Leveraging tubular cable conveyor process automation can significantly revitalize your operations. However, upgrading your roasting plant can be a challenging task. Before bringing in new machinery, the benefits of modernization are clearly visible.
Your current operation might look outdated and seem to be operating beyond its optimal capacity. Not only are the labor costs skyrocketing, but rivals are also persuading your customers with claims of superior quality and freshness, courtesy of their more modern plants, which enhance efficiency and skill in every step of the roasting and packaging process.
Addressing Unforeseen Challenges in Plant Modernization
However, adopting the tubular cable conveyor process automation isn’t without its pitfalls. Many have shared terrifying accounts of roasters initiating new plant setups, only to realize later that specific elements are incompatible with each other. Upon initiation, it becomes evident that despite the continuous adjustments, calibrations, and tweaks, the labor expenses have surged due to increased downtimes, leading to missed shifts and extended hours.
Additionally, the newly introduced packaging strategies, despite their fresh and modern appeal, haven’t found favor with your clientele. The redesigned format doesn’t accommodate the designated shelf space adequately, and the bags are prone to easy damage. Retail customers, who are enthusiastic about your new offerings, tend to handle every bag excessively while making a selection, resulting in noticeable wear and tear before they finally make a purchase with a 12 oz. bag of coffee.
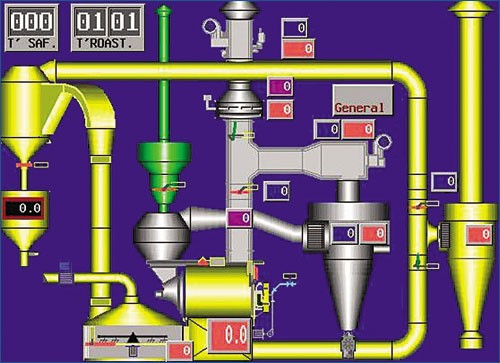
Rules of Thumb for Cable Conveyors
Keep in mind that the equipment you invest in now might be the same equipment you wish to upgrade from and sell in the future. Similar to a vehicle, several factors, such as the resale value, the credibility, and the track record of the vendor, as well as the quality standards of your machinery, hold significant importance.
While you might not be concerned about your equipment adhering to international standards, a prospective buyer might value this, potentially broadening your market scope when the time comes to sell. Additionally, consider the availability of spare parts both now and in the future, possibly even 20 years down the line. Will they still be accessible?
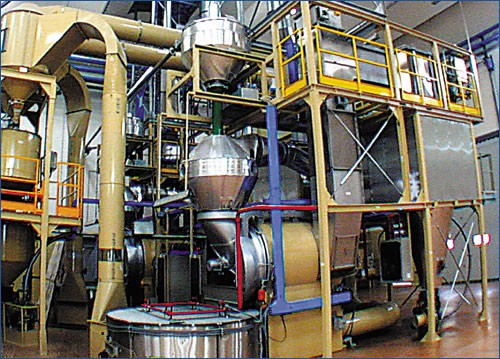
How to Approach Tubular Cable Conveyor Process Automation
Ensure that the different pieces of equipment you plan to purchase are compatible with each other. If a single company is managing your setup, they would be accountable for this harmony. If not, it’s your duty to guarantee that your conveyor doesn’t transport products at a speed that surpasses your roaster’s capacity to roast. Procure references from potential vendors and make a point to connect with them. Don’t simply presume that all the references will offer positive feedback – you might find that some contacts were not even aware that they were listed as references.
Leverage the Community Experience
Remember, the roasting community is renowned for its camaraderie and willingness to share knowledge. Don’t hesitate to request a visit to another facility to see and possibly operate the equipment you are considering. The members of the coffee roasting community are known to be amongst the most generous individuals globally in sharing insights.
We recently engaged in conversations with several reputable equipment vendors to understand the current trends and developments in the industry. While their viewpoints varied, all emphasized adopting a meticulous, well-studied, and systematic approach when selecting and installing any new equipment.
