In the fast-paced realm of material handling within food processing facilities, choosing the right conveyor system is pivotal. How is a tubular conveyor different from a screw conveyor? This question forms the cornerstone of our exploration. While both can get the job done, in this blog post we’re going to dive into why a tubular cable and disc conveyor is the better option when it comes to handling delicate materials.
How Is a Tubular Conveyor Different From a Screw Conveyor?
A tubular conveyor differs from a screw conveyor in design and functionality. Utilizing a tubular casing with a cable and disc system, these conveyor technologies offer gentle material handling, minimizing damage and ensuring contamination-free operations. In contrast, traditional screw conveyors may risk product integrity through abrasive rotation, making tubular industrial conveyor systems the superior choice for delicate materials in various industries, particularly in food processing.
Understand the Advantages of Tubular Cable and Disc Conveyors in Food Processing Facilities
When it comes to moving materials in a food processing facility (or any other kind of facility), automated conveyor systems are a game changer. But not all of them are created equal. Two popular options for food processors are tubular cable and disc conveyors and screw conveyors.
We’ll compare the design, material handling capabilities, and maintenance and cleaning requirements of both types of conveyors and show you why a tubular cable and disc conveyor is the superior choice for food processing facilities. So, let’s get started! Here is a comprehensive breakdown of the main differences between an auger conveyor (screw conveyor) and a tubular conveying system.
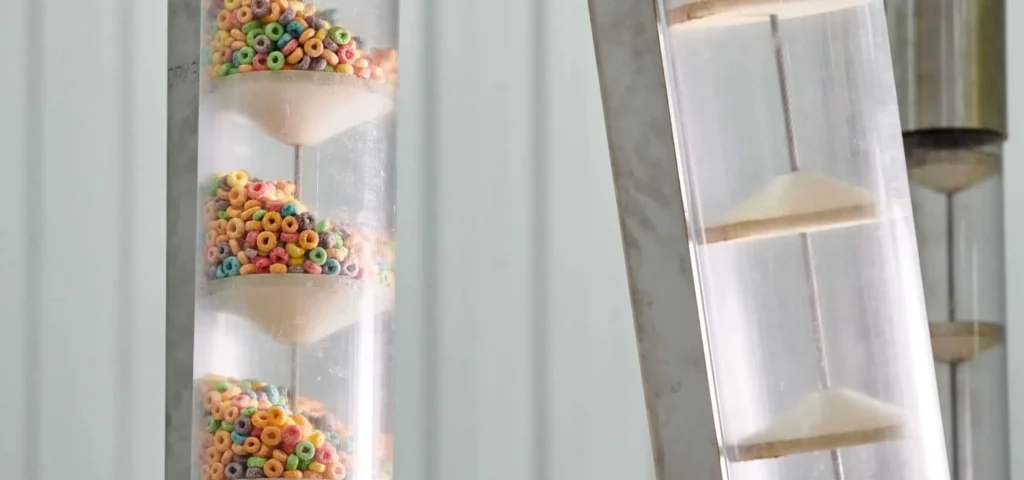
Design and Construction of Both Mechanical Conveyors
The design and construction of a conveyor stand as the foundational elements that define its operational prowess. After all, the operational efficiency and effectiveness of the entire setup depend precisely on these two features. This being said, let’s take a deeper look at them.
Tubular Cable Drag Conveyor Is Made from Stainless Steel and Can Be Customized
A tubular cable and disc conveying system is a mechanical conveyor made up of a tubular casing with a cable running through the center. The cable is made from stainless steel and is sealed in nylon, meaning it doesn’t come into direct contact with the conveyed material. Solid circular discs are attached to the cable at regular intervals, and these discs act as carriers for the materials being conveyed.
The tubular design helps to protect the cable and the conveyed materials from external factors, such as dust and debris. The tube also helps to contain the material, reducing the risk of spills or loss of product. The cable and discs are driven by a motor, which powers the movement of the conveyor.
The tubular cable and disc conveyor can be customized to suit the specific needs of the application, such as the diameter of the tube, the distance between the discs, and the speed of the conveyor. It is best suited for conveying the following bulk material options:
Screw Conveyor Is Great for Conveying Materials Short Distances
A screw conveyor is another mechanical device that uses a spiral shaft with a helix (auger) that rotates within a tube or trough (which is how we get a tubular screw conveyor and a trough screw conveyor). The helix is the component that moves the material through the conveyor.
The screw conveyor can be inclined or horizontal. The material is fed into the conveyor at one end and is moved along the conveyor by the rotation of the helix. The conveyor can be powered by a variety of means, such as an electric motor, a gas engine, or a hydraulic motor. Typically, an inclined screw conveyor requires more power to operate than a horizontal screw conveyor because the material is conveyed against the forces of gravity.
The screw conveyor’s design allows for the efficient movement of materials over short distances. The open design of the trough version of the auger conveyor allows for easy access to the interior for cleaning and maintenance. Screw conveyors are most commonly used to convey both sluggish and free-flowing materials, such as:
- Grain,
- Animal feed,
- Meat,
- Bone meal,
- Boiler ash,
- Food waste,
- Municipal solid waste.
