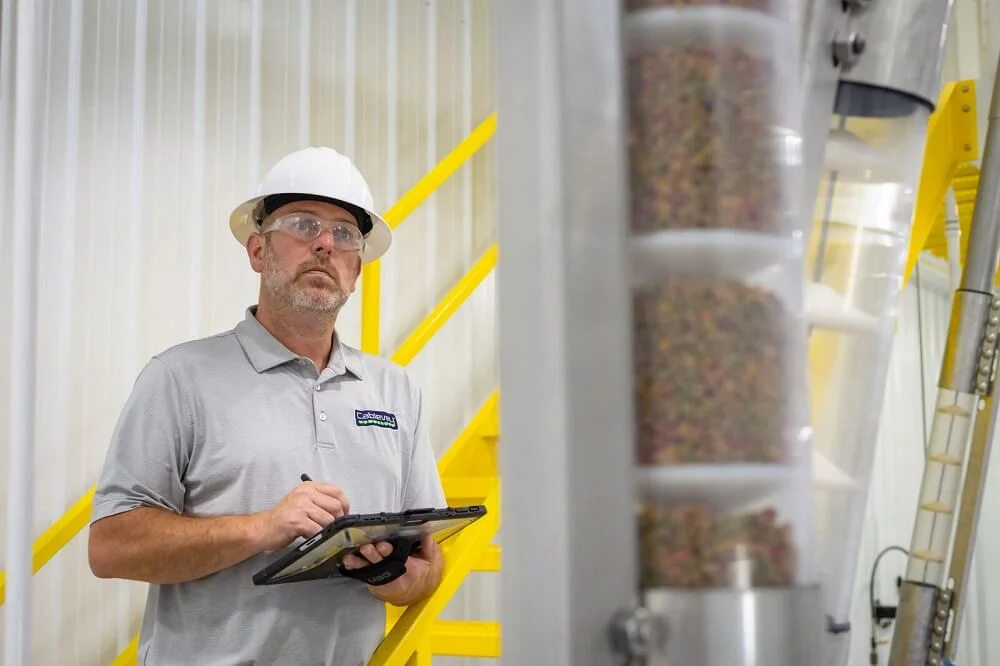
Guidelines for Choosing a Top Conveyor for Your Pet Food Processing
There are several factors and design considerations that need to be assessed whenever a dry pet food manufacturer chooses a conveyor system for their facility. First of all, the conveyor system needs to be configured to operate within the facility’s physical layout. This requires a fair degree of flexibility to maneuver the plant’s inclines, declines, turns, lifts, and flights. While some pre-engineered conveyors are highly modular and allow for a high degree of customization, others are relatively fixed. It’s important to determine how difficult it will be to modify a custom-designed conveyor and at what cost.
Consider Whether Cleaning Is Straightforward
Maximizing production should never come at the expense of thorough cleaning. Product contamination will be far costlier in the long run than any amount of time saved when neglecting proper sanitation. As such, the system needs to be easy to clean while facilitating fast and seamless line changeovers. Sacrificing safety and hygiene in favor of maximizing immediate benefits is shortsighted and potentially dangerous.
Another Factor – Maintenance
On a somewhat similar note, standard preventive maintenance should also be given priority. Any system failures need to be anticipated, even for the most reliable automation conveyor systems. As such, the frequency and ease of access ought to be considered as well. A system that needs continual maintenance and replacement parts will tend to affect your production and overall costs. Getting everything up and running quickly is, therefore, critical for your success.
Depending on the exact type of pet food you are producing, you need to ensure that the system you choose will not result in extensive product breakage and degradation. This will lead to product waste, increased operating costs, and even the possibility of contamination.
Requirements for Energy Efficiency in Operations
Operational energy efficiency requirements should also be taken into account. You need to compare the different types of conveyor systems suitable for your needs, their capacity for customization in regard to your facility’s layout, as well as the amount of horsepower required to move the desired material capacity. Shortening the distance with custom conveyor belt systems even by as much as 10% can significantly reduce your energy bills over the long term and lower your overall carbon footprint.
