In a strategic move to enhance efficiency and reduce waste, Hamilton Ranches, a prominent nut grower, swaps out a bucket conveyor for a tubular system designed by Cablevey Conveyors. This upgrade significantly cuts losses and accelerates cleaning times, showcasing the tubular system’s superior handling and maintenance capabilities. The switch optimizes the processing line and also ensures that the highest quality nuts are delivered with minimal downtime, reflecting a commitment to excellence and innovation in the industry.
Company Is Nuts About the New Pecan Conveyor
Operators at Hamilton Ranches Inc. can’t help but feel a bit nutty about their new pecan conveyor system. That’s because they spend their days processing pecans and walnuts. The family-owned company, based in Visalia, California, dehydrates about 750 dry tons of walnuts per day, but its main focus is on the cracking, shelling, and processing of pecans. The pecan meat is sold to candy manufacturers and other companies for use in food products.
At one step in the process, the company was conveying wet pecans via a bucket elevator to a dryer. However, there are several challenges that need to be overcome when conveying nuts like pecans. For starters, wet pecans tended to stick to the plastic buckets, creating a mess and causing operators to spend extra time cleaning the buckets and any spilled pecans from the plant floor. The company decided to replace the bucket elevator with equipment that would convey the wet pecans without any material loss or unnecessary labor.
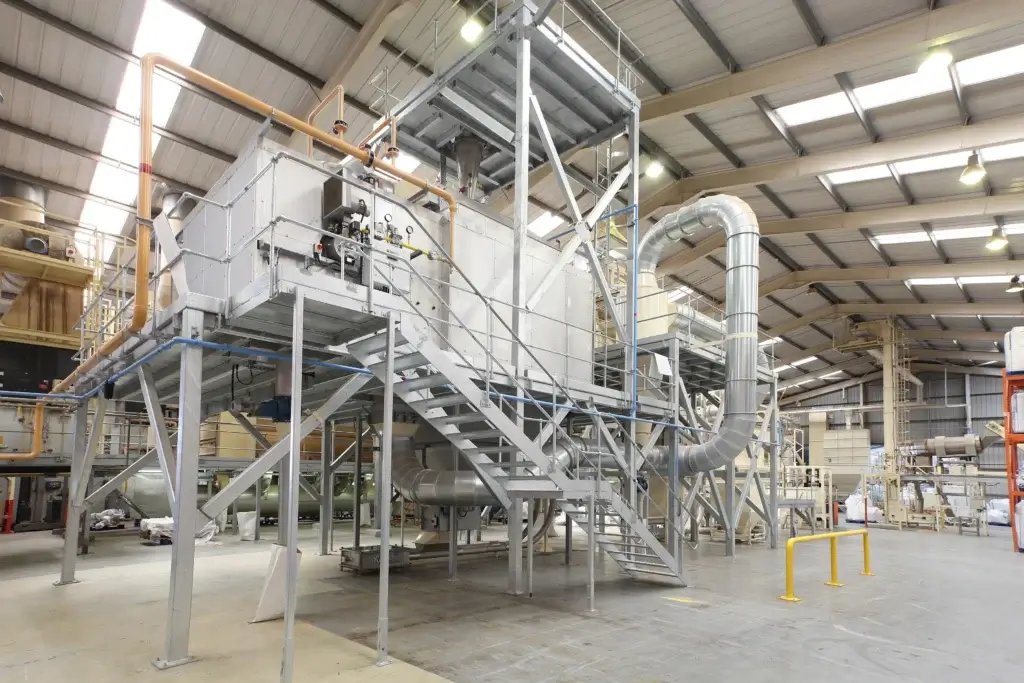
The Initial Stages of Pecan Processing
The company uses a flotation process to separate the pecan meat from its cracked shell. In this process, the pecans are put into a water-filled vessel where a combination of hydration and vacuum pressure causes the shell to fall off and sink to the vessel’s bottom and the pecan meat to float to the vessel’s top. There, the pecan meat discharges onto a shaker or dewatering table made of perforated metal.
The table shakes the excess water off the pecan meat, which is then transported to a dryer inlet several feet distant from and above the level of the shaker table. In the past, the pecan meat discharged off of the shaker table to a bucket elevator with plastic buckets and was conveyed up to the dryer inlet.
What Were the Problems With Bucket Elevators?
