Are you looking for conveyors that minimize material loss, degradation, and breakage? Which conveyors are the best for fragile materials, and which can be configured to work in a variety of environments? In this blog post, we will explore these questions and more. We’ll also look at how conveying systems impact process efficiency and throughput when it comes to fragile materials like coffee beans, breakfast cereal, nuts, and more.
Main Causes of Material Damage During Food Processing
Fragile materials are prone to damage, such as crushing, material breakage, and pulverization. It is important to choose a conveying system that will minimize damages as much as possible while also maximizing the output rate of your process line. To better explain the ideal conveyor system for fragile materials, we first need to take a closer look at the two primary causes of material damage during conveying: freefall and relative motion.
Freefall, or, more specifically, the landing after a free fall, typically occurs when the product is transferred between conveyors and when the material is fed into the conveyor or discharged from it. Relative motion refers to the relative motion between particles and between particles and a stationary conveyor component. This can be observed in vertical bucket elevators where materials are scooped out from a boot by the buckets.
To preserve product integrity, it is crucial to minimize the effects of free fall and relative motion during material transport. There are several conveyor types that would be suitable for this, and we’ll talk about them in the next section of this article.
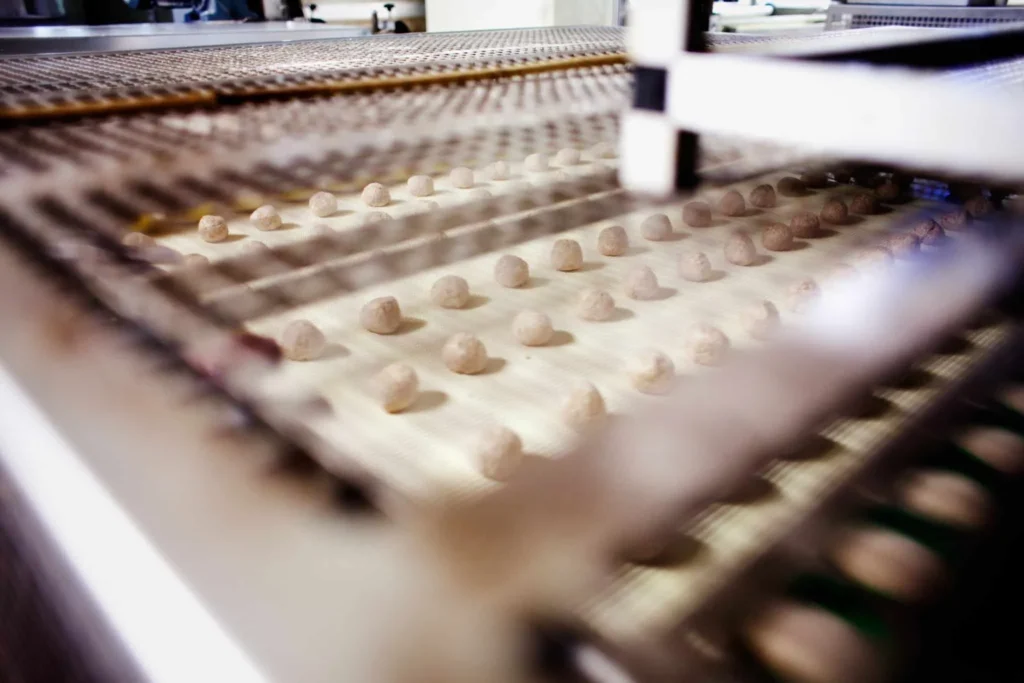
Tubular Drag Cable Conveyors
For fragile materials in the food processing industry, tubular drag cable conveyors are hands down the best choice, especially for transporting nuts (pecans, almonds, walnuts, peanuts, pistachios), coffee (ground coffee, roasted coffee beans, green coffee beans), tea, dried peas, dried beans, seeds, rice, grains, frozen food, and breakfast cereals.
The main principle of tubular cable systems lies in an enclosed tube with a coated stainless steel cable running through it. This cable pulls evenly spaced discs inside the tube, which gently pushes the material forward. With tubular cable conveyors, there are no rollers or drums. The inner tube prevents abrasion and damage to the material. The benefits of tubular drag cable conveyors include:
- The system is extra gentle on delicate products,
- There won’t be any food contamination or dust,
- There is no noise pollution,
- The system efficiently transports material from one end to the other,
- Low maintenance and cleaning costs are guaranteed,
- You can expect low energy expenditure,
- The machine has a modular design (it can fit any floor plan and layout),
- Systems can be customized for specific needs.
