As a manufacturer, you are probably wondering what are tubular cable conveyors and how they can enhance your processing of food and materials. Tubular cable conveyors are a type of mechanical conveyor that uses a continuous cable and disc system to move materials through a round, enclosed tube. They are increasingly used in the food processing industry (we commissioned over 32k conveyors in 66 countries around the world!), as they are efficient and reliable material handling solutions.
With their space-saving design, gentle conveying capabilities, low maintenance requirements, and flexibility, tubular cable conveyors are perfect for handling delicate materials.
What Are Tubular Cable Conveyors?
A tubular cable and disc conveyor is a type of mechanical conveyor that utilizes a unique design to move materials through an enclosed tube in a continuous loop. The belt conveyor system is made up of several key components, including:
- An enclosed tube,
- A stainless steel cable coated in nylon,
- Solid circular discs that are evenly spaced along the cable.
The enclosed tube is the main structure of the conveyor and serves to protect the conveyed material from outside contamination, such as dust and debris. The tube is typically made of durable and corrosion-resistant material, such as stainless steel, which allows for a long lifespan.
Our Clearvey System Is Revolutionary
Another option for tube material is our patented Clearvey system which allows for easy transport of fragile materials that contain oils, such as nuts. It is essentially a form of plastic (durable and flexible), but one that doesn’t release particles into the conveyed material or cause any alterations in the food product. The stainless steel cable in the conveyor tube, coated in nylon, is the driving force of the conveyor. It is responsible for moving the discs and in turn, the material being conveyed. The cable is strong and durable, able to withstand the weight of the materials being conveyed.
The solid circular discs are attached to the cable at regular intervals and are responsible for carrying the material through the tube. The discs are typically made of a durable and wear-resistant material such as polyurethane or high-density polyethylene. A drive unit is also a part of the conveyor. It is typically located at one end of the conveyor and can be powered by an electric motor or other power sources.
Additional Features
Additionally, clean-in-place (CIP) mechanisms are often incorporated into the design of tubular cable and disc conveyors to facilitate easy cleaning and sanitizing of the conveyor, which is important in the food processing industry. Other components of a tubular drag cable conveyor can include a pneumatic tensioning device, which is used to adjust the tension on the cable, ensuring smooth operation, and a control panel to control and monitor the conveyor’s operation.
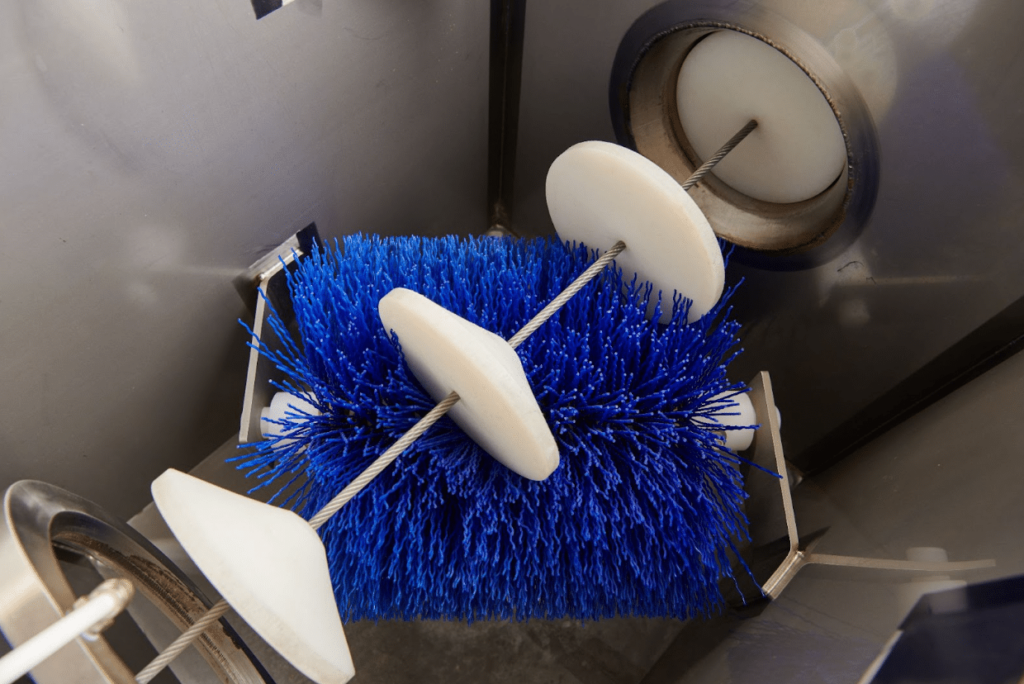
How Tubular Cable Conveyors Work
Tubular cable conveyors work by utilizing the design of their components to move materials through an enclosed tube. The basics are pretty straightforward – the drive unit provides the power to move the cable inside the tube, which in turn moves the discs. Food material fits in the space between two discs and is then gently pushed along through the tube. You can see just how tubular drag cable systems work in our videos here.