“We were experiencing major problems with the bucket elevator,” says Chris Hamilton, sales manager and engineer at Hamilton Ranches. “Because the pecans are wet when we convey them, they were sticking to the sides and bottoms of the plastic buckets. Once the pieces dried onto the bucket, it was really hard to clean them off. That was a big problem for us because we’re processing food, and the entire process needs to be sanitary.
In addition to that, pecan meat was falling out of the buckets and onto the ground. We were losing about two thousand pounds of meat per day using the bucket elevator. After spending a lot of downtime cleaning the buckets and the floor, we knew there had to be a better way to convey the pecan meat to the dryer.”
Searching for Replacement Equipment – What Was the Process Like?
About 2 years ago, Chris Hamilton began researching different nut conveyor technologies and suppliers on the Internet. He eventually found Cablevey Conveyors from Oskaloosa, Iowa, a supplier of tubular drag conveyors. Our website had videos of the equipment in operation, and Hamilton felt that the equipment offered the features that he was looking for in a conveying system. He contacted Cablevey, and we sent a local representative to the company’s plant with samples of the equipment to show how it would work for the company’s application.
“I checked out other conveyor suppliers, but their equipment didn’t operate the way I wanted it to,” says Hamilton. “The other equipment I found runs its motors so fast that it creates a vacuum. I didn’t want it to run that fast. I wanted it to go slow and just gently pull the material through the conveyor. The major selling point for me was that the Cablevey conveyor has an adjustable variable-speed motor that provides gentle material handling.”
The company filled out an application data sheet, and Cablevey Conveyors designed a tubular drag conveying system to suit the company’s requirements. “It was entirely customized for us, which was awesome,” says Hamilton. The conveyors can be configured in thousands of different ways to fit into an existing plant environment. The supplier shipped the equipment to the company, and company personnel installed it in July 2005. Because the company had ordered extra tubing, the only adjustment needed was to cut the tubing to the correct size. It took only a couple of days to install it, and it worked perfectly from startup.
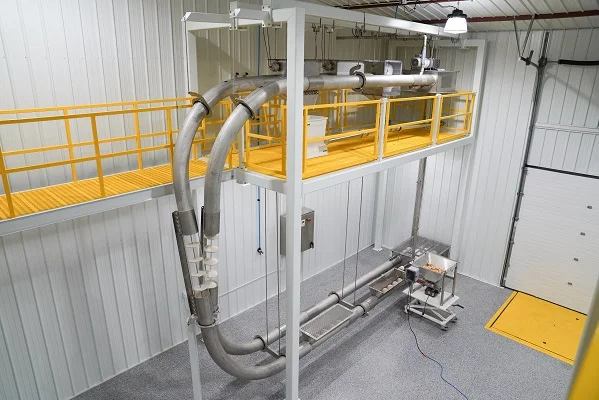
What Are the Features of a Tubular Drag Conveying System?
The Super 4 tubular drag conveyor is 18 feet tall and has Type 304 food-grade sanitary stainless steel construction. The fully automatic system consists of a gravity-fill inlet, 4-inch diameter tubing, an Ultra-Flex nylon-coated cable, ultrahigh molecular weight (UHMW) plastic discs, a drive unit with a drive sprocket, a free-flow outlet, and a tension turnaround unit.
The system’s components are connected with compression couplers and gaskets, making it a totally enclosed, dust-free system. The tube conveyor system is Z-shaped, with the self-tensioning turnaround unit located on the Z’s bottom leg below the gravity-fill inlet and the drive unit located on the Z’s top leg above the free-flow material discharge outlet.
Two 90-degree sweep corners alter the conveyor’s direction and the material path from horizontal to vertical and back to horizontal. The flexible cable has plastic discs attached every 6 inches and is pulled through the conveying tube by the drive unit in a 94-foot-long endless loop. The conveyor’s variable-frequency 3-horsepower electric motor allows the system to convey about 2,000 pounds of pecans every 2 hours.
Operating the Tubular Conveyor System
After the pecan meat has been dewatered, it falls off the end of the shaker table through the tube conveyor’s gravity-fill inlet and enters the conveying tube. The material falls in between the cable’s plastic discs, which gently and gradually glide the material through the tube without using air and causing any degradation. The material is conveyed horizontally until it reaches the first 90-degree sweep, where it changes direction to vertical.