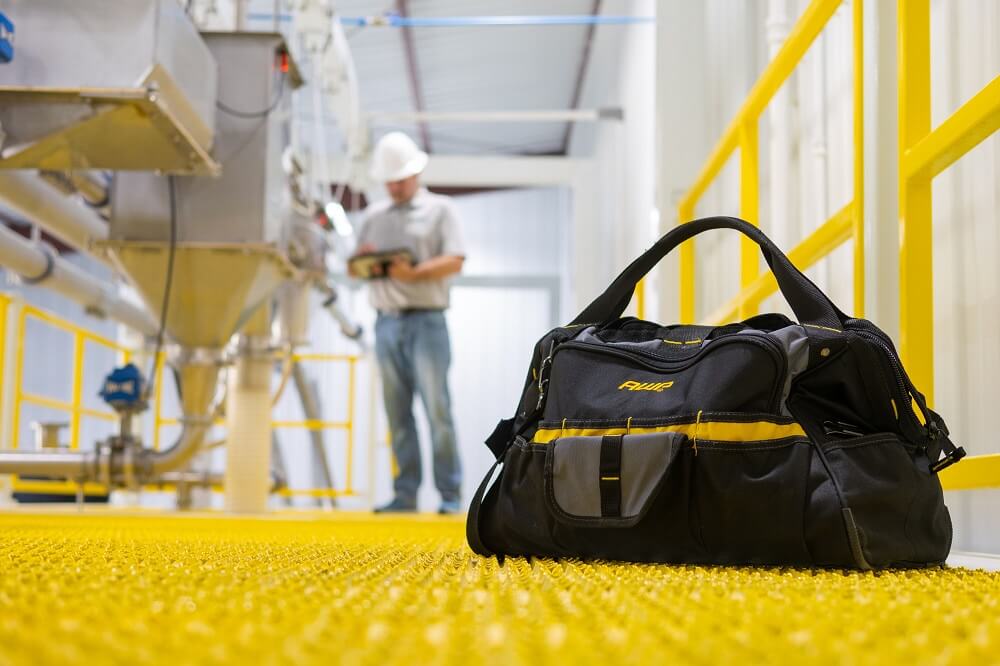
What Is The Best Type of Conveyor System?
When it comes to pet food production, the best processing systems are tubular drag cable conveyors. While other standard conveyor systems used in the pet food industry have issues with product attrition, cable and disc tubular drag conveyors are custom designed to minimize it. In addition, being an enclosed tube, there is no risk of any material dust escaping into the facility’s environment. Dust and fines are captured in a specific box for release under your control.It’s also important to note that tubular drag conveyors are able to transport most types of dry and moist pet food, regardless of whether they are dry, cooked, chopped, extruded, or powdered. They also reduce the incidence of any potential health hazards or the potential for dust explosions. This makes them an excellent option for carrying bulk materials in the pet food industry.
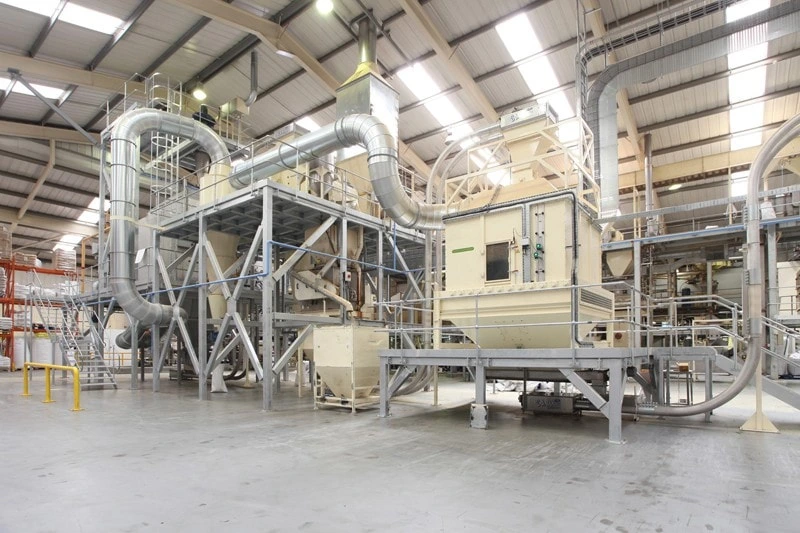
The Benefits of Cable and Disc Tubular Drag Conveyors
Pet food manufacturers are adding an increasing number of ingredients to their formulas and recipes. Similarly, they are using differently-sized and configured packages. As such, they also need a higher degree of flexibility from their conveyor systems, able to handle this diversity. Other concerns are in regard to product integrity, system maintenance, sanitation, and maximizing the floor space. So. let’s examine all the benefits of these systems for food processing.