One of the main advantages of tubular cable conveyors is their flexibility in terms of material handling and conveyor path. Because of the enclosed flexible tube design, the conveyor can move material in any direction, including horizontally, vertically, and at an incline. This allows for a conveyor system that can navigate tight spaces or multiple levels, making it an ideal choice for food processing facilities where space is often limited.
What About Their Size and Capacity?
The size and capacity of the tubular cable conveyors can also be tailored to fit the specific needs of the food processing facility. The tubes can be of varying sizes, allowing for different capacities and throughputs. Here are the tube diameters and conveyor capacities that Cablevey offers for its tubular cable and disc conveyors:
- 2” tubes – convey up to 3,000 lbs per hour,
- 4” tubes – convey up to 21,000 lbs per hour,
- 6” tubes – convey up to 49,420 lbs per hour,
- 8” tubes – convey up to 80,000 lbs per hour.
Are There Different Types of Tubular Cable and Disc Conveyors?
In short – no, there is only one type of tubular cable conveyor. However, tubular cable and disc conveyors represent a subset of tubular drag conveyors. It is important to note that they should not be confused with tubular drag chain conveyors. Tubular cable and disc conveyors utilize a continuous cable and disc system to move materials through an enclosed tube, while tubular drag chain conveyors use a chain and disc system to move materials through an enclosed tube.
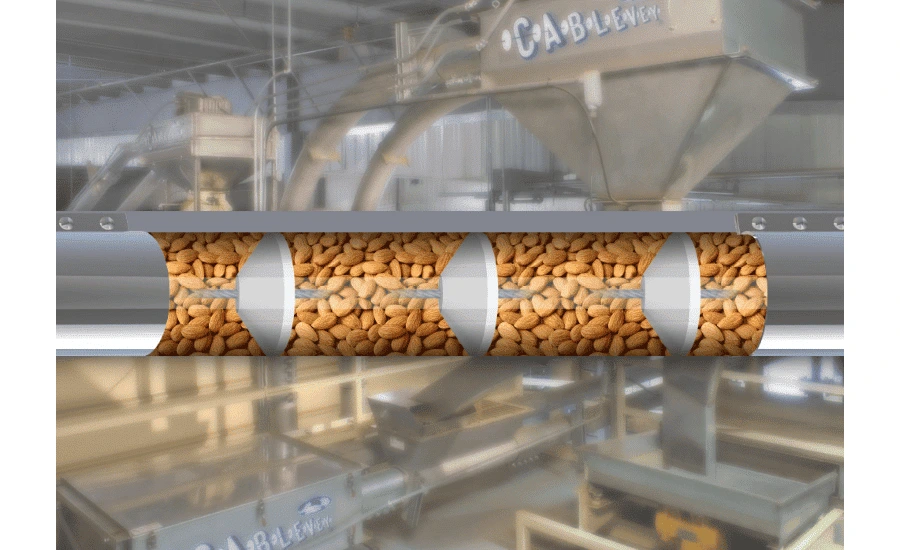
What Do Tubular Cable Conveyors Move?
Tubular cable conveyors are a versatile and efficient material handling solution that can be used in a wide range of industries and applications. However, they are particularly well-suited for the food processing industry, where they are commonly used for transporting fragile materials and blends. In the food processing industry, tubular cable conveyors are used to transport bulk materials such as:
- Snack food,
- Frozen food,
- Specialty grains,
- Nuts,
- Coffee beans,
- Pet food,
- Powders,
- Tea blends, and more.
The enclosed tube design of the conveyor provides a safe and hygienic way to transport these materials, while the high throughput and efficiency of the conveyor ensure that materials are moved quickly and efficiently.