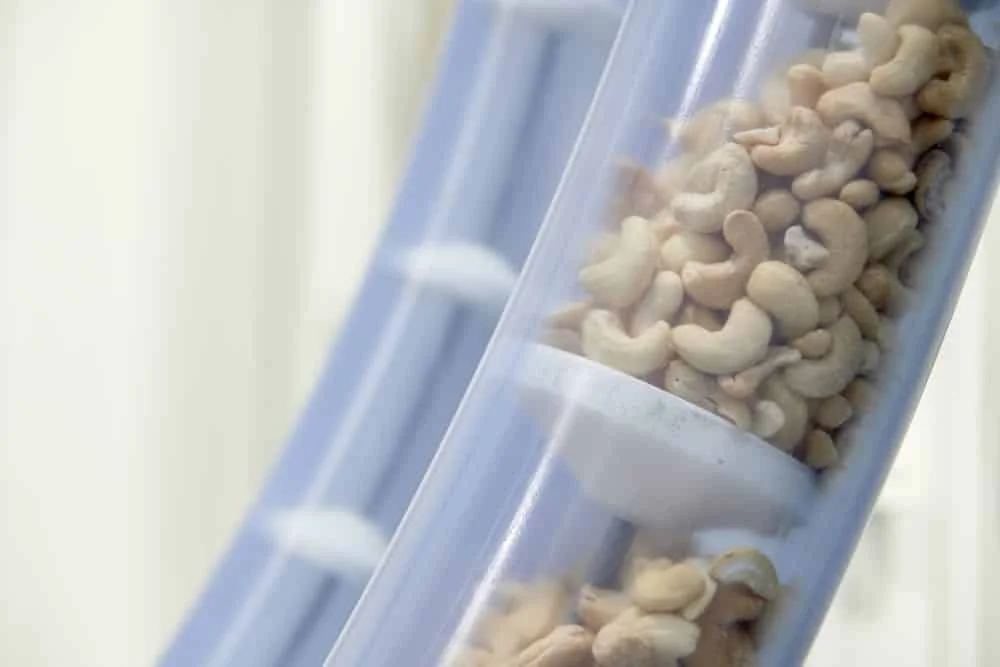
Wrap Conveyor System
A wrap/tube conveyor starts as an open belt conveyor system and then “wraps” itself into a tube, enclosing the product as it travels between the inlet and outlet. This conveyor type can accommodate multiple inlets and outlets, as well as different inclines or even curvatures. It is relatively easy to clean and an incredibly gentle commercial solution for transporting fragile materials. Wrap conveying is an excellent choice for the following products:
- Candy,
- Vegetables,
- Meat,
- Fish and shellfish,
- Animal and pet food,
- Fish food,
- Coffee,
- Rice,
- Nuts,
- Peas,
- Corn.
Of course, there are many more products that can be transported via this conveyor system. Still, when it comes to the quality of bulk material handling equipment, this system also has its downsides. The downside of wrapping conveyors is a reduced transport capacity per unit length of belt compared to an open custom conveyor belt for the warehouse.
Vibratory Conveyor System
Vibratory or vibrating conveyors function based on vibrational energy that causes materials to move up or down a pathway. The conveying surface is usually a trough with vibratory components attached to it, making it shake lengthwise. These vibrations cause the material to “hop” with the same frequency as the vibrations towards one end of the smooth trough. These conveying systems can operate at high temperatures and lead to very low material degradation.
Even though the relative motion in these conveyors can be high, they don’t significantly impact material integrity. Because of their vibrating feature, they are better suited for larger particles than fine powders, such as ground coffee. Cohesive materials might stick to the conveyor and could be discharged in the form of agglomerated lumps. Other downsides to vibratory conveyors are that they can operate only over short distances and are not suitable for high inclines.
Belt Conveyor System
An industrial conveyor belt for food is not a bad option for moving fragile materials. The conveyed product or material remains stationary on the belt during transport, drastically reducing any chance of damage. This kind of system can be installed in any space with enough available floor area.