Material Handling Capabilities Determine What Kind of Products Your Conveyor Transport
This feature stands as the heartbeat of any conveying system, defining its ability to transport diverse materials with precision and care. The effectiveness of a conveyor is profoundly influenced by how well it can handle materials – be it delicate, bulky, or free-flowing. The choice of conveying technology, especially in the hands of more traditional belt conveyor manufacturers, directly influences the integrity of conveyed goods, production efficiency, and the overall success of conveyor belt systems in various industrial applications.
Tubular Drag Conveyor Handles Fragile Materials Without Damage
One of the key advantages of tubular drag conveyors is their ability to handle delicate materials without causing damage. The design of the conveyor allows for a gentle material handling process that minimizes the risk of damage. As mentioned above, the discs that are attached to the cable are carriers for the conveyed material. These discs gently push the material forward without any jostling or breakage.
The spacing between the discs is such that the material is practically not moving while being conveyed, which means that it doesn’t experience any unnecessary agitation that could cause damage. Material breakage is kept to a minimum. In addition to this, the conveyor’s speed can be adjusted to match the fragility of the conveyed product, ensuring that it is handled as gently as possible.
Screw Conveyor Isn’t Suitable for Conveying Delicate Products
Unlike in a tubular cable and disc conveyor, the rotation of the helix within the screw conveyor can cause damage to fragile materials, such as nuts, coffee beans, snack foods, and similar. The rotation of the helix can cause abrasion or breakage of delicate materials due to the friction between the helix and the material. Essentially, the conveyor blade is slicing through the conveyed material, ruining its integrity.
Consequently, using a screw conveyor to handle delicate or friable materials can lead to loss of product, decreased product quality, and increased maintenance and cleaning costs. It’s important to consider these factors when choosing an automated conveyor system for delicate materials.
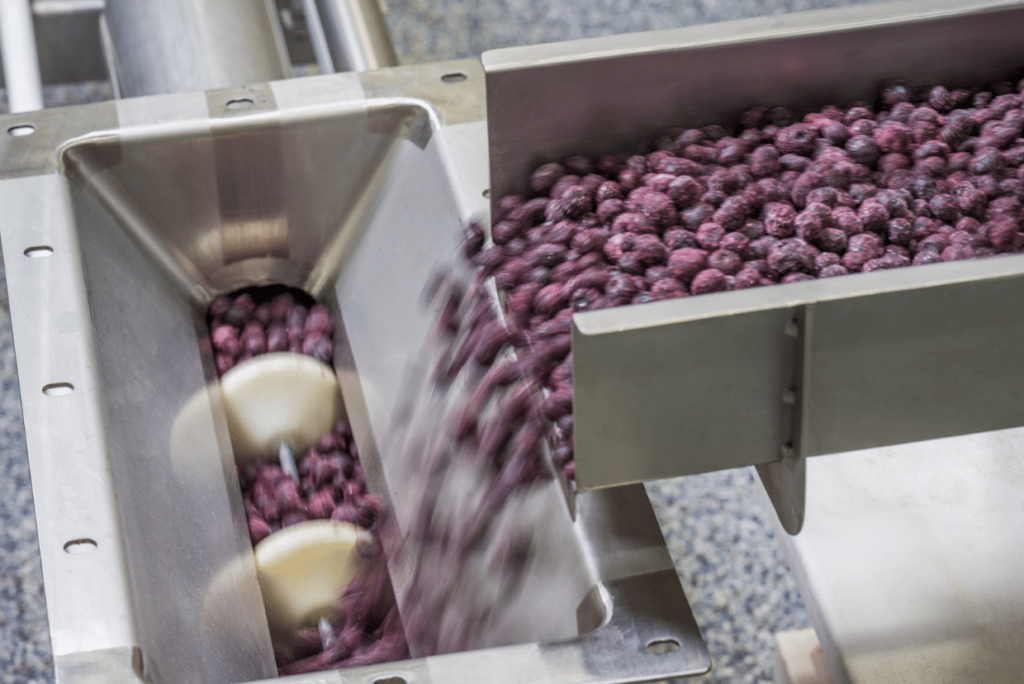
Maintenance and Cleaning Ensure Conveyor System Resilience
These aspects are the guardians of operational continuity, ensuring the sustained efficiency and longevity of conveyor systems. Maintenance activities safeguard against wear and tear, minimizing the risk of unexpected breakdowns that could disrupt production.
Simultaneously, well-structured cleaning conveyor belts play a pivotal role. This process ensures the thorough removal of residues and contaminants, serving as a bulwark against potential cross-contamination and preserving the integrity of conveyed materials from start to finish.
Tubular Drag Conveyor Is Easy to Maintain
These tubular mechanical conveyors, a testament to precision in conveyor engineering, are meticulously designed to minimize downtime during essential maintenance and cleaning routines, ensuring a continuous and smooth production flow. One of the key features that make maintenance and cleaning easy is the conveyor’s enclosed tubular design, unlike the more traditional belt conveyor system.
