Conveyors have long been the backbone of the grain industry, providing an effective means for the transport of grains from one point to another and playing a pivotal role in the agricultural and processing industries. So, let’s explore the different types of grain conveyor systems, their features, benefits, and potential drawbacks.
Challenges and Considerations of Preserving Quality and Value in Post-Harvest Processing
When it comes to post-harvest processing, the focus is placed on preserving the quality and adding value to the grain by removing impurities and segregating lots (based on special characteristics of the grain). When it comes to such agricultural products, quality loss can occur due to poor drying techniques, substandard or improper bulk material handling equipment, as well as a lack of adequate storage equipment – from a conveyor belt for a warehouse to storing solutions that can result in various forms of deterioration. Among these, we can include cracking, sprouting, splitting, dry matter loss, insect damage, or mold growth.
The Importance of Suitable Grain Conveyor Systems
Large grains such as corn can be particularly susceptible to physical damage during handling, especially when dried at high temperatures. In turn, physical damage can also make the grain more susceptible to fungi and insect infestation. As such, all post-harvest operations aim to maintain the initial quality of harvested grain.
During storage, the grain needs to be protected from deterioration or mold, insects, and rodent attacks. During grain handling and drying operations, the material needs to be protected against any physical or chemical deterioration. Therefore, it’s critical to choose a grain conveyor belt system capable of minimizing deterioration and maintaining the desired level of quality.

What Is End-Use Quality?
End-use grain quality can take on different meanings, depending on the intended use of the grain. When it comes to hard wheat, for example, the ultimate criteria may be about loaf volume in baked bread. When it comes to soft wheat, the main objective may be cookie dough. Soybeans, on the other hand, may be processed for their protein and oil content.
Corn has a wide range of applications. If used in the ethanol industry, the amount of starch available is a critical factor for fermentation. Ethanol producers may also have other quality concerns because they could be selling coproducts like dried distillers grains (DDGs). These contain minimal or no mycotoxin.
Milling is also an important processing step for many grain products. Therefore, various milling characteristics are often important quality factors for rice, corn, hard, soft, or durum wheat. Some specialized end-users may focus on one grain quality parameter, such as a high oil content in soybeans or corn or amino acids when it comes to animal feed.
Traditionally, US grain grading standards were not focused on product quality characteristics that are of interest in today’s specialty grain markets. The early grain standards were created to facilitate trade and describe grain’s physical properties and storability. They were also used to characterize the product yield and overall grain quality. These initial grain standards were used to address any deterioration issues that negatively affected the product quality.
But over the years, with the development of rapid measurement technologies, these standards have evolved to also incorporate product quality characteristics. There are some standards that reference the specific product quality issues. For instance, the insect-damaged kernels (IDK), as they are described by the Federal Grain Inspection Service (FGIS), address potential milling problems of insect fragments found in the flour.
Quality measurement of a grain sample will assume that the sample will be representative of the quality of the entire sampled lot. Without a representative sample, any grade assigned to the material will be meaningless. As such, the FGIS recommends the use of continuous diverter type samplers to get the most representative samples.
The agency also requires the use of specific grain probes like a vacuum probe and a grain trier (gravity fill probe) that should be long enough to reach the container’s bottom. Also, the sample needs to be collected by using an approved probing pattern that includes nine different locations on shallow flat storage or flat-bottom trucks.
It’s important to keep in mind that grain quality never improves during storage. The best results are when it’s maintained to the initial quality as much as possible. Various grains can be kept in storage for prolonged periods of time if the storage equipment and overall conditions are properly managed. However, when degradation occurs, quick intervention is needed to minimize any product damage and market value loss.
The main reasons for the decline of grain quality are a result of the drying process, grain respiration, insect and rodent damage, mold and/or bacterial contamination, as well as during storage or handling. Proper grain moisture and temperature management are critical in reducing stored crop damage. High humidity and temperature levels will promote both insect infestation and mold development.