When it comes to belt conveyors, there are two types: open type and closed type. Which one you use depends on what material will travel along the belt – if fragile materials are your key focus, then the closed type is your best bet. It’s important to note that belt conveyors have a limited conveying angle, though this can be increased with a textured belt.
Open belt types have no means of protecting the moving material from outside contamination, preventing material loss due to windage, or preventing dust from spreading inside the facility. Closed belt systems, on the other hand, are not that easy to clean. If they are not properly maintained, you could face potential contamination issues inside the enclosure.
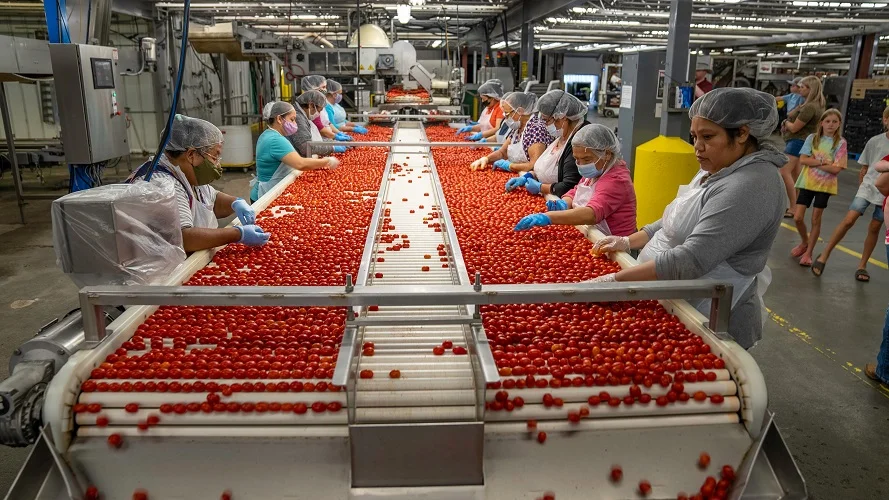
How to Choose the Right Conveyor System for Fragile Materials?
Weighing the pros and cons of each conveyor system is a good place to start your selection process. However, you should consider more than just the drawbacks and benefits of a conveyor system. Which machine is most appropriate for your needs? Which material will you be conveying, which production process are you using, and what weight capacity do you need to meet demand? The answer may not always seem clear at first glance, but with some research and evaluation, the right conveyor for your application can be found.
Consider the Characteristics of the Material
The choice of the best conveyor system for fragile materials isn’t always the same – it can vary depending on the type of material that you’re processing. When choosing a new conveyor, it’s important to pay attention to the characteristics of the material in question – here’s what to keep in mind when deciding:
- Moisture content,
- Bulk density,
- Particle shape,
- Sensitivity to humidity and temperature,
- Drop testing data,
- Units or volume to be conveyed,
- Particle distribution data,
- Optimal temperature of the operating environment.
Have a Test Run to Determine the Suitability of a Conveyor System
Ideally, the conveyor manufacturer will enable a test run of the material on the conveyor before purchasing. This is the best way to determine if the system in question fits your needs. During the test run, make sure you observe all of the following:
- The distribution of particles along the conveyor’s length and width ensures uniformity.
- If your material is sensitive to humidity or temperature, make sure that these conditions are measured as well.
- Make note if any segregation occurs in relation to particle size.
- Check for any undesirable properties, such as static charges or corrosiveness that may show up during the test.
When a material is fragile, it may not survive being dropped from higher heights or while traveling through choppy air currents in conveying systems. For delicate products such as cereal and coffee beans, drop testing data (a controlled fall) can help confirm that your product will make the trip without breaking.
Another consideration is the product’s bulk density and its flowability (or lack thereof). If you need to pack a lot of cereal into a small volume, your material may not be ideal for conveying systems that require compacted loading or high throughput rates. The same goes if it does not readily stick together in clumps during transportation.
Don’t Overlook Application Requirements
First, think of the budget. While going over your budget is not a good idea, it is also not advisable to go for a cheaper option solely because of its price. Don’t overlook the power requirements. The power bill for your conveying system is a significant portion of the total cost. If space in your facility is limited or ceilings are low, tubular drag conveyors could make more sense than any other conveyor type.
