In numerous industries, maintaining the integrity and quality of the products or materials during the production process is crucial. This is particularly evident in the food processing sector, where products are delicate, and any damage can result in significant drawbacks. Fortunately, reducing material breakage with a tube conveyor system is possible. In our article, we’d like to delve into common causes that lead to material breakage. Learn how a tubular conveying system can eliminate or reduce this.
Bear in mind that, while it’s essential to maintain material integrity during transportation, a significant 29% of industrial establishments report that material damage ranks among their top three daily conveying obstacles.
Here’s Why Maintaining Material Integrity Is Crucial
Material breakage occurs when stress causes material particles to split into multiple fragments. Whenever a product or raw material rubs against an automated conveyor system’s surface, whether tubular, flat, or other, it can lead to abrasion of the product and potentially cause it to split.
Processes like grinding or intentionally mixing reduce products into finer particles to simplify their handling. These are beneficial steps in the production chain, designed to serve specific objectives. Outside these operations, breakage typically diminishes the product’s value. In the food processing industry, minimal breakage can result in product loss, sanitation problems, and reduced operational efficiency.
When Does Material Breakage Negatively Impact Production Operations?
Simply put, breakage leads to financial losses, be it through lost products, repair-related downtime, or low-quality products that require to be reprocessed or disposed of. Maintaining the quality of materials is especially crucial in certain situations, such as:
- When dealing with materials susceptible to deterioration, including brittle, delicate, or generally fragile products.
- When it’s crucial to maintain the uniformity of blends or mixes. This is essential for products like snack foods, morning cereals, tea mixtures, and other items demanding a balanced mix of ingredients.
- When the generation of product dust is an issue, certain substances produce more dust upon breaking. This could pose respiratory risks for employees, cause equipment issues, and other dust-related dangers, such as potential dust explosions.
Every production company’s primary objective, especially when handling unique materials or specific blends, should be to minimize or completely avoid product breakage. However, to achieve this, we first need to identify the root causes of this issue.
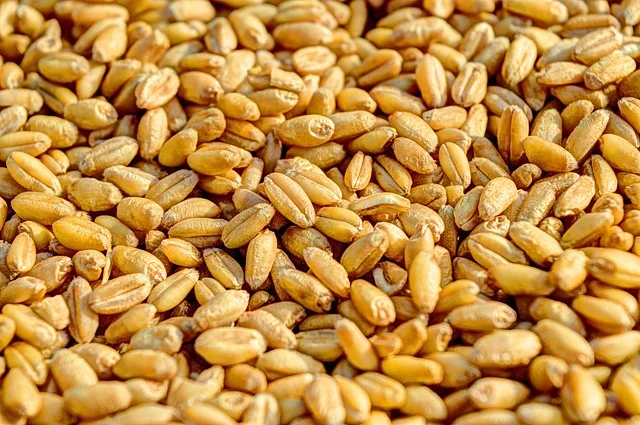
Why Do Materials Break?
The predominant cause of this problem during conveyance is impact. This impact primarily manifests in two ways: free-fall impact, where material drops from a height, and collision impact, where material forcefully comes into contact with another object or surface. These issues typically occur with some less advanced conveyor belt systems.
Free-Fall Impact
When delicate items fall or are thrown from a height, there’s a high chance of them breaking. Such free-fall impacts often happen during transitions between conveyors or when materials are loaded onto or unloaded from them.
Such breakage is often observed in automated conveyor systems like bucket elevators and other conveyors that rely on gravity. When the product is raised and subsequently transferred into the chute or channel, its fall and the subsequent impact on the surface underneath can lead to damage.
Collision Impact
Collision impact occurs when two transported material pieces come into contact, like when two particles strike each other while in motion. It can also happen when a particle hits a fixed part, such as the side of an automatic conveyor system, its belt, a tube, or other conveyor parts.
This kind of material breakage is frequently observed in systems like screw conveyors and pneumatic conveyors. As particles travel through these systems, particularly in pneumatic conveyors, their high speeds can lead to breakage upon collision with an obstacle.