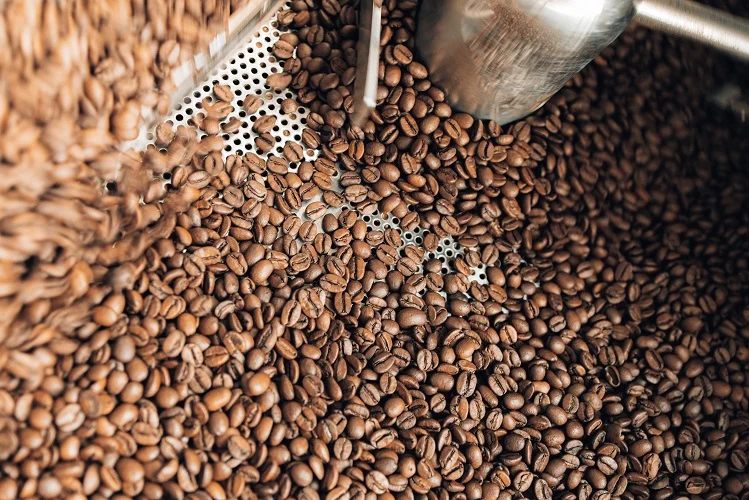
Insights from Industry Veterans, Starting With Howard Weiss
Our initial conversation was with Howard Weiss, the chief executive at Texpak Incorporated, the exclusive agent for Scolari Engineering in the USA and Canada. Before the outbreak of the Second World War, Scolari acquired a firm that specialized in manufacturing roasting machines for a variety of needs, but now their focus is primarily on coffee. Weiss elucidated that Scolari Engineering, based in Milan, Italy, pioneered the market by being the first to offer commercial roasters operated through personal computers. This venture became more intensive following the creation of the IBM personal computer.
“Our systems have a lot of information that is important to clients. We have factory integration that ties into the enterprise’s own operational software and affects everything from sales and packaging materials to different types of coffee.”
“We make continual improvement on our programs,” Weiss claims. “We’ve got several hundred roasters on our PCs that help us improve what we’re doing by giving us input because roasters do things in their own unique way. The computer gives the roaster operator a better set of tools. It plays a role even in the consistency of the roast and in barometric pressure. The roaster may elect to use many or few of the tools, but giving them the tools allows them to do a better job.”
Although a 6-bag drum roaster is not a particularly large task for Scolari, Weiss said that they are pleased with the details.
Weiss on Computerized Silo Systems
Systems for storing green and roasted coffee in silos are computerized so that when a batch of green coffee is created, the computer may download the specifications for that specific batch.
“Through the use of the computer, we’ve also improved the conveying of coffee,” Weiss says. “The lots are tracked through the entire production process. This is important, especially if you’ve ever had a product recall. Roasters can be very technical, so the cost of the controls themselves can get expensive. But as the coffee moves, it gets tracked, and that gives control. The roaster ultimately will yield a better and much more consistent product because of the tools and technology offered. You’d be surprised at some of the technology that’s still being used out there, 80-90 years old!” Weiss has exclaimed.
Stepping Wisely Towards Automation
When asked about advice for companies considering the shift towards automation, Weiss recommended a gradual approach. “It’s better if companies go one step at a time to upgrade and update their automated systems. They can do green coffee one year, roasted coffee the next year,” he suggested. Weiss emphasized that the transition isn’t solely about incorporating flashy features. “You know, customers can taste the difference between Scolari grinders and the older style grinders that are not computerized. Our grinder has enough difference that it can be tasted.”