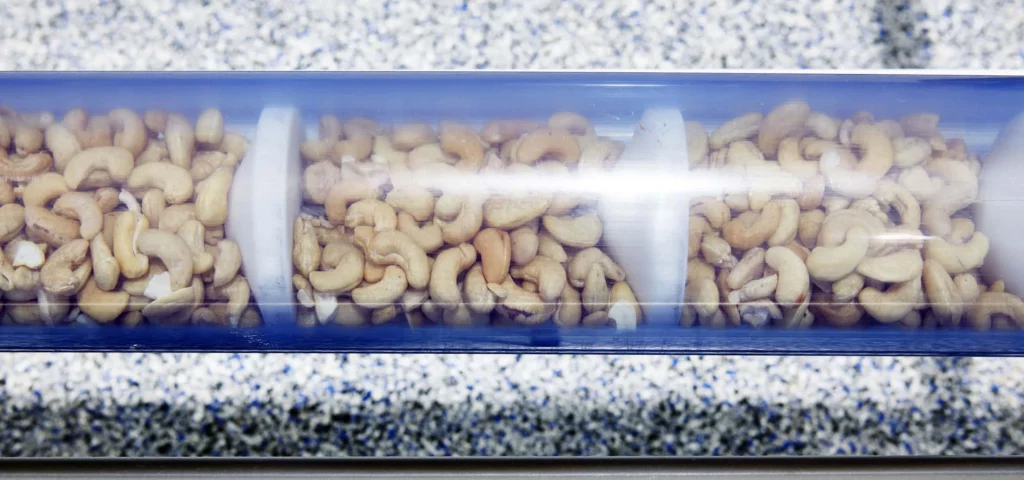
Main Benefits of Tubular Cable Conveyors
Tubular cable conveyors have revolutionized the movement and handling of materials across a variety of industries, playing an instrumental role in enhancing operational efficiency and productivity. From their ability to handle fragile goods to their user-friendly design and easy cleaning mechanisms, we will delve into what makes these conveyors stand out in the realm of material handling solutions.
The way the material is moved through a tubular cable conveyor ensures that it doesn’t jostle in any way. In fact, material breakage in this type of conveyor is kept to an absolute minimum. This is especially important in the food processing industry, where the integrity of the materials determines the quality of the final product. Take the example of Probat Inc, a world-renowned coffee supply company that relies solely on tubular cable conveyors (Cablevey conveyors at that) to convey its precious fragile material, the coffee bean
The flexible design of tubular cable conveyors allows for a compact and space-saving solution. This is especially useful in food processing facilities where space often comes at a premium. You can even opt for a modular conveyor that will allow you to choose which components you want now and which can come later when your business expands and you have more space to work with.
The enclosed tube is a barrier that prevents contamination of the conveyed materials. Food contamination can lead to a whole host of problems, not least of which are foodborne illnesses, loss of customer trust, damaged company reputation, and ultimately, loss of revenue. Keeping your conveyed ingredients in a contained loop ensures that none of this happens. Furthermore, the tube protects from spills and loss of product during production.
Many tubular cable conveyors include clean-in-place mechanisms that allow for easy cleaning and sanitizing of the conveyor. Essentially, they serve to clean your conveyor system without the need to disassemble it.
The tubular cable conveyor has few moving parts, meaning it requires minimal maintenance. This, in turn, leads to lower operational costs and less downtime. The lack of moving parts means less wear and tear, which results in a longer lifespan for the conveyor.
The design of tubular cable conveyors allows for high material throughput and efficiency, resulting in low energy consumption when compared to other conveyor types (such as an industrial conveyor belt for food, pneumatic conveyor systems, bucket elevators, and similar).
Screw Conveyor Design
Screw conveyors are mechanical conveyors, just like tubular cable systems. They consist of a tube or a trough through which a helix (or an auger) rotates, moving the material forward as it does. Auger conveyors are great for moving materials such as:
- Meat,
- Animal feed,
- Grain,
- Boiler ash,
- Bone meal,
- Food waste,
- Municipal solid waste, and more.
