“What is a grain conveyor?” might be a question posed by those new to the field of agricultural and industrial processing. In essence, a grain conveyor is a specialized system used for the transportation of grain and other similar bulk materials.
These systems play a crucial role in a variety of agricultural and industrial settings, facilitating the efficient movement of materials from one location to another. Conveyor systems have evolved significantly over the years, adapting to the changing needs of different industries. This evolution has led to the development of various types of conveyor systems, each suited to specific tasks and operational requirements.
Historical Background of Conveyor Systems
Conveyor systems have had somewhat of an interesting journey throughout the history of industrial technology. Conveyor systems have existed for several centuries. In fact, farmers have been using various forms of conveyor belts to get grain into ships since the late 1700s. But unlike the highly technical and efficient tube and cable conveyor systems assembled by Cablevey, these early types of conveyor systems consisted of a wooden framework, cloth, leather, or rubber manufacturing conveyor systems and were operated by hand. They were also used primarily for bulk material handling, such as crops.
Evolution During the Industrial Revolution
As the Industrial Revolution kicked off in Great Britain during the 18th century and soon after moved to America, manual labor in various production environments began to be phased out in favor of the most innovative technology at the time: steam power. Less than a decade after the conveyor systems were invented, the first steam-powered conveyor systems were put into use by the British Navy. However, the first such automated system was not used in loading ships but in a bakery that produced biscuits for sailors. Regardless, this improvement meant that conveyor systems no longer needed to be operated manually, making them more effective and versatile in a wider range of applications.
20th-Century Advancements in Conveyor Technology
Machine-driven conveyors soon began appearing in all sorts of industries. By the early 1900s, factories began implementing industrial conveyor systems for bulk material handling. During the 1920s, engineers developed conveyors that could carry goods safely over ever longer distances, while rubber and cotton covers were also created and used around this time.
Several innovations during the 20th century brought automated conveyor systems closer to what we have today. While natural material resources, such as rubber, were needed for the war effort, conveyors began being made out of synthetic materials during World War II. Both the agricultural and industrial sectors entered the era of fast expansion and technological evolution in the post-war American economy that would also reflect on conveyor improvement.
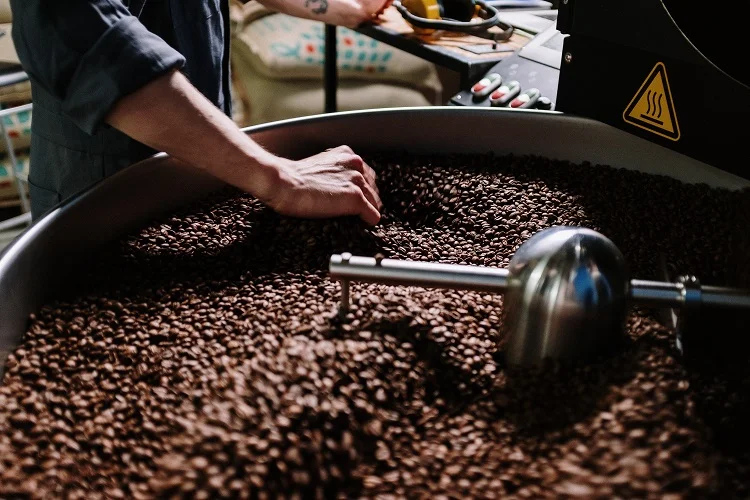
Modern Grain Conveyor Systems – Enhancements and Applications
During the last several decades, conveyor systems were constantly improved in order to run more efficiently, have low horsepower requirements, improve sanitation, have better dust control, and have fewer maintenance requirements. Many conveyor systems today are computer-controlled and automated, resulting in maximum performance and workload flexibility.
There are also many different kinds of grain conveyors in use today. Each of them has its own specific uses, depending on different variables such as the type of grain handled (commodity or specialty grain), the transportation distance, or the cubic weight or speed of conveyance of grain production and processing, among other considerations.
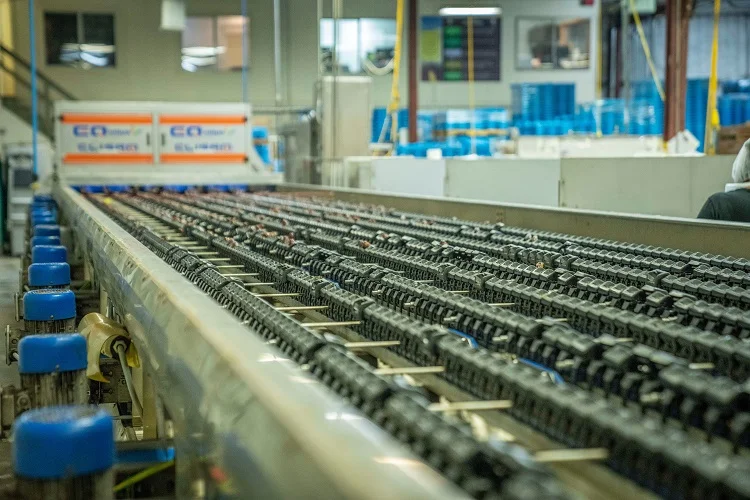
What Is A Grain Conveyor? Understanding Common Types of Grain Conveyor Systems
In the realm of agricultural and industrial processing, various types of grain conveyor systems have been developed to meet the diverse needs of grain handling and transportation. Each system offers unique features and advantages, tailored to specific applications and environments.