Most types of pet food are made of fragile materials. Fish food, in particular, is most prone to breakage, affecting packaging lines and scalability. Factors such as friction-induced separation, high conveyor speeds, sudden temperature fluctuations, poor inlet design, and more add to this problem. Aside from the wasted pet food product and increased costs, material degradation can also increase the incidence of contamination or microbial growth. Tube conveyors have a sanitary design that minimizes any product breakage.
Another significant benefit concerns the nutritional mix and how pet food manufacturers need to maintain it throughout the entire process. Premiumization plays a key role in customers’ selection of pet food these days, meaning that they expect quality consistency with every purchased item. But since pet food tends to have ingredients of variable granularities and densities, separation issues can affect proportional accuracy.
Cablevey conveyors are far better suited than buckets, pneumatics, augers, and other systems in this regard. Our system moves material blends without actually changing the ratios designed by the nutritionist and employed by the manufacturer.
Being enclosed systems with minimal moving parts – basically, cable, discs, and a sprocket wheel, tubular drag conveyors don’t generate any fugitive dust and eliminate any chance of spillage or product loss. There’s also the minimum chance of cross-contamination, something that is relatively common when dealing with other conveyor systems. With minimal cleaning, tube conveyors will be as good as new after every line changeover.
Cable and disc tube conveyor systems can be customized to maximize the floor space of any facility. Different tube materials and diameters can be used for a wide range of applications and pet food products. The same thing applies to all components like vibratory feeders, transfer systems, and all sorts of other modern process equipment.
In addition, tube conveyors also use smaller drives than chain-disc conveyors or bucket elevators. Aside from some periodical maintenance checks of the discs, cable couplings, and several other components, there’s not much else in terms of maintenance. If a disc or other component becomes damaged, there’s no need to replace the entire cable system – just the damaged part. Lastly, these tubular conveyors are more energy-efficient than other systems with similar purposes.
Drawbacks of Each Pet Food Conveying System
Pet food is generally fragile and needs gentle transportation so as to ensure minimal breakage during processing. This is one area where bucket elevators, chain-disc conveyors, pneumatic conveying systems, and auger systems tend to fall short. Buckets, for instance, are also notorious for their difficulty to clean, and we’ve already established the benefits and importance of a clean conveyor belt system. Wet and canned pet food tends to be unsuitable when it comes to bucket elevators, particularly for this reason.
Pneumatic conveyor systems, on the other hand, are more suited for powdered materials but have a high incidence of breakage. When transporting solid materials with pneumatic systems, there’s also a higher probability of product blend separation. Chain-disc conveyors, however, can process a wider array of pet food material. Still, they do have a tendency to grip on solid and fragile products, also resulting in degradation and waste.
These systems also use chain links that occupy more space in the enclosed tube and consume, on average, two or three times more energy than other alternatives.
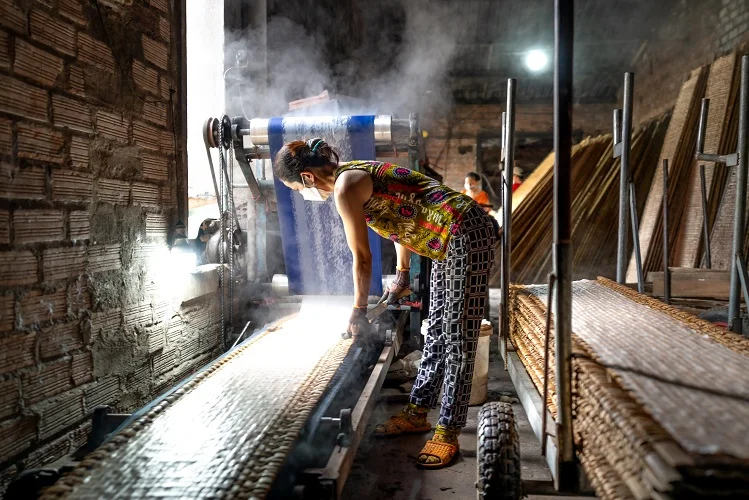
Cleaning Cable and Tube Conveyors
If pet food manufacturers run multiple products on the same lines, these need to be cleaned between changeovers. Bucket elevators and other systems require extensive downtimes when cleaned, which will translate into lost revenue. Tubular cable conveyors, however, comply with all FDA sanitation requirements. Components contain a special polymer-coated 304/316 stainless steel, which is highly corrosion-resistant. With every conveying cycle, the inside discs will eliminate material fines and waste products.
