In the world of grain handling, ensuring the careful transportation of delicate specialty grains is paramount to maintaining quality and preventing contamination. When faced with the myriad of conveyor solutions, the crucial question arises: “How to choose the best specialty grain conveyor?” Join us as we explore the key factors influencing this critical decision and shed light on why Cablevey Conveyors emerge as a top choice for gentle, efficient, and low-maintenance grain handling.
How to Choose the Best Specialty Grain Conveyor?
Selecting the ideal specialty grain conveyor involves considering factors such as material damage, conveying speed, and system type. Tubular drag cable conveyors, known for their gentle handling and low maintenance, stand out as a top choice. Cablevey conveyors, in particular, offer a reliable solution for protecting delicate grains during transportation, ensuring optimal product quality and minimal breakage.
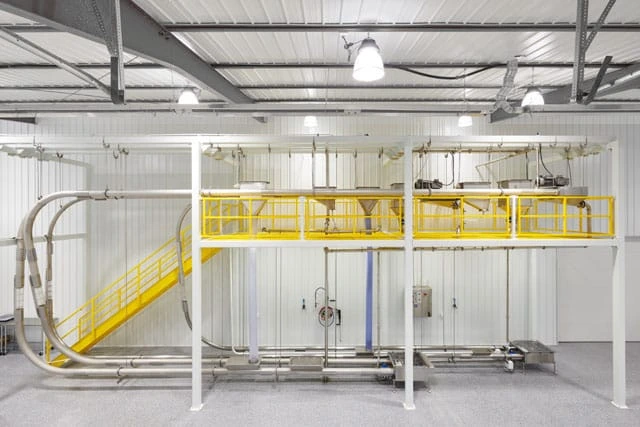
What Are Specialty Grains?
Specialty grains (rye, oats, millet, amaranth, etc.) are delicate and need to be handled with care, which means they require a special automated conveyor system. If not, then the grain will break easily and be susceptible to contamination from other substances. So, how do you know what kind of specialty grain conveying system to use?
There are several types of conveying systems, and all of them have their pros and cons. Of course, it all depends on how much space you have available in your facility and how many people work there. But it’s always best to find out all the information before making a final decision about choosing the best specialty grain conveyor.
What Is Grain Handling Equipment?
Grain handling equipment is another way of saying grain conveying systems. In the past, conveying was done manually, meaning that workers had to load the grain by hand using shovels and convey it through chutes. Fortunately, manual material transport is becoming obsolete.
Nowadays, automatic material handling equipment is being used to transport materials from one place to another. This ensures better health, safety, and environmental standards. On top of that, production processes are faster and more efficient. Any larger facility in practically any industry across the world can benefit from an automatic conveyor system. Whether it’s for transporting grains or any other material, there is a specialized type of conveyor that can handle the job.
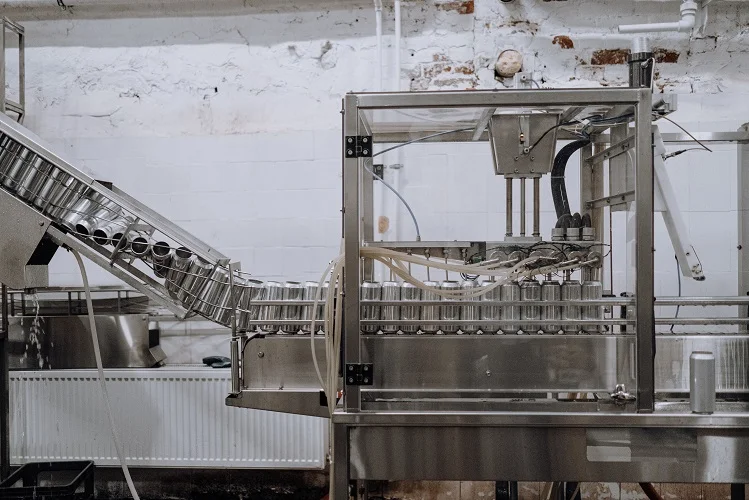
What Must Be Considered When Choosing a Grain Conveyor System and Why?