Efficient Inspection for Optimal Performance
As the material is vertically conveyed, it passes through the tube’s clear plastic inspection section, which allows the operator to easily monitor the material as it’s conveyed. “The inspection section is great because it allows us to watch the material and make any necessary adjustments,” says Hamilton. “We can immediately see if the material is plugged or if the conveyor is running too slow or too fast. If we see that only a little bit of material is running through, we simply slow the conveyor down, and it immediately runs more efficiently.”
Another reason the inspection section is helpful is because the system runs so quietly. “The conveyor hardly makes any noise,” says Larry Van Zee, vice president of operations at Cablevey. “If there’s other equipment running in the plant, you probably won’t hear the conveyor at all. The inspection section allows the operator to see that the equipment is indeed running and conveying material without the operator having to turn off other equipment in the plant to double-check.”
Streamlined Discharge and Continuous Operation
After it passes through the inspection section, the material travels several feet higher until it reaches the second 90-degree sweep and changes direction back to horizontal. From there, it moves to the drive unit, where the cable and discs briefly leave the tube and are suspended in the air. During this time, the material falls by gravity out of the drive unit’s discharge outlet, onto a slide, and into the dryer, where the pecans are gently dried at low heat for about 2 to 5 hours.
The cable continues around the drive sprocket, exits the drive unit, and enters the return side of the tube. The return tube also has an inspection section, which allows the operator to monitor the tube again to ensure that the material has fully discharged and isn’t stuck to the discs. At the tail end of the tube, the cable enters the tension turnaround unit, which contains a sprocket that the cable travels around.
The turnaround unit also has a self-tensioning device with a safety switch that automatically shuts the conveyor down if the cable becomes too tight or too loose. The turnaround unit is located just before the gravity-fill inlet, so after the cable has wound around the sprocket, it picks up more material and begins the loop again.
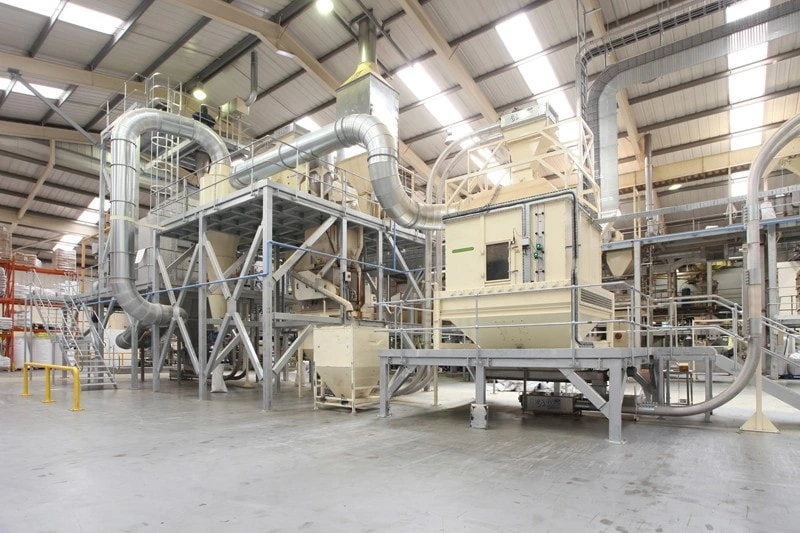
Keeping the Conveyor in Peak Handling Shape Is Crucial
To clean the tubular conveying system, polyurethane wiper discs are attached to the cable and are left on during operation. “The wiper discs make the conveyor pretty much self-cleaning,” says Van Zee. “They’re like oversized rubber washers that are larger than the tube’s inside diameter. They constantly keep the tube clean by eliminating any residual material and any chance of material buildup.” The wipers last about 2 months before they need to be replaced.
To change each wiper, an operator simply has to unbolt the old one and bolt a new one in its place. In addition to the wiper discs, Hamilton Ranches designed and installed a washdown system. Water lines are attached to the drive unit’s discharge outlet and to an inlet in the turnaround unit. As the cable winds around the drive sprocket, a nozzle sprays water onto the discs. The cable continues its loop as the water cleans the discs.
Efficient Cleaning and Maintenance System
When the cable reaches the bottom turnaround unit, the water exits through a small outlet, empties into a drain located on the plant’s floor, and exits into a basin located outside the plant. As the cable continues through the turnaround unit, another spray nozzle blasts a stream of water onto the discs. When the cable reaches the top drive unit, the water discharges onto a 10-degree slide and is collected on a plate that empties into a PVC pipe that runs from the top of the dryer down to the drain on the plant floor.
