Embark on an exploration into the efficiency and innovation of material handling with tubular drag conveyors. But first things first – what are tubular drag conveyors, and how do they work? This inquiry unveils a technological marvel that has shaped industries for over five decades. Join us as we unravel the intricacies of these conveyor solutions and delve into the seamless synergy of tubular chain and cable conveying systems.
What Are Tubular Drag Conveyors, and How Do They Work?
Tubular drag conveyors belong to the category of a mechanical conveyor belt system, functioning by gently pulling bulk materials through a sealed tubular space. This tubular space can be made of steel, fiberglass, or plastic, depending on the industry where the conveying system is used. The maximum conveying speed achieved with a tubular conveyor is approximately 2,000 cubic feet per hour (56.6 m3/h).
Inside the tube, discs are evenly spaced along the length of a cable or a chain. This is why there are two main tubular drag conveyor types – cable and chain conveyors. The ends of the tubular conveyor form an endless loop because they are connected. The entire system is powered by a motor-driven sprocket that sits within a tube.
Versatility and Gentle Handling – Explore the Tubular Conveyors’ Diverse Applications
The tubular conveyor technologies have been around for over five decades. They are crucial for a wide range of industries, including the food and beverage industry. This type of conveyor is an excellent material handling solution for a variety of fragile materials that need to be handled gently:
- Powders,
- Pellets,
- Granules,
- Shavings,
- Flakes,
- Dust,
- Chunks.
Due to their design, these industrial conveyor systems can be installed on inclines as well as declines, making them very versatile for any application. They transport materials horizontally, vertically, at angles, and around corners without any problems. If you wish to transport any blended materials, tubular drag conveyors can achieve this without causing separation.
Modular Excellence – Customization and Dust-Free Precision in Tubular Drag Systems
A tubular drag system has a modular design, allowing for changes in the number and position of inlets and outlets and conveyor length and routing. The main benefit of these automated conveyor systems is that they ensure an enclosed, dust-free environment. They are ideal for the food processing industry (among others) because they prevent food contamination and reduce the risk of dust explosions and health hazards.
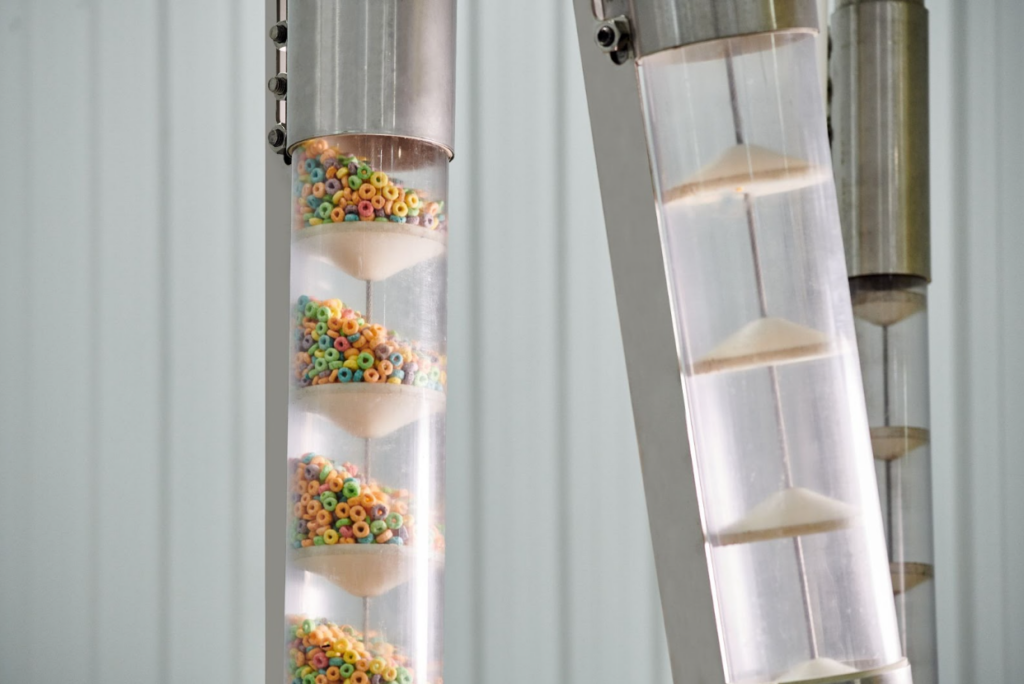
Tubular Chain Conveyors Enhance Material Flow
A tubular drag chain conveyor features a stainless steel chain that smoothly traverses the tubing system, facilitating the gentle movement of the product. This conveying solution comes in two types to correspond with two chain variations: roller and link chains. Attached to the chain are solid circular discs, also known as flights, responsible for pushing the material through the tube.