Below, we delve into some of the most commonly used grain conveyor systems, examining their designs, functionalities, and the specific contexts in which they excel. From the traditional bucket elevators to the advanced pneumatic conveyors, this section provides a comprehensive overview of these essential components in modern grain management and processing facilities.
Bucket Elevators
Bucket elevators are a type of vertical grain handling equipment, typically made out of galvanized steel and rubber belts. They have leg support towers that are usually at the center of the entire operation. The legs consist of a metal housing that encloses the belt, allowing the grain handled to pass through them. Spaced buckets are bolted directly into the belt, which runs vertically between two wheels located between the leg support towers. The grain flows into the buckets at the base of the elevator and is lifted to the top wheel, where it’s discharged by centrifugal forces as the buckets rotate around the conveyor belt.
Such grain handling equipment is typically used to move dry grain, animal feed, and various other processed materials. While it has somewhat low horsepower requirements, the bucket elevator design may result in unwanted fines and dust accumulation within the bucket coving or in product mixes or blends being compromised.
Chain Conveyors
Chain conveyors can handle horizontal grain handling and on an incline. The conveyor chain is made out of heat-treated metal and hardened with press-fit joints. Plastic pedals are mounted between two chains, which are used to move grain along its length. Inclined chain conveyors are used to transport grain to a higher level point. By combining both a horizontal and inclined chain conveyor, users can help reduce the cost of material handling equipment by not needing the use of a bucket elevator.
Auger Systems
Grain augers can be either portable grain handling systems or fixed and can move material both horizontally (sweep auger) or on an incline. Compared to a system like a tubular conveyor, augers are very limited in their ability to operate on different planes. Auger systems also come in different sizes and are almost exclusively used for the movement of commodity grain. While larger models have a greater capacity and can move the material faster, they are also more energy-intensive. Nevertheless, they have a somewhat low horsepower requirement as compared to other traditional conveyor systems and are easier to maintain and operate.
It’s important to keep in mind that a high moisture level of the product will tend to decrease the amount of grain moved by the system, as well as increase its power usage. Also, when moving materials in their “screw,” bigger and heavier materials in a blend will typically get pushed ahead while smaller materials fall behind. This denigrates the intended blend or mix. In addition, auger systems are unyielding in their screwing process. This means that materials will tend to get stuck between the screw and tube and get crushed in the process. This is not what is desired by anyone, but some accept the material loss because of the lower costs of the auger system.
Belt Conveyors
Belt conveyors tend to have lower energy needs than grain auger systems and will carry the material in a more gentle manner. However, belt conveyors are more limited in terms of the extra floor space they need, their high costs, and the shallow angles of incline. In addition, belt conveyors are also not perfectly suited to prevent exposure to external contaminants. Conveyor belts, like many other entries on this list, cannot maintain ingredient mixes or recipes such as those used in the production of flour used in making bread, crackers, snack foods, oats, various other prepared meals, or beer brewing.
Pneumatic Conveyors
Pneumatic conveyors are equipped with both positive and negative pressure conveyors. They are continuous conveyors used for bulk material handling. The grain is conveyed in an enclosed system by means of a vacuum or compressed air. Both types of systems work on the same principle. When the air velocity is fast enough, solid particles are picked up by the conveyor’s airflow and are moved along the pipe.
These types of conveyors feature more flexibility in terms of routing, and they have a simpler construction, require less space, and move the material in an enclosed environment. Their major disadvantages are that they have high energy costs, a high risk of becoming clogged, and can cause a lot of grain damage due to the high speeds at which the grain is handled if there is a bend, sweep, or discharge point. Wherever the straightaway ends, the material will tend to cluster rapidly and become damaged.
Cablevey’s Tubular Cable Conveyors for Specialty Grain
All of the conveyor systems we’ve talked about up until this point are, more or less, suited for handling commodity grain. However, because of their bulky sizes, high conveying speeds, and lack of flexibility, they are not particularly suited for handling specialty grains. So, instead of choosing grain handling equipment like bucket elevators, belt conveyors, horizontal drag systems, pneumatic or auger systems, it’s better to choose a tubular cable conveyor to handle all of your value-added grain processes.