Conveyor layout and routing are things to think about, and so are the ease of cleaning and sanitary requirements. You want to be able to clean your system as easily and quickly as possible. Consider the desired conveying rate and check to see if it will be sustainable, given the power requirements and floor size. Of course, safety is a vital consideration as well – you don’t want a conveyor system causing injury to your employees or damaging other equipment.
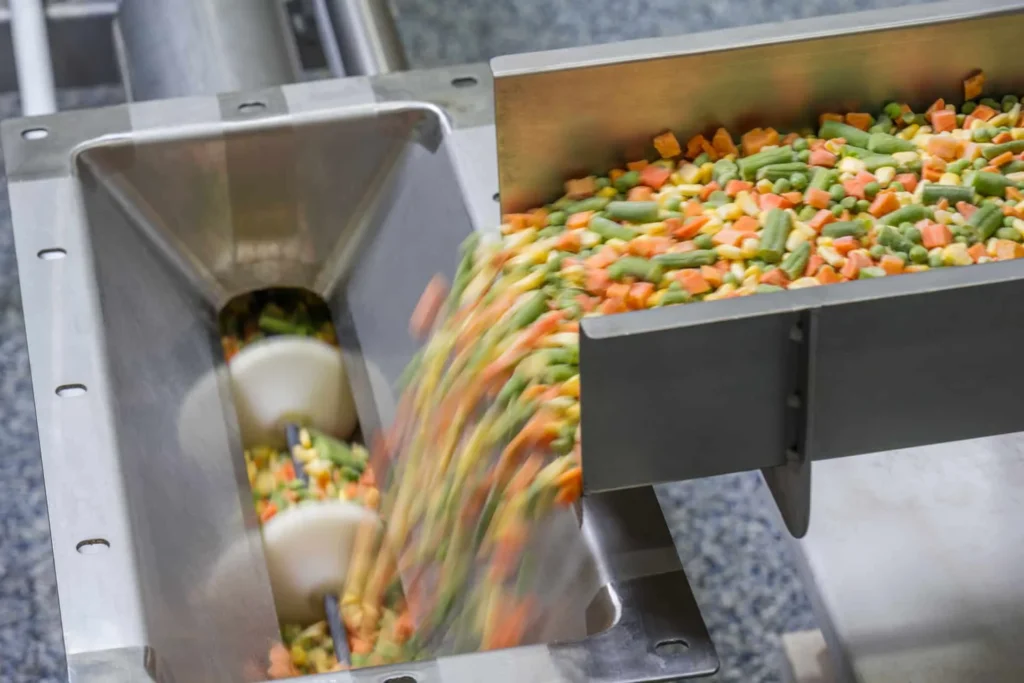
Deciding Which Conveyors Are the Best for Fragile Materials
So, let’s recap what we’ve talked about. When it comes to fragile products and materials in the food processing industry, there are four primary types of conveyors you should consider: tubular drag conveyors, vibratory conveyors, wrap conveyors, and belt conveyors. Each one of these types has its pros and cons, depending on your specific needs.
Before you make the final decision on the new system for your facilities, take a moment to consider the material and business requirements, such as material type, particle shape and size, moisture content, bulk density, as well as site constraints, budget, and power requirements, and more.