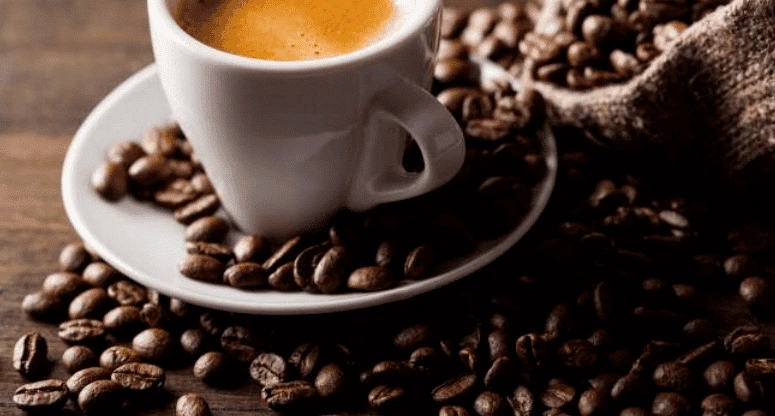
Striving for Consistency – A Chat with Diedrich Roasters’ Michael Whitley
Next, we had a conversation with Michael Whitley, who holds the positions of Sales and Marketing Director, as well as the Interim General Manager at Diedrich Roasters, located in Sandpoint, Idaho. Whitley emphasized the role of automation in enabling a roaster to replicate popular profiles effortlessly and multitask efficiently. The prime focus at Diedrich is to achieve absolute consistency in the roast profile. While Whitley recognizes the existence of various fads and trends in the industry, he maintains that the approach adopted by Diedrich sets it apart.
“Our standard is for slow, controlled growth. It’s a family business with a passion to develop very high-quality roasting profiles. We develop roasters, equipment, and roastmasters (through Diedrich training programs) that address the growth of any business as a whole, not just spot training. It’s important to ensure quality and consistency from growing and harvesting to the roast profile itself. Any roaster can now store, edit, modify, and duplicate roast profiles accurately. This really expands the roaster’s and the business owner’s toolbox.”
Introducing the Versatile Diedrich Automated Roast Control System
Diedrich offers a product known as the Diedrich Automated Roast Control System, a versatile tool compatible with any roaster, not exclusively those from Diedrich. For in-store roasters, this system resembles a tall cabinet equipped with a touchscreen interface at its summit. It boasts the ability to store or modify over 40 roast profiles, replicating precise parameters with ease.
A notable feature of this system is its intuitive “teach function,” which allows for the instant saving of manually roasted profiles, coupled with added functionalities such as password security. Its commercial counterpart sports a more streamlined appearance, featuring a slender monitor attached to a mounting arm and furnished with a vibrant 10- or 12-inch touchscreen display.
“These features give the roastmaster precise control. We developed these criteria to modify any roasting system. We’ll overbuild before we take any shortcuts. We could retrofit roasters, but you still have the same grade of equipment unless you start with the auto system.”
Diedrich’s Relentless Pursuit of Perfect Roast Profiles
What propelled the evolution of Diedrich’s roast profile automation?
“Having to work with a live biological product like coffee made it necessary. We were concerned with duplicating things like temperature, airflow, and timing. We had a Siemens engineer who helped us out. Automation used to be a modulating gas system where only two or three target temperatures get developed for the roasts.”
However, the Diedrich system transcends these constraints.
“It records in milliseconds and reports the roast profile in progress every 15 seconds” via a digital display. “It can store many profiles. We’re pretty relentless about the pursuit of precision, detail, and quality.”