In general, the drier the storage environment, the higher the temperature will need to be before mold can begin to form. Every grain and seed variety will have its own safe storage moisture, temperature, and equilibrium relative humidity (ERH) criteria.
Grain overdrying can result in darkening, cracking, and seed damage. While drying damage is typically associated with corn, soybeans, rapeseed, canola, and other oilseeds can also be damaged during this process. Seeds will shatter during the handling process if they are dried to less than 6% moisture content. Drying can also result in non-visible damage. For example, overheated wheat may look normal on the surface but will contain denatured proteins that will affect the performance when making flour.
The primary causes of damage during storage are mold and insects. Grain kept in poor conditions will become a prime target for mold growth and insect population increase. In addition, damaged kernels will lead to pockets of fine material that impede the aeration distribution. This, in turn, allows insects to multiply, increasing both moisture and temperature in the process. Mold forms under high-temperature, high-moisture conditions. Cleaning the grain before storage, spreading the grain to reduce fine concentrations, and properly managing the aeration and storage equipment will help reduce mold and insect activity.
Last but not least, we need to address the mechanical handling, which can damage grain and seeds, reducing the overall quality and favoring other undesired conditions. Among these, we can include insect population growth and moisture hot spots due to poor aeration as a result of broken kernels. Damage can occur for several reasons, such as high-velocity impact, stress cracking during drying and cooling, or if the grain is very cold and very dry.
Choosing the right handling equipment, such as an auger system, horizontal drag conveyors or tubular drag conveyors, is essential in minimizing kernel damage. It’s important to keep in mind that the auger system needs to be operated at the rated capacity and speed for the specific grain handled. For example, slower and larger augers can help reduce handling damage to some degree.
The unloading process also needs to be given special attention. The grain can be unloaded from a bin directly into transport vehicles or another bin used for mixing with other products and/or ingredients. Handling equipment can differ significantly depending on the type of bin systems, facility layout, grain type, load-out, and conveyors.
Different Types of Grain Conveyor Systems and Other Grain Handling Equipment
Grain conveyor systems differ in terms of their use and configuration. However, they are all used to move material from one point to another. Selecting the type of belt conveyor system should, nevertheless, be based on reducing grain loss and damage during transfers from one facility to the next. Below are some of the most common material handling equipment used in moving grain.
Auger Systems
Portable or fixed augers move grain either horizontally or on an incline. An auger system can come in many sizes. Larger augers have greater capacity and move material quickly. However, that also means higher energy requirements. When compared to other conveyor systems, augers have somewhat low horsepower requirements. They are, nevertheless, simpler to operate and easier to maintain.
They are also more adaptable to different materials and conditions. It is important to note that a higher grain moisture level can decrease the amount of material an auger system will be able to convey. It will also increase the power required to do so. Augers are also used to move commodity grain and are not particularly suited for specialty grain.
Belt Conveyors
While belt conveyors have a higher capacity per horsepower than augers, they tend to be limited by the shallow angles of incline, steep costs, and extra floor space they require. By comparison to an auger system, belt conveyors are more gentle and will result in less grain damage. These types of systems are used in larger facilities or facilities that process products that cannot tolerate rough handling.
Nevertheless, even enclosed belt conveyors can still result in grain damage and will expose the product to contaminants. A usual industrial conveyor belt will also not maintain any preexistent ingredient mixes or recipes, such as those used in breweries, for different flours, in mixes for bread, oats, crackers, prepared meals, pet food, or snack foods.
Bulk Conveyors
Also known as mass flow grain handling equipment, these conveyors move bulk materials by scraping or pushing the material along a conveyor path. These bulk conveyor flights used to move the material are typically made from a low-friction plastic or composite material. These conveyors are generally used during on-farm operations and used in handling commercial grain. And while they use relatively less horsepower than augers or conveyor belts, they are less versatile, particularly when handling specialty and value-added grains.