It allows for easy access to the interior of the conveyor. Additionally, many tubular cable and disc conveyors are equipped with special “clean-in-place” mechanisms that allow easy cleaning without disassembling the conveyor.
When it comes to maintenance, tubular cable and disc conveyors are relatively low-maintenance. The conveyor’s enclosed design helps to protect the internal components from dust and debris, which can prolong the life of the conveyor. Furthermore, the conveyor’s discs and cable can be easily replaced as needed.
Screw Conveyor Requires More Time and Energy to Clean
When it comes to maintenance and cleaning, screw conveyors can present some challenges. Unlike tubular cable and disc conveyors, screw conveyors are not equipped with special “clean-in-place” mechanisms, which inherently makes cleaning more difficult and labor-intensive.
One of the main issues with cleaning a screw conveyor is that not all the parts are fully accessible. The helix and other internal components are difficult to reach, which can make cleaning time-consuming. Additionally, food products and other delicate materials can leave residue and debris within the conveyor, which can be difficult to remove without causing damage to the conveyor.
When it comes to maintenance, screw conveyors can also be more challenging to maintain than tubular cable and disc conveyors. The open design of the screw conveyor trough can expose the internal components to dust and debris, which can shorten the life of the conveyor. Additionally, the helix and other internal components are subject to wear and tear, which can require more frequent replacement than a tubular cable and disc conveyor.
Advantages of Using a Tubular Cable and Disc Conveyor in Food Processing Facilities
The truth is that all conveyors have their pros and cons for specific use cases. Not every conveyor type will work for conveying frozen food (conveyor belt system, for example), just like not every conveyor type will work for conveying sand or packaged goods or glass bottles or electronic chips. Given all that we outlined above, there is no doubt that tubular drag cable conveyors are a part of advanced conveyor manufacturing and well-suited for transporting fragile materials in food processing facilities. Their biggest advantages include:
- Gentle conveying,
- Virtually no material damage,
- Enclosed system that is safe from contamination,
- Easy cleaning and maintenance,
- Low energy consumption,
- Low noise levels,
- Ability to fit into pretty much any floor space.
While screw conveyors are still used in some areas of food processing, perhaps it’s time to rethink their role and switch to manufacturing conveyor systems that lead to less material loss and higher product quality at the end of the day.
Enjoy Versatility and Precision in Tubular Conveyor Solutions
We highlighted how tubular cable and disc conveyors are a better choice when it comes to handling delicate materials in food processing facilities. These conveyors use a gentle material handling process thanks to the closed tubular design and discs attached to the cable, minimizing the risk of damage to fragile materials. Additionally, tubular conveyors can be tailored to suit the needs of the specific application, making them a versatile option.
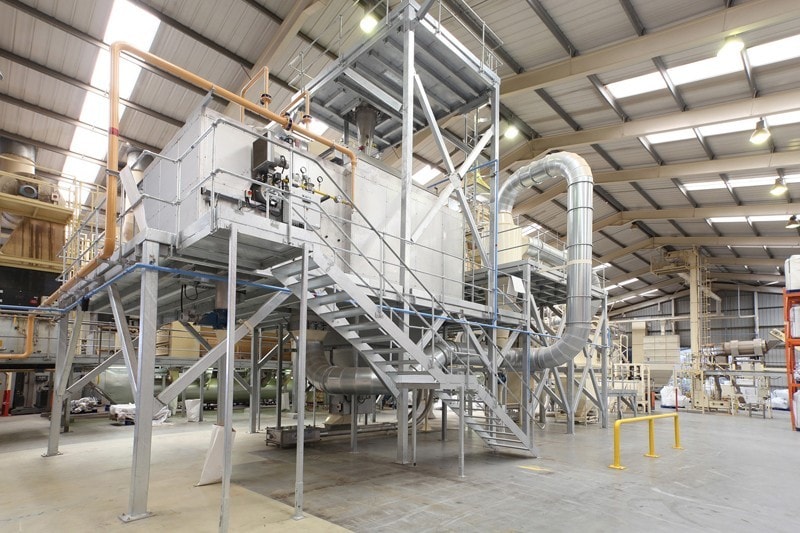
Trust Cablevey Conveyors – One of Top-Notch Conveyor Systems Manufacturers
Not only are tubular drag cable conveyors superior for handling delicate materials, but they also boast lower maintenance and cleaning requirements, resulting in reduced downtime and heightened productivity. These efficiency gains translate into substantial cost savings, minimizing the need for costly repairs or replacements. If you’re in the market for an automatic conveyor system for your food processing facility, seeking the expertise of Cablevey Conveyors extends beyond product knowledge. Our commitment includes comprehensive support, including conveyor installation supervision. Don’t hesitate to reach out – our dedicated team is more than happy to answer queries and guide you toward the optimal conveyor solution tailored to your unique needs.