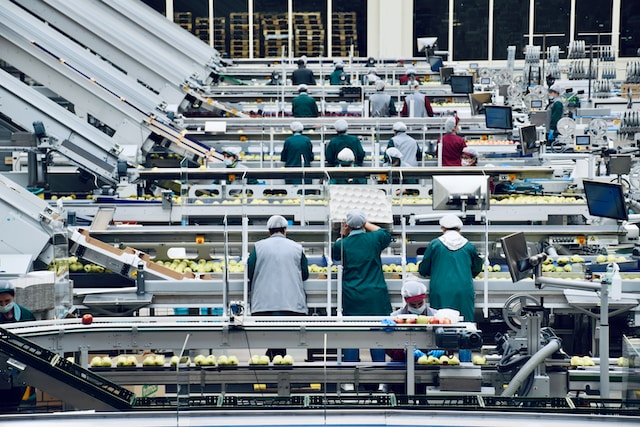
Other Causes of Breakage
Apart from collision impact and free-fall impact, different causes impact production less frequently, but that should be known as well. These include:
- Excessive vibration,
- Chemical erosion,
- High temperatures,
- Moisture damage,
- Electrostatic discharge.
Although various factors might lead to material breakage, the most prevalent reason is collision impact. However, it’s vital to know that conveyor systems manufacturers have come up with needed conveyor solutions that would reduce this issue.
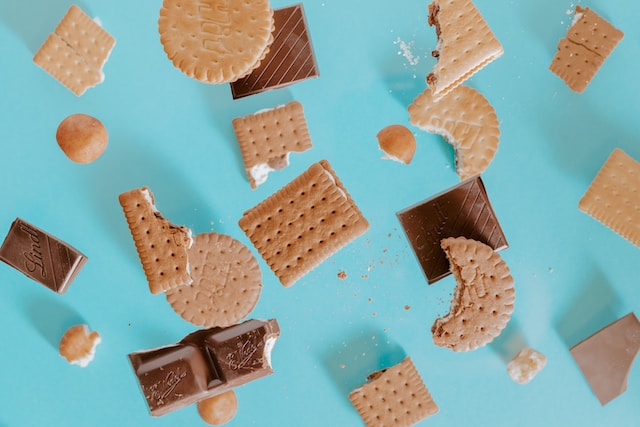
Is There a Way to Prevent Material Breakage? Yes, and Here’s How
Follow our tips to minimize breakage and keep your materials intact. The way to prevent this issue from jeopardizing production is by doing the following:
- Instead of screw feeders and rotary airlocks, use vibratory feeders – Vibratory feeders reduce breakage at the entry point, eliminating the need for the rotating shaft found in screw feeders or the blades present in rotary airlocks.
- Easy speed change – Alterations in the speed of an industrial conveyor system can lead to abrupt impacts, potentially breaking the product. It’s advisable to implement speed adjustments, whether increasing or decreasing, in a gradual manner to prevent such issues.
- Use gentle curves – Curves in an automated conveyor system might cause materials to decelerate and have increased interaction with the underlying surface, raising the risk of breakage. It’s best to steer clear of abrupt bends or opt for surfaces made of materials with minimal friction to lessen contact.
- Monitor humidity and temperature – Ensure that your environmental conditions in the facility adhere to the suggested parameters to help reduce material degradation.
Reducing Material Breakage With a Tube Conveyor System
A straightforward yet frequently neglected strategy to decrease or prevent material breakage is to employ a soft conveying system. Such a system emphasizes slow, high-volume movement, ensuring materials progress along the conveyor with minimal contact points, minimizing impacts and breakages. This is the advantage of tubular conveyors.
How Does a Tubular Conveying System Function?
A tubular conveyor is a closed system that uses a cylindrical loop to transport material within a facility. The substance is introduced into an initial tube, and as it progresses, it transitions smoothly to subsequent tubes. This cycle persists until the product arrives at the conveyor’s endpoint.
The material’s movement is facilitated by round, solid discs uniformly distributed on a cable that spans the tube’s length. These discs discreetly propel the material forward. They are linked to a gearbox, which in turn is attached to a motor. The motor’s velocity dictates the pace of the discs and, consequently, the rate at which the product moves.
Given the steady movement and absence of sudden shifts in direction or velocity, coupled with the continuous propulsion by the discs, the likelihood of the material breaking is very low.
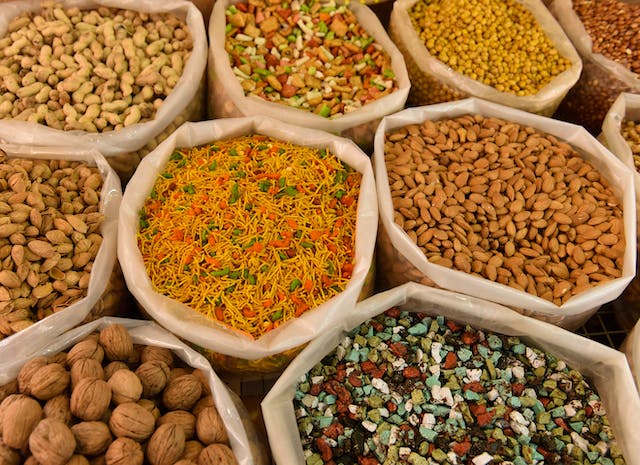
Additional Benefits of a Tubular Conveyor Prevent Material Degradation Efficiently
These conveyors can be configured to function at reduced velocities, decreasing the potential for the material to encounter intense vibrations or elevated temperatures. Additionally, given the conveyor’s stainless steel composition, there’s no threat of chemical corrosion or electrostatic releases.