Disadvantages of Screw Conveyors in Food Processing
Significant material damage – The biggest disadvantage of auger conveyors in the food processing industry is that they are not gentle on the conveyed material. At all. The rotating helical blade slices through the conveyed product, grinding it against the side of the tube or the trough and ruining its integrity. This is why screw conveyors are not as good a choice for moving fragile materials as tubular cable conveyors.
No possibility of installing clean-in-place mechanisms – In fact, it can be quite challenging to clean the helix within the screw conveyor. The entire system needs to be shut down, and the cleaning process must be done carefully to ensure that even the hard-to-reach parts of the auger are spotless.
Inflexible design – Compared to tubular drag conveyors, screw augers are really inflexible. They can be used horizontally, vertically, or at an incline, but they take up quite a bit of space any way you place them. They are powerless against corners and tight sweeps in small facility spaces.
Low energy efficiency as the incline increases – Because the helix needs to work against gravity, energy consumption increases if the conveyor is positioned at a steeper angle.
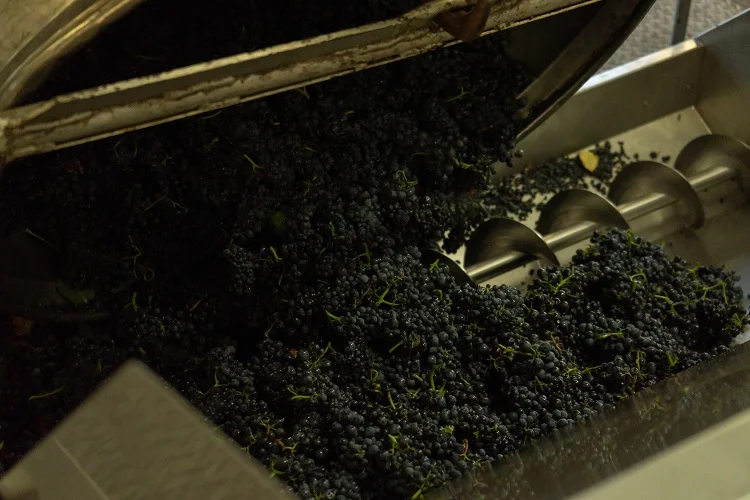
Tubular Chain Conveyor Design
Despite having a similar design at first glance, when you peer in, tubular cable and tubular chain conveyors have one significant (and somewhat obvious) difference – one uses a cable to move its discs through a tube, and the other uses a chain. But this seemingly inconsequential difference brings in a number of important disadvantages to the tubular chain system compared to the cable one.
Disadvantages of Tubular Chain Conveyors in Food Processing
Compromised food safety – The chain in a tubular chain conveyor is not sealed in nylon. It comes into direct contact with the conveyed material, increasing the chances of food particles getting stuck in between chain links. This drastically increases the risk of contamination and cross-contamination.
Significant system downtime – Unlike tubular cable conveyor systems, tubular chain conveyors don’t have a way to redistribute the load if a link breaks. If even the smallest thing breaks, the entire system needs to be shut down for repairs. Additionally, the chain sprockets require relatively frequent replacing, which means more money spent on replacement and spare parts and more system downtime.
Limited cleaning options – Tubular chain conveyors can have clean-in-place mechanisms, just like tubular cable conveyors. However, their options for dry cleaning processes are limited. Where a tubular cable conveyor has five different mechanisms for dry cleaning, a chain conveyor has only two. This severely limits how fast line changeover can happen in production and can compromise cleaning and sanitation levels.
Using more energy – Lastly, the chain in a tubular chain conveyor is 2.5x heavier than the cable in a tubular cable conveyor. Because of this added weight, a chain system uses up more energy than a cable one, meaning your power bill will be higher in the long run.