The dirty water exits into the outside basin. The washdown cycle takes about 5 minutes. “The conveyor is enclosed, so the entire washdown cycle is self-contained,” says Hamilton. “The water doesn’t spray everywhere, so there’s no mess. Since we’re handling food, the conveyor is cleaned out between every batch, which is up to four times a day.”
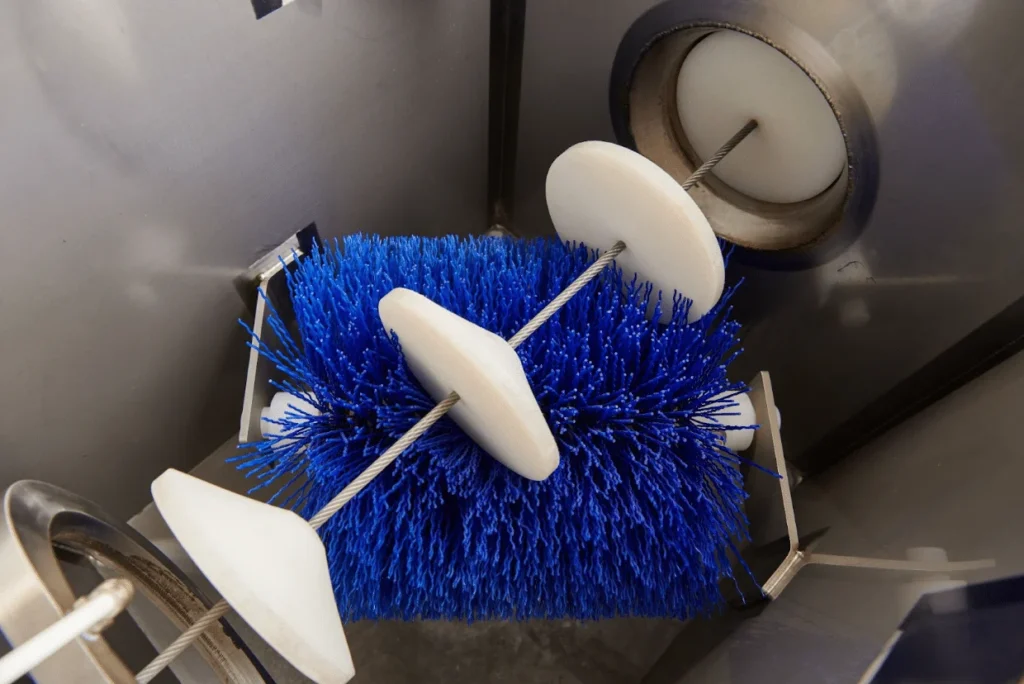
Tubular Drag Conveyor Offers Plenty of Benefits
The company has been extremely satisfied with the new tubular drag nut conveyor. “The conveyor was a simple, simple solution to our problem,” says Hamilton. “It’s been operating in our plant for more than two years, and other than replacing wiper blades, we haven’t had to do any repairs or replacements. The wiper discs constantly keep the tube clean by eliminating any residual material and any change of material buildup.”
Streamlined Operations and Reduced Labor
Since the installation, the company has experienced a reduction in labor needs. “We needed an automatic system badly because California has been raising the labor rates,” says Hamilton. “With the new conveyor, we only need one operator to run the machine. Plus, the conveyor is never down – it just keeps plugging along without any problems.
An operator basically puts whole pecans in at one end of the processing line, monitors the equipment for four to five hours, and then the pecan meat discharges into a bin at the other end of the line and is ready to be sent to grading tables.” “We’ve been so happy with this conveyor,” says Hamilton.
“We knew the instant we turned it on that it would completely solve our problems. Plus, we’re very pleased with the supplier’s customer service. We get around five requests a year from other nut processors asking if they can come and look at the conveyor and our processing line because they’re experiencing the same problems we used to have. We always feel comfortable recommending this conveyor.”
Contact Cablevey Conveyors for Customized Conveyor Solutions
When your operation demands customized conveyor technologies tailored to your specific needs, look no further than Cablevey Conveyors. Our team of experts is ready to collaborate with you to design a system that not only meets but exceeds your expectations. With a focus on gentle handling, efficiency, and cleanliness, our conveyors are ideal for a wide range of applications, from food and beverage to nuts and grains. Whether you’re upgrading your current system or designing a new facility, let Cablevey be your partner in achieving optimal production efficiency. Contact us today to explore how we can help streamline your conveying needs with precision and care.