The link chains offer the advantage of facilitating changes in conveying direction across multiple planes, acting as a universal joint. This design allows a single conveyor to transport a product in various directions, providing adaptability to specific requirements. Roller chains, on the other hand, are not as flexible. They are made from interconnected plates and allow only one-dimensional movement.
Chain Maintenance and Sanitation Excellence: Meeting FDA Standards in Conveyor Systems
These chains can be made of stainless or carbon steel. A tension turnaround unit maintains the proper chain tension during operation. Because they have to meet strict FDA sanitation regulations, the chains are acid and corrosion-resistant, and the guidelines for their cleaning have to be followed to a tee.
This is especially true for a roller chain because food particles can become trapped between pins, bushing, and plates. Additionally, water may not drain properly after cleaning, leading to product contamination. Cleaning options for chain conveyor systems include dry cleaning and wet cleaning mechanisms.
Dry cleaning mechanisms include chain knockers – a rotating line insert that dislodges the dirt particles by knocking against the chain and brush box – and a line insert that mechanically brushes accumulated material fines off discs.
The wet cleaning mechanism consists of a three-step process that happens within the tube:
- Foam cleaning and sanitizing – a high-foaming cleaning solution is injected into the conveyor tube to remove and sanitize accumulated particles.
- High-pressure rinse – a water stream that washes off all materials from the inside of the tubes, including the foaming solution.
- Dry air – Warm air is blown through the tubes to dry them. After that, the conveyor is ready to resume operation.
Chain manufacturing conveyor systems can convey a maximum of 80,000 pounds/h (36,287 kg/h) of a dry food product, depending on the bulk density.
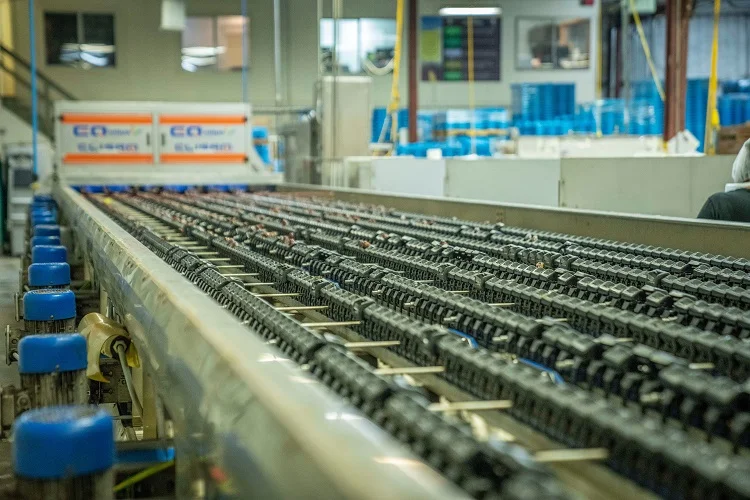
Tubular Cable Conveyors Enhance Cleanliness and Durability
Unlike the chain conveying system, the cable system has a cable running the length of the tubular housing. It is a stainless steel cable but also sealed in a nylon jacket, making it more difficult for food particles and debris to accumulate in the cable strands.
In most tubular drag conveyors, you will find a WSC (wire strand core) cable, which is widely used in aircraft. These are incredibly high-tensile cables that will not break under normal working conditions. Their core is made from type 316 stainless steel and is surrounded by steel-stranded ropes.
Discs used in cable conveyors are solid and attached directly to the cable without any bolts or screws. All of these components are easily removable for efficient and hassle-free cleaning. Tubular cable conveyors also have more cleaning options than chain ones.