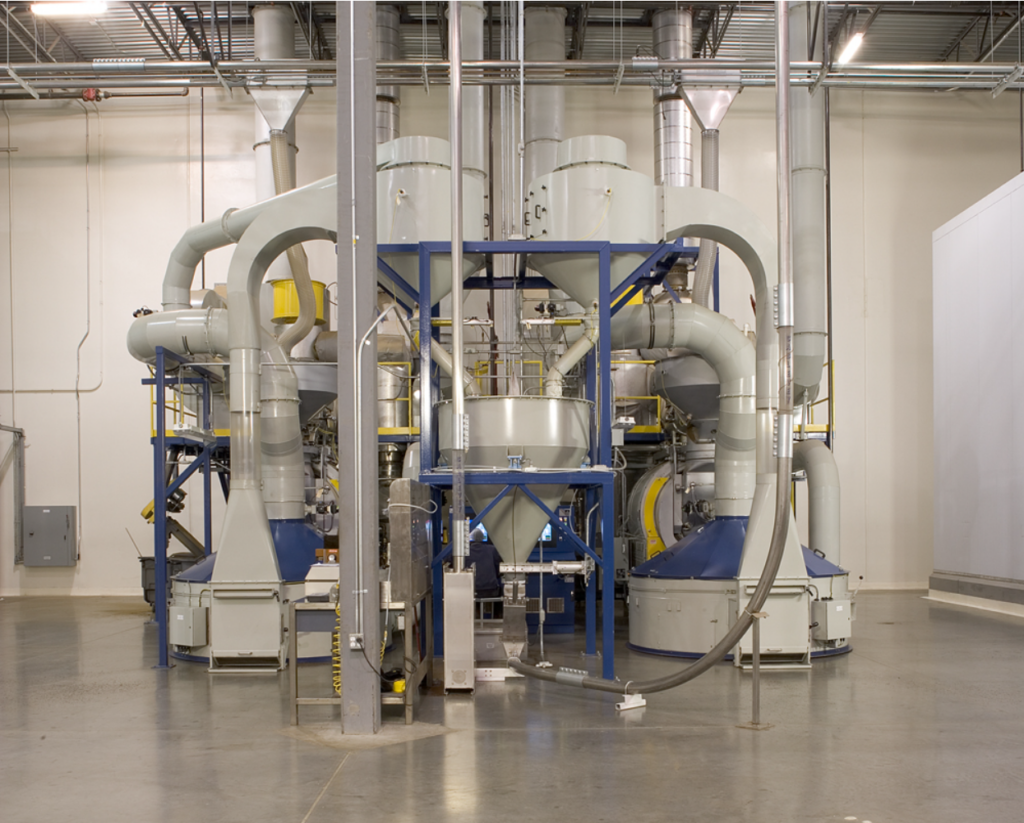
Pneumatic Conveyor Design
Pneumatic conveyors rely on compressed air to move material from point A to point B within a facility. There are positive pressure conveyors and negative pressure conveyors (also known as vacuum conveyors). Pneumatic conveyors convey material at incredibly high speeds.
Their design is relatively flexible, in that they don’t take up too much space and can accommodate multiple infeed and discharge points. They can convey products over long distances. Additionally, pneumatic conveying systems, just like tubular cable conveyors, don’t have many moving parts, making them easy to maintain.
Disadvantages of Pneumatic Conveyors in Food Processing
Significant product damage – Just like screw conveyors, pneumatic conveyors are not gentle on the conveyed materials in the least. Because of the high speeds at which the material is moved, the food particles slam against each other and the sides of the conveyor, easily breaking apart. This is one of the main reasons why pneumatic conveyors shouldn’t be used in moving delicate materials, such as nuts.
High energy consumption – If you want to slow down the conveying speed to try and preserve as much of your material as possible, you will find that it takes a lot of energy to do so. Indeed, if not used at its optimum speed, a pneumatic conveyor can rack up quite the power bill (using up to 10x more energy than a tubular cable system!).