Bucket Elevators
Bucket elevators use a vertical conveyor belt for food equipped with cups for scooping and elevating grain. Bucket elevators are also used in bulk material and grain storage facilities. Usually, the elevator legs are at the center of the entire operation, as most of the grain handled goes through them.
The grain leg consists of two metal vertical housings that enclose a belt. This belt supports closely spaced buckets bolted to it. The belt runs vertically between the top and bottom wheels on the legs. Grains will flow into the buckets at the base of the elevator leg and are lifted to the top, where it’s centrifugally discharged as the buckets rotate over a head drive wheel.
Bucket elevators can handle most types of wet and dry grain, processed materials, meals, and feed. This type of material handling equipment receives and delivers grain from most other conveyor systems in the facility.
Pneumatic Conveyors
Pneumatic conveyor systems are gaining a lot of popularity in commercial grain handling facilities. These systems are equipped with positive or negative pressure to manage air and materials. The pressure is used to discharge the material into trucks or grain bins for transfer to different storage containers. However, operators should make sure that there are no plugged airways in these conveyors.
However, great care needs to be taken in order to minimize grain impact damage. If at all possible, sharp turns should be avoided. Suction pressure conveyors need to have a vacuum and pressure gauge installed on the inlet and outlet of the rotary lobe blower. Filters also need to keep grain dust out of the blower. If not properly cleaned and maintained, the dust can quickly wear down the lobes and housing, which will increase the lobe tip clearance that can destroy the blower’s performance through excess bypass air leakage.
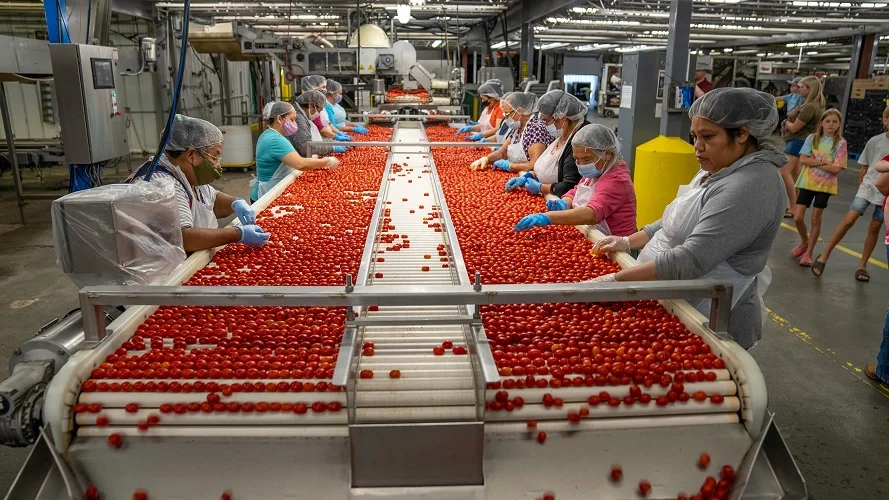
Using Tubular Cable Conveyors for Specialty Grain
While there are plenty of options to choose from when it comes to grain handling equipment, be it pneumatic, vacuum, grain elevators, enclosed belt conveyors, horizontal drag systems, and more, some are particularly well-suited for handling specialty grain. The handling system needs to move the grain in a gentle and dust-free environment. This is where tubular conveyors come into play. There are two types of tube grain handling systems – cable and chain conveyors.
Tubular Cable Conveyors
Tubular cable conveyors have emerged as a superior alternative to traditional chain conveyors, particularly for handling specialty grains and other delicate materials. Their versatile design and enclosed structure offer a multitude of benefits that contribute to their growing popularity in various food processing sectors. Here are some of the key advantages:
- Handling delicate materials: These conveyors can gently handle delicate bulk materials, powders, and mixes throughout the production, processing, and packaging phases. This is particularly valuable for specialty grains that may be more prone to damage.