This being said, here are what dry cleaning mechanisms involve:
- Brush box – the same type of mechanism as in chain conveying systems.
- Urethane wiper disc – the insert that cleans the inside of the tubing by wiping away material particles while the system is still running.
- Air knife – a stream of high-pressure air positioned at the locations where the product is discharged from the line. This air blows accumulating fines off the cable and the discs.
- Sponge disc and sanitizing cleaner – This involves the use of a single-use sponge disc designed to clean the interior of the tubing with the assistance of a cleaning agent.
- Bristle brush – This mechanism employs a specialized brush for cleaning purposes.
Wet cleaning mechanisms are similar to chain solutions, with the main difference in the third and final step:
- Foam cleaning,
- Sanitizing rinse,
- A water rinse is a second stream of hot water that removes the sanitizing rinse, ensuring the tube is ready for production.
Tubular cable conveyors can move a maximum of 80,000 pounds/h (36,287 kg/h) of a product, just like chain conveyors. This depends on bulk density and the conveying tube diameter.
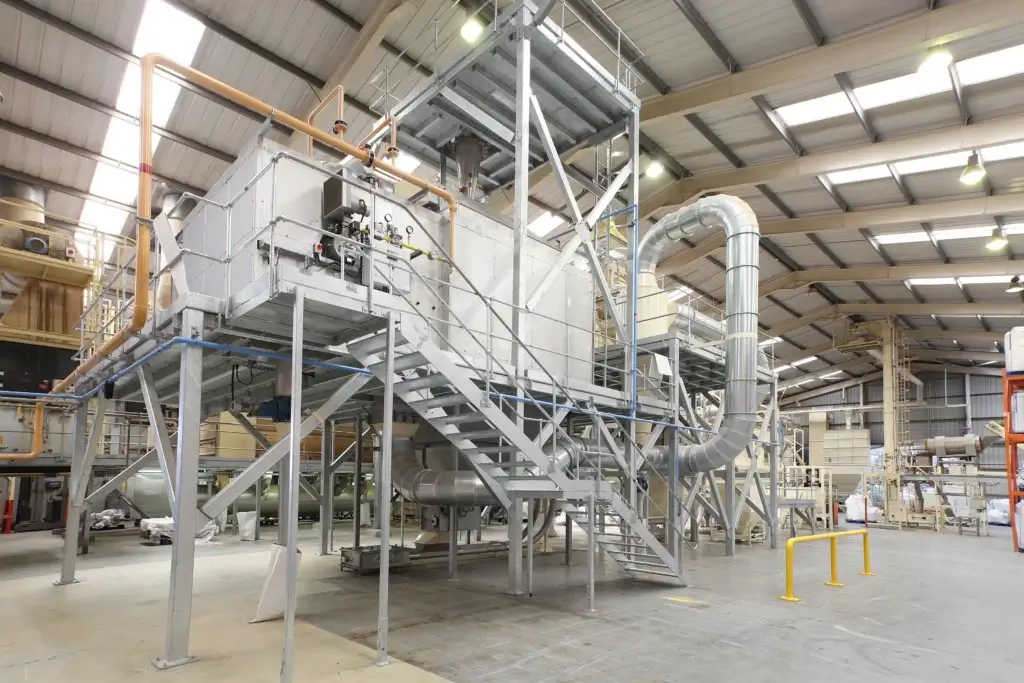
Cable vs. Chain Drag Conveyors – Which Option Is the Best for Your Material Handling?
At first glance, tubular drag chain and cable conveyors might seem similar. And they are, generally speaking. But there are a few key differences you have to take into account, especially if you are looking for an automatic conveyor system as a food processor:
Cost
Both cable and chain conveying systems require a medium upfront investment. However, tubular drag chain conveyors have a high maintenance cost – they require more frequent maintenance and part replacement than cable conveying solutions. This is especially true for round-link chain systems.
Their sprockets tear up often, causing businesses to experience prolonged downtime and high maintenance costs. Additionally, cable systems require less horsepower than chain ones, leading to lower operating costs.
Food Safety
Both tubular chain and cable conveyors are enclosed systems that prevent outside