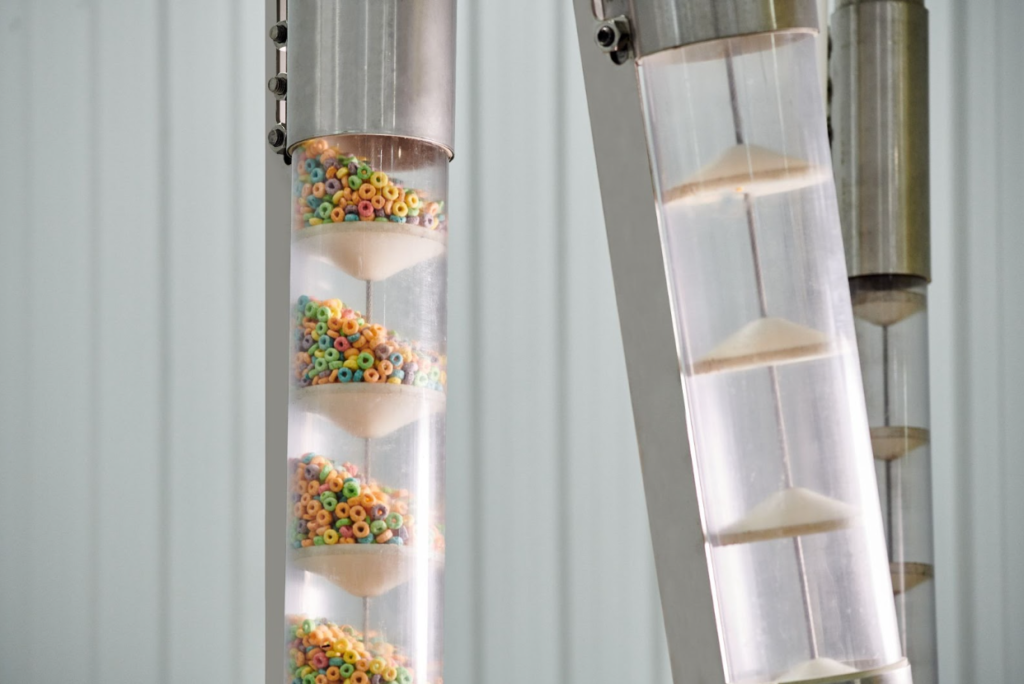
Contact Cablevey Conveyors and Improve Your Production Process With Our Top-Quality Conveyor Systems
If you are looking for a system that is gentle on the products and minimizes production loss or degradation of fragile materials like breakfast cereal, coffee beans, and nuts, check out Cablevey’s tubular drag conveyors. Contact us for more information on tubular drag conveyors and how they can help expand your business – Cablevey Conveyors is here to help!
FAQ
What Are the Main Causes of Material Damage During Food Processing?
Fragile materials, especially in the food industry, often face damage due to two primary reasons: freefall and relative motion. Freefall typically arises during transitions between conveyors or when material is introduced into or ejected from a conveyor. Meanwhile, relative motion can be due to the movement between particles or between particles and a stationary part of the conveyor, often leading to abrasion or crushing.
Why Are Tubular Drag Cable Conveyors Considered the Best for Fragile Materials?
Tubular drag cable conveyors offer a unique mechanism where materials are gently ushered through an enclosed tube, preventing exposure to external factors. These conveyors not only shield against abrasion and potential damage but also ensure minimal contamination and dust. The systems are notably quiet, minimizing noise pollution, are energy efficient, and can be tailored to fit various production needs.
How Does a Wrap Conveyor System Work?
The wrap conveyor system starts its operation as an open belt conveyor. As it progresses, it “wraps” itself into a tube, thereby enclosing the material and safeguarding it during transit. Suitable for products from candy to grains, this conveyor offers multiple entry and exit points. While its capabilities are vast, it’s essential to note that its transport capacity per unit length might be slightly lower compared to other conveyors.
What Are the Characteristics of a Vibratory Conveyor System?
Vibratory conveyors operate using vibrational energy, creating a motion pathway for the materials. These conveyors are designed to handle high temperatures and are recognized for minimal material degradation. They are optimal for larger particles, though their vibrational nature makes them less suitable for powders or materials prone to agglomeration. Their length and incline capabilities are also more limited than some alternatives.
How Does a Belt Conveyor System Differ in Its Open and Closed Types?
An open belt conveyor system is straightforward, with no protection against external factors. In contrast, the closed type encompasses the moving material, offering a layer of protection. However, while closed systems keep contaminants out, they might be more challenging to clean. Proper maintenance is vital to prevent potential risks of internal contamination.
What Factors Should I Consider When Choosing a Conveyor System for Fragile Materials?
Beyond the fundamental pros and cons of each conveyor type, it’s essential to delve into the material’s specifics: its moisture content, bulk density, particle shape, and sensitivities. Conducting a comprehensive test run can offer insights. Moreover, practical considerations like power consumption, spatial constraints, budget, safety protocols, and ease of maintenance should be assessed thoroughly.
Which Conveyor Systems Are Most Recommended for the Food Processing Industry?
For food processing, especially when dealing with fragile materials, four conveyor types often stand out: tubular drag conveyors, vibratory conveyors, wrap conveyors, and belt conveyors. Each offers its set of advantages tailored to different needs and material types. A thorough evaluation of material properties, coupled with business requirements, will guide the ideal choice.