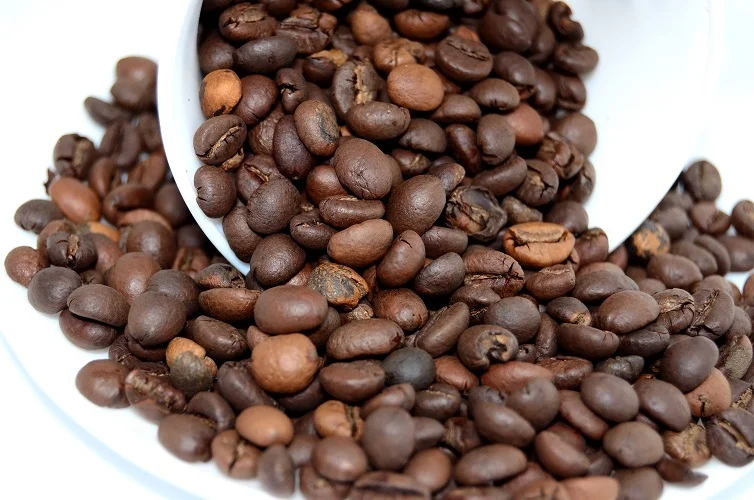
Pioneering Automated Solutions Beyond Individual Roasters
Our conversation series continued with Tim Reardon, the product marketing manager at Key Technology, headquartered in Walla Walla, Washington. Established in 1948, the company is adept at crafting automated solutions for processing various commodities, including food, tobacco, and plastics, among others.
Their advanced systems offer features like optical sorting and shape-based categorizing, equipped to make swift judgments on substantial volumes, often surpassing the capabilities of channel sorters. While their involvement in the coffee sector spans nearly nine years, their primary collaborations are with larger plants and manufacturing entities rather than individual roasters, a topic that promises to unravel interesting insights in an upcoming article.
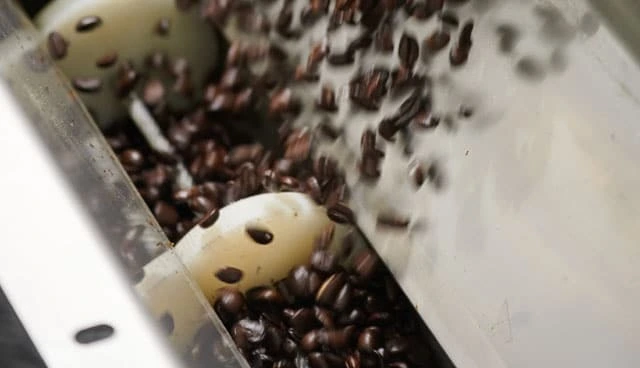
Cablevey’s Journey – From Agribusiness Origins to Conveyor System Excellence
Next, we had a dialogue with Gary Hall, the CEO of Cablevey, a company rooted in Iowa since 1974. They are renowned for their expertise in crafting conveyor systems catering to both industrial and agricultural sectors. Initially founded by Hall’s father and uncle with a primary focus on agribusiness, Cablevey has now expanded to encompass a comprehensive range of services related to enclosed tubular drag conveyor systems.
“Our system is very flexible,” Hall says. “It enables clients to use their processing space. As they grow, they can add to their conveyors. There is an acrylic tube to view the process, and the client can handle the material without degrading the coffee product. The coffee business took a long time to appreciate this kind of automation. But Cablevey also didn’t see the coffee industry as a market — at first. Now, many installations have occurred for coffee roasters, especially in the last five years.”
Preserving Aroma and Ensuring Clean Transitions
A case in point is a coffee roasting firm that approached Cablevey seeking a sealed system capable of retaining nitrogen and preserving the rich aroma of the coffee. They headed straight to the Cablevey Conveyors facility to conduct tests with both flavored and unflavored coffees. Although the minimum setup they have accomplished for coffee roasters is around half a million pounds, they are equipped to undertake projects as cost-effective as $5,000, which might be more suited for spices or teas.
Depending on the requisite steps – be it roasting, flavoring, grinding, or packaging – the processed beans or ground coffee traverse through the plant via conveyors in diverse manners. A distinctive feature of their setup is the Cablevey clean-out disc that travels through the tubing during operations, ensuring the elimination of lingering flavors. This disk, fashioned from urethane and slightly exceeding the tube in size, effectively cleans the inner surface of the tube, maintaining the purity of each batch.
Cablevey’s Expansive Portfolio – From Renowned Coffee Brands to Diverse Industries
Hall shared insights into several successful installations that Cablevey has accomplished, featuring prominent names such as Green Mountain Coffee, Paul Newman’s Shape, Van Houtte, Wrigley’s Gum, and Unique Coffee based in Staten Island. “But no tea applications have come in yet!”