Design and Versatility of Cablevey’s Systems
Unlike the other systems mentioned above, cable, disc, and tube conveyors were specifically designed to handle higher cost, higher value, value-added combinations of grains of different sizes, shapes, and strengths, powders, delicate bulk materials, specialty grains, and mixes all throughout the production and processing line. Tubular cable conveyors ensure that no foreign materials enter the enclosed environment and that nothing escapes it.
Applications in Sensitive Industries
It’s during these value-added grain processes that a high degree of delicate handling is required. Take the beer brewing industry, for instance. While it’s being conveyed from the grinder to the mash tun, the barley needs to be protected from grain damage and foreign contaminants. The same thing can also be said about oilseeds, parent seeds, grain blends, and more.
Parboiled rice and various other rice mixtures can also become degraded and separated during processing if they are handled by faster-moving conveyor systems. Cablevey’s Rice Conveyor Systems, on the other hand, can move all sorts of rice blends and mixtures while avoiding breakage and maintaining the exact blend ratios.
Maintaining Quality and Accuracy in Transportation
As the ingredients can have different densities and granularities, they can be separated during transportation from one station to another. When this happens, the proportional accuracy can quickly become compromised. Fortunately, tubular cable conveyors carry the batch loads in between discs pulled by cable inside of stainless-steel and (sometimes for certain materials) plastic tubing, where all ingredients are moved without any risk of separation, wastage, or damage. Cablevey conveyors are also designed in such a way that they can cater to a wide range of applications.
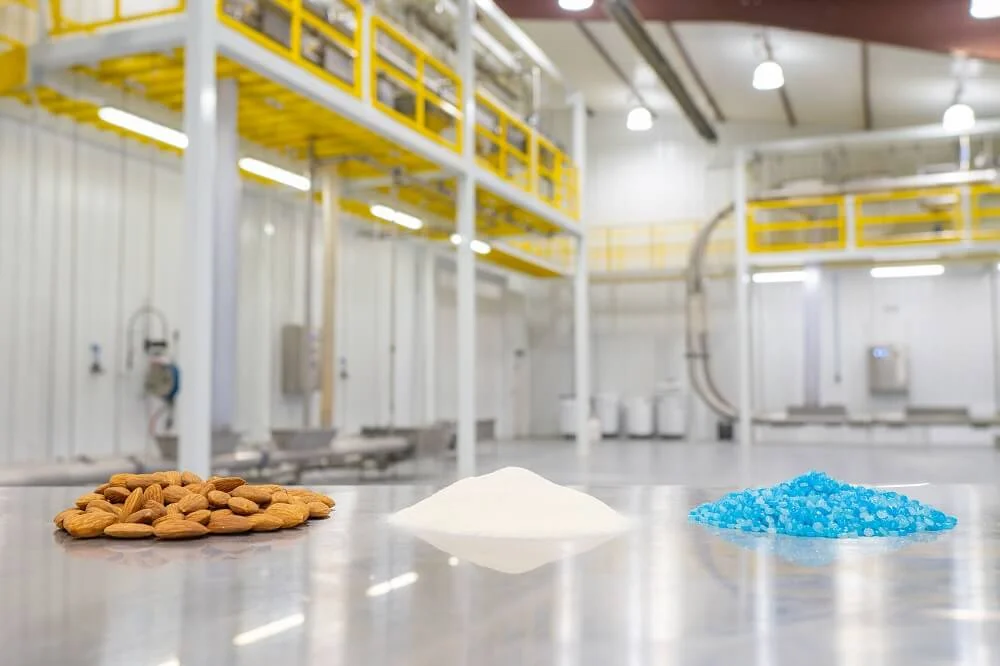
Conveyor Systems – From Manufacturing to Installation
The entire system, including tube diameters, materials, and component parts, can come in several sizes, depending on your unique requirements. They also include a full range of inlets, transfer systems, and cleaning equipment based on the facility’s layout. Thanks to the high hygienic standards, low horsepower requirements, and easy maintenance that these systems feature, Cablevey’s Tubular Cable Conveyors ensure complete handling of your specialty grains from start to finish.
Discover Cablevey’s Advanced Conveyor Solutions
In the realm of agricultural and industrial processing, various types of grain conveyor systems have been developed to meet the diverse needs of grain handling and transportation. Each system offers unique features and advantages tailored to specific applications and environments. We delved into some of the most commonly used grain conveyor systems, examining their designs, functionalities, and the specific contexts in which they excel.
To explore how Cablevey Conveyors can revolutionize your grain handling processes with our cutting-edge tubular conveying system, reach out for a consultation. Our expert team is ready to provide tailored solutions that meet your specific requirements, ensuring efficiency, safety, and the highest quality in grain transportation.