There are several important aspects to take into consideration when choosing manufacturing conveyor systems. Size, capacity, how much space is available, and how many people work in the facility are all critical factors. You should also consider the conveyor’s power consumption, how much maintenance it needs, and how reliable it is. For grain handling systems, the following aspects are crucial:
Material Damage
Fragile grains cannot handle vibrations and shocks as well as other materials. To avoid material damage, choose a conveyor engineering system that is smooth and consistent in how it conveys the material from point A to B. The grain should not be jostled too much or bumped into anything else along its way down the line. Otherwise, grains can break easily, leading to grain quality degradation and lower-quality products.
Conveying Speed
If the tubular conveying system moves too quickly, grains will suffer more breakage and not travel too far to reach their destination. If it moves too slowly, then your production lines will be delayed, and you might start losing profit.
When choosing how fast to move your grain, you should find a balance between how much damage it can handle without breaking and conveying at an appropriate speed, considering how long it takes for transportation to complete its route.
Open-Air or Enclosed Systems
Ideally, it would be best if you went for enclosed automated conveyor systems. This prevents contaminants from entering and spoiling your product. Cross-contamination is another big problem for delicate grains, and the only way to avoid it is by keeping them inside an enclosed system. Furthermore, dust represents a serious concern in a grain processing facility. Enclosed tubular conveyor systems ensure that the environment is dust-free and as clean as it can be.
Explore Some of the Best Conveyor Options
With numerous options available, choosing the most appropriate one could be quite overwhelming. From the steady performance of tubular drag cable conveyors to the classic reliability of belt conveyors, let’s check out the various industrial conveyor systems.
Tubular Drag Cable Conveyors
When taking into account everything we’ve mentioned above, we strongly recommend choosing tubular drag cable conveyors. They are enclosed systems that can handle a wide range of fragile materials and come in different capacities for how much weight they can carry. They also need less maintenance than the belt, screw, auger, and bucket elevators which is an important aspect to keep in mind.
In terms of how much space they require, drag cable conveyors are a good choice because they have a modular design. This means that they can easily be configured to fit your space constraints. In addition, tubular drag cable conveyors cause virtually no breakage or damage in general. They transport material in a steady, smooth motion that is appropriate for how fragile your product is, grain included.
The reason why they are so gentle on the material being moved is because of how their cables work. Instead of using rollers or belts to move along a track as other types of conveyors do, these systems rely on steel cables with fixed, solid circular discs that glide inside a tube. This prevents friction and material damage that would otherwise occur with other types of conveyors.
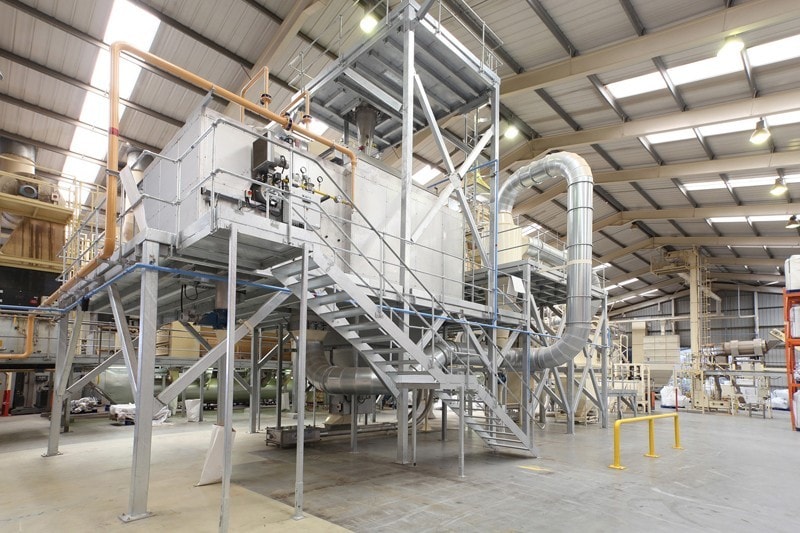
Bucket Elevators Are Great for Handling Larger Amounts of Materials
Bucket elevators may be a suitable choice for bulk grain conveying but are not ideal for specialty grains. They are good at moving large amounts of material but can easily damage materials like grain that need to be handled with care.