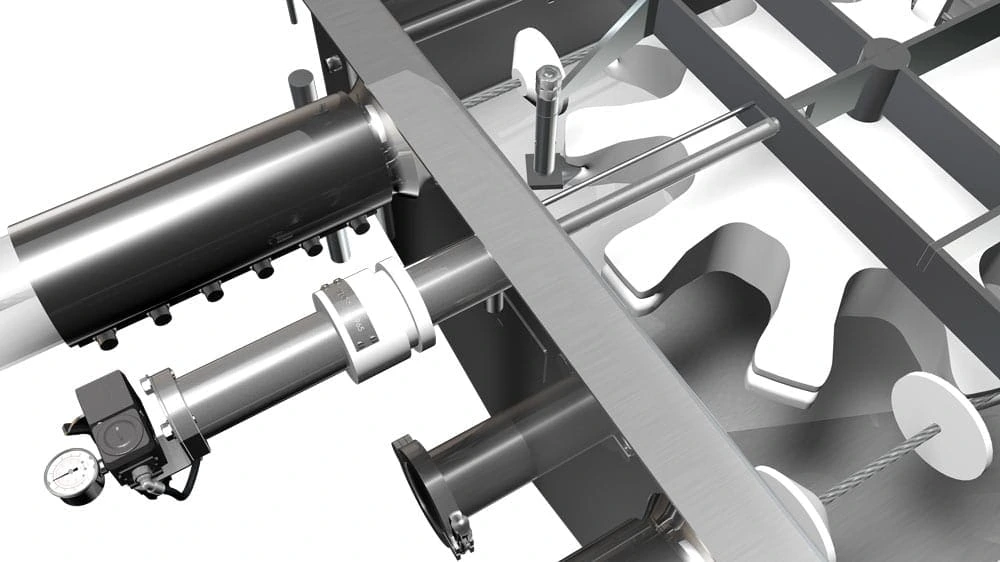
Is the Tubular Cable Conveyor the Right Choice for You?
While we have discussed how tubular cable and disc conveyors, as well as the conveyor belt system, can be superior to other conveyor types, it is important to note that this is only in the context of conveying fragile materials in food processing. Tubular cable conveyors are not well-suited for transporting materials such as sticky materials, liquids, viscous fluids, and similar.
When considering which conveyor system to invest in next, it is important to never lose sight of the nature of the material you would like to convey, as well as the potential limitations of your facility and budget. That’s why we offer product testing services. If you are interested in acquiring a tubular drag cable conveyor, you can test out how your material flows through our systems first. That way, you will know exactly what you’re getting and how it will impact the bottom line of your business.
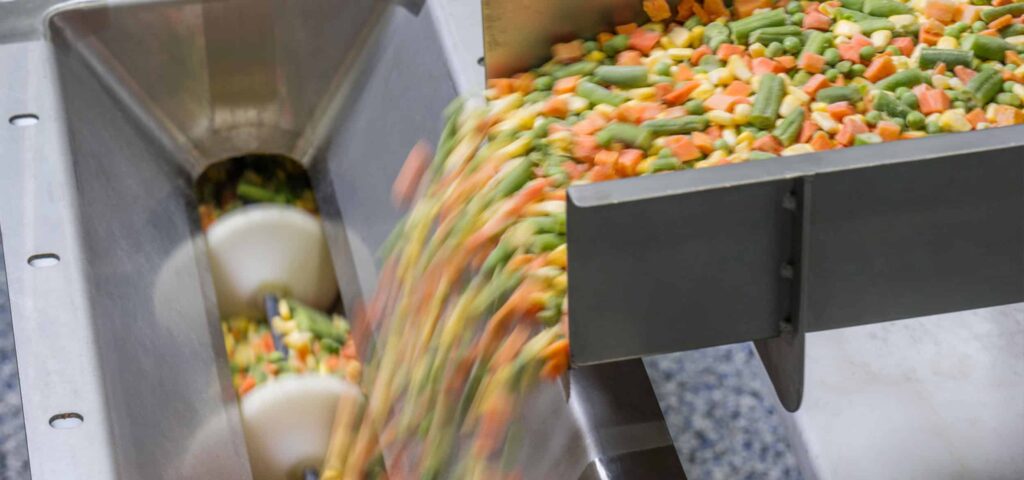
Our Automation Conveyor Systems Will Revolutionize Your Processes
Tubular cable conveyors can be the bulk material handling equipment you were looking for. They are mechanical conveyors that are exceptionally gentle on the conveyed materials, don’t require much maintenance or downtime, have special clean-in-place mechanisms, and are energy efficient. Moreover, tubular drag cable systems will effortlessly meet the strict sanitary requirements inside any food processing facility.
Compared to more traditional conveyors such as pneumatic conveyors, screw conveyors, and tubular chain conveyors, the tubular cable conveyor requires less space to operate well, is easy on the energy bill, and doesn’t affect the integrity of your material in any way. It also comes in a range of capacities to suit your business needs.If you’re ready to take the next step and improve your material handling process, add a custom conveyor belt for the warehouse, or enhance food processing, Cablevey Conveyors is ready to work with you to find the best solution for your facility. Don’t hesitate to contact us to discuss the possibilities of implementing a tubular cable conveyor.