Given the sealed design of the tubular conveyor, it’s simpler to regulate environmental factors like temperature and humidity, further reducing the chances of material deterioration.
Furthermore, they are easily customizable to customer’s specific needs (particularly Cablevey’s conveyor with a cable and disc). This implies that you can design them to transport materials in a manner that limits touchpoints and diminishes the likelihood of collision-related impacts.
Chain Disc vs. Tubular Cable Systems
If you’re considering tubular drag conveyors to mitigate material breakage, you might be deliberating between a tubular cable or a chain disc mechanism. When it comes to maintaining product quality, cable disc systems hold a slight advantage over tubular chain setups.
Materials are less prone to getting caught on the nylon-coated cable and discs, resulting in reduced breakage. On the other hand, the open chain links in a chain might capture materials, leading to tearing, fracturing, and buildup.
On top of this, cable and disc conveyors are notably more hygienic and straightforward to clean compared to chain and disc conveyors. The cable and disc systems lack the small crevices where bacteria or contaminants might settle, unlike the chain and disc systems. What is more, when considering maintenance, cable and disc tubular conveyors prove to be a superior choice.
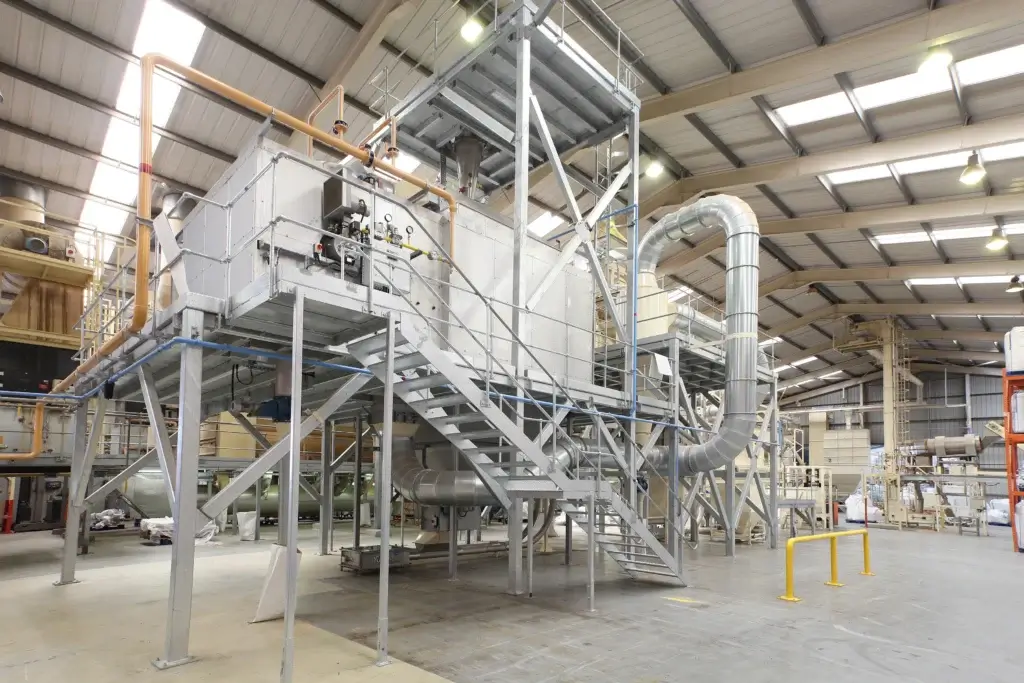
Invest in a Conveying System That Preserves Material’s Integrity
Preserving your material’s quality is crucial for the end product’s quality. In the realm of food processing, this involves avoiding material damage. While there are various methods to achieve this, utilizing a tubular material handling system stands out as one of the best methods.
Employing gentle conveying techniques with slow, high-volume movement allows for fewer contact instances, reducing potential breakage risks. Thanks to the build and design of a tubular conveyor – from the choice of materials to its architectural approach – you can also limit the degradation of materials, ensuring the highest quality of your product.
For tubular conveyors and conveyor installation supervision, contact Cablevey Conveyors right away. Our team of engineers can work on a custom system that will meet all of your needs.