Bucket elevators can be open or enclosed, and they can move both horizontally and vertically. However, they require more maintenance than the other conveyor types on this list, which you must consider when deciding how much time and effort it will cost your business. While bucket elevators may be a suitable choice for other products, they are not the best option when you’re considering how to handle specialty grains.
Conveyor Belt Systems Are Traditional Solutions That Provide Efficiency
An industrial classic, a belt conveyor system can be a good choice for handling specialty grains. They can be enclosed systems that consistently transport materials without causing any damage or breakage along the way.
However, it is important to note that the conveyor belt system requires more space than most other grain conveyor systems. They can transport material only horizontally or at a slight angle, meaning that they can’t be used in tight spaces that require vertical conveying. They also need more maintenance than tubular drag cable conveyors, which is something to keep in mind when considering how much will be required for upkeep.
Pneumatic Conveyors Don’t Require High Repair and Cleaning Costs
Plenty of food processing facilities rely on pneumatic systems to convey specialty grains. Pneumatic conveyors are not a bad choice since they are enclosed, dust-free systems that do not require a lot of space for setting up. Furthermore, they are also low maintenance, meaning that your cleaning and repair costs will be kept to a minimum.
However, they rely on compressed air that moves the material along. This means that there needs to be an intense, high-speed airflow to transport materials properly. This extreme airflow isn’t gentle on specialty grains. Grain breakage and product damage and loss are common issues with a pneumatic system. Adjusting the airflow speed on this conveyor type is possible, but the energy costs of lowering the speed are likely to be high.
Screw or Auger Conveying Systems Come in Horizontal and Vertical Configurations
Auger conveyors work based on a helical screw that rotates within an enclosed tube. They can come in both horizontal and vertical configurations, but they require more space than most conveyors due to how the augers move inside the tubes. A significant benefit of these systems is their low maintenance cost. They don’t require a lot of cleaning and repairs to keep them running efficiently.
However, they also don’t offer the best value when it comes to how gentle on specialty grains they are. The biggest downside to screw conveyors is that the screw blade is quite damaging to the material. They are even known to compromise blends, causing the product to be unusable. Overall, augers are more suitable for material that doesn’t need to be handled with care.
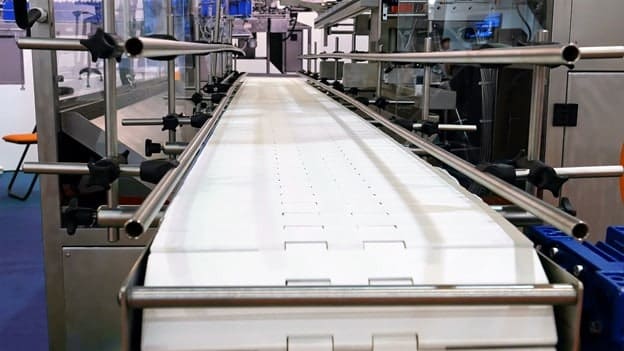
Elevating Specialty Grain Handling with Cablevey Conveyors
First and foremost, grain handling systems for specialty grain need to be gentle on the product. The best conveyors for this type of product minimize damage, contamination, and loss of material. Business owners should also consider how much time and resources will be required for maintenance upkeep, how much energy the system will need to keep running, how much space is needed for installation, and how labor-intensive it will be.If you’re wondering how to choose the best specialty grain conveying system, contact us today! Cablevey Conveyors is one of the top conveyor systems manufacturers that will help you select a system that protects your product and won’t cause damage or breakage along the way.