Beyond their work with coffee companies, he informed us of Cablevey’s diverse portfolio, which extends to collaborations with breweries, the development of pet food systems, ensuring pellet integrity, and projects with the renowned Bong Brothers in Hawaii.
“One of the first installations Cablevey ever did in coffee was for a small roastery in Kansas City.” The proprietor had encountered Cablevey in Boston a couple of years prior and was so impressed that he aspired to integrate it into his own operations.
The Superiority of Cablevey’s Tubular Drag Conveyor System
“Our tubular drag conveyor system has a slow, slow speed. Every six inches, a hockey-puck-sized device gets dragged through the line. And we have two-inch, four-inch, and six-inch systems.” The availability of these different configurations provides a versatile solution adaptable to both compact and expansive coffee/tea processing setups.
“What the coffee industry especially likes is that there is less than 1% breakage with our system as compared to 5-6% breakage using a bucket system.” He recounted his visit to a roastery where traditional bucket elevators and pneumatic conveyor systems were still in use. The efficiency of their technology, he emphasized, stems from the design of the disks, which function similarly to a rail car, ensuring the product reaches its destination intact and without breakage, he noted with palpable excitement.
Strategic Investment in Equipment
Purchasing equipment is inherently a substantial investment, consuming not only financial resources but also significant amounts of time and effort, even in the preliminary research phase. When the need to acquire new machinery becomes imperative, proceeding with caution and utmost diligence becomes a necessity. It might appear excessive to travel great distances just to witness a piece of equipment functioning in real time. However, this could potentially be less wasteful compared to installing a unit in your facility that might turn out to be unsuitable, causing persistent issues for you and your workforce for years to come, not due to any fault in the machinery itself, but owing to its incompatibility with your specific setup.
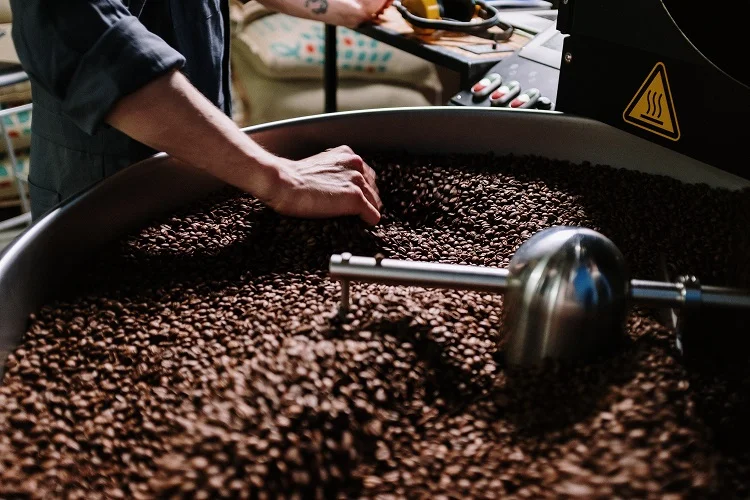
Choose Cablevey for a Seamless Transition into the Future
In the dynamic world of coffee roasting and manufacturing, the efficiency and adaptability of your conveyor belt system can fundamentally redefine the productivity and quality of your output. Cablevey Conveyors stands as a beacon of innovation, offering belt conveyor system solutions that minimize waste while ensuring the integrity of your product. Don’t let the intricacies of the industry hold you back. Elevate your operations to new heights with Cablevey’s pioneering bulk material handling equipment solutions, where durability meets sophistication.
Take the decisive step towards revolutionizing your business. Visit our website or contact us directly to explore how Cablevey Conveyors can tailor a solution that aligns with your goals. Together, we can craft a future where excellence is not just an aspiration but a tangible reality. Whether it’s a custom conveyor belt for a warehouse or an industrial conveyor belt for food, invest in Cablevey Conveyors – where your vision meets our expertise.