Wet or dry cleaning accessories can also be attached to the cable with relative speed, making it incredibly easy to provide thorough cleaning of the entire system. Cablevey conveyors offer both wet and dry tube conveyor cleaning options. A more basic method of internal tube cleaning is by not using any liquid materials. When dry cleaning, this process includes several steps and pieces of equipment. On the other hand, wet cleaning is available for 4″, 6″, and 8” diameter systems, and it’s comprised of several steps. All these steps are shown in the table below.
Type of Cleaning | Mechanism | Description |
Dry cleaning | Air knife | Being a line insert, the air knife blows compressed air to eliminate any accumulated fines found on the discs and cable. |
Dry cleaning | Brush box | The brush box is a line insert that cleans discs of any residual fines using 2 poly brushes. |
Dry cleaning | Sponge disc and sanitizing cleaner | Having an applied cleaning agent, a disposable sponge disc is run through the entire tube system. The sponge is then discarded. |
Dry cleaning | Urethane wiper disc | This wiper disc will squeegee away any remaining particles within the system; the urethane disc is a wider diameter than the tube it passes through, acting a “pig” to pull through and clean out any residue. |
Wet cleaning | Initial water rinse | Water will be introduced to rinse out the inside of the tube and all other components. |
Wet cleaning | Foam agent | A foam cleaning agent is introduced into the tubular system, cleansing all internal parts. |
Wet cleaning | Sanitizing rinse | A sanitizing rinse solution will run through the entire system, flushing out any remaining debris and contaminants, as well as the previous foam agent. |
Wet cleaning | Final water rinse | A final rinse of hot water will make the system and its components production-ready. |
Cable and Disc Tube Conveyors in Pet Food Production – Safety, Efficiency, and Sanitation
While there are a lot of conveyor manufacturers making conveyor systems that can be used in the pet food industry, not all of them are safe, gentle, or efficient. When it comes to pet food production, no system is better and more efficient than cable and disc tube conveyors. They are in line with all safety and sanitary regulatory standards, minimize material degradation, eliminate the possibility of cross-contamination, and are the fastest and easiest to clean of all other conveyor systems.
Ready to optimize your pet food production line with the highest safety and efficiency standards? Contact Cablevey Conveyors today and experience the difference provided by our industry-leading cable and disc tube conveyors, designed to maximize productivity while adhering to the strictest sanitary regulations. Don’t compromise on quality — let’s get started on your custom conveyor solution now.
FAQ
What Makes Cable and Disc Tube Conveyors Better for Pet Food Production?
Cable and disc tube conveyors are specially designed to be safe, gentle, and efficient. They minimize material degradation, eliminate cross-contamination risk, and are built to meet stringent safety and sanitary regulatory standards. Furthermore, they are the fastest and easiest conveyors to clean, making them a highly efficient choice for pet food production.
Are Cablevey Conveyors’ Systems in Line With Safety and Sanitary Regulations?
Absolutely, Cablevey Conveyors’ systems strictly adhere to all relevant safety and sanitary regulations to ensure the highest quality standards for pet food production.
Can Cablevey Conveyors’ Systems Be Used in Other Industries Besides Pet Food Production?
Cablevey Conveyors offers a wide range of conveyors suitable for various industries. Each system is designed to meet specific operational needs and safety standards.
How Do Cable and Disc Tube Conveyors Prevent Material Degradation and Cross-Contamination?
These systems are specifically designed to move products gently, reducing the chances of material degradation. As for cross-contamination, our systems feature easy-to-clean designs that help ensure a clean and sanitary process.
How Can I Get Started With Cablevey Conveyors?
To get started with Cablevey Conveyors, you can contact us through our website or directly call our customer service team. We’ll help identify the best conveyor system for your production line and guide you through the process of installation and operation.