- Versatility in use: They are versatile enough to move both wet and dry products, making them useful across different stages of the processing line. The food industry widely uses these systems for conveying a variety of products, including grains, powders, cereals, vegetables, snack foods, and more.
- Reduced contamination: The enclosed design of tube cable and disc conveyors helps to keep fines and chaff from escaping into the environment, reducing the risk of contamination.
- Improved product safety: At the same time, the enclosure protects the grain from external contaminants, ensuring that it remains safe and clean as it moves through the conveyor system.
In light of these advantages, it’s clear why many operations are choosing tubular cable conveyors as an integral part of their grain handling systems.
An Ideal Solution for Delicate Handling of Rice and Cooked Vegetables
Many processes will require a high degree of delicate handling. Parboiled rice and rice mixtures, when processed using conventional and fast-moving conveyor systems, can become degraded and separated if processed by the more common and rapid-moving conveyor systems, other than Cablevey’s rice conveyor systems. These can effectively move various types of rice at any point in the production process because their design prevents damage to materials. Parboiled rice, as well as rice combined with various herbs, spices, and other added ingredients, is more tender and fragile than commercial, uncooked rice.
As such, Cablevey Conveyors are far better suited for the handling of both white and brown rice, as well as any other rice blends, to avoid the breakage of the material and maintain the exact ratios of rice blends throughout the conveyor process. The same thing can also be said about cooked vegetables, which cannot be distressed to any significant extent on their way to the packaging process.
Securing Quality in Beer Brewing and Beyond
Another example is in beer brewing, a process in which barley needs to be protected while it’s being conveyed from the grinder to the mash tun. This principle also applies to beans, parent seed, frozen fruit, oilseed, and grain blends. All of these materials need to be handled with minimal to no breakage whatsoever.
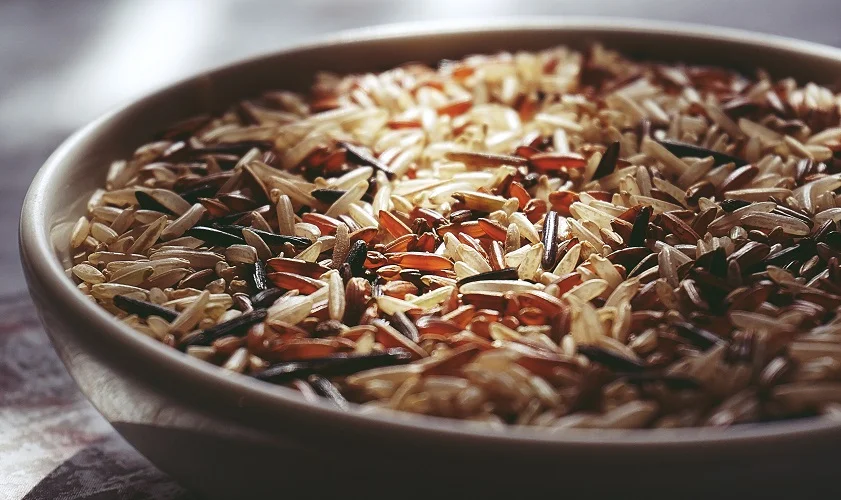
The Superiority of Cable and Tube Conveyor Systems in Maintaining Proportional Accuracy in Mixed Batches
It’s also important to know that for the food processing industry, it’s essential to maintain proportionate mix blends while they move through the food and grain conveyor system. But this can pose significant challenges, particularly for some material handling systems, such as horizontal drag conveyors, bucket elevators, pneumatic conveyors, augers, and more.
As the ingredients have variable granularities and densities, they can be faced with separation issues that may affect the overall proportional accuracy. Luckily, cable and tube conveyor systems have a definitive solution to this problem. Since the batch loads are contained between the discs and within an enclosed tube, the batch ingredients are moved all throughout the processing line and grain bins without the risk of damage, separation, or wastage.
You Can Tailor Cable and Tube Conveyors to Fit Your Needs
It’s also important to take into consideration the flexibility and high degree of customization that cable and tube conveyors feature. Since they are modularly designed, they can be used in a wide range of applications. Tube materials, diameters, and component parts come in a variety of sizes, depending on your needs. We also offer a full range of transfer systems, be it vertical or horizontal, feeders, different conveyor layouts such as loop, inline, horizontal corner, U-shape, or Horizontal-Vertical-Horizontal (HVH) layouts, and cleaning equipment, depending on your facility’s exact blueprint.
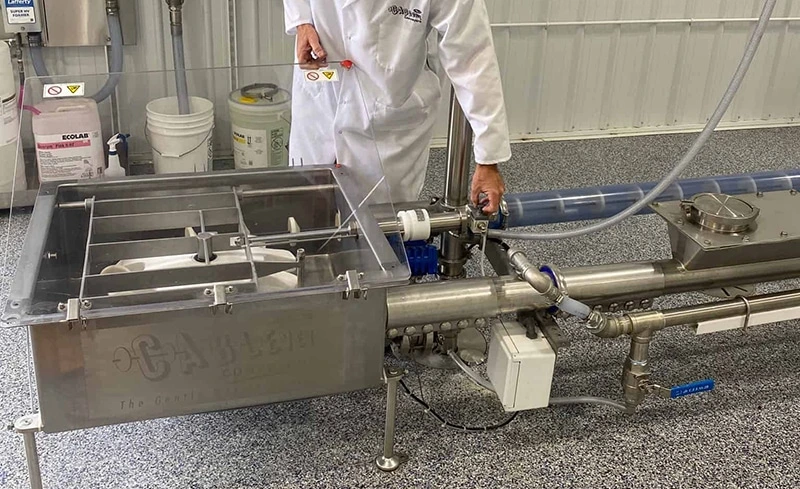
Cablevey’s Custom Solutions
Each of Cablevey’s specialty grain conveyor systems is a custom conveyor belt system. They are custom-designed by our engineering department to ensure they will be specifically optimized for your needs. Typical design considerations include how much bulk material can be moved without breakage, as well as how far, how high, or how fast you need your specialty grain to be moved from one processing center to another.
The existing configuration and available space within the processing environment will be taken into consideration to solve just about any grain conveyor movement needed. Add consistent hygiene, low horsepower requirements, and easy maintenance to these conveyors’ features, and you have everything you need to produce and process your specialty grains.
Ready to revolutionize your grain handling process? Explore our versatile, customizable, and efficient solutions at Cablevey Conveyors. Our expert team is just a call or click away, ready to guide you to the ideal conveyor system tailored to your needs. Let’s transform your operation together, minimizing wastage and maximizing productivity. Reach out to Cablevey Conveyors today!
FAQ
What Is a Grain Conveyor System?
The grain conveyor system is a mechanical system used in agriculture to transport grains from one point to another. It is a critical tool for enhancing productivity and efficiency in the grain industry.
What Are the Different Types of Grain Conveyor Systems?
Grain conveyor systems come in various types, including belt conveyors, pneumatic conveyors, drag conveyors, and tubular cable conveyors. Each has its unique features, benefits, and potential drawbacks.
Why Are Tubular Cable Conveyors Considered Superior for Handling Specialty Grains?
Tubular cable conveyors are gentle on delicate materials, versatile in moving both wet and dry products, reduce contamination risk with their enclosed design, and ensure product safety by shielding the grain from external contaminants.
What Factors Should Be Considered When Choosing a Grain Conveyor System?
When choosing a grain conveyor system, you should consider the longevity of the system, its capacity, maintenance requirements, safety features, cost, and the delicacy of the materials being handled.
What Is the Importance of Milling in the Grain Industry?
Milling is a crucial process in the grain industry. It greatly influences the quality factors of different grain products, such as rice, corn, and wheat. These quality factors may include oil content in soybeans or corn or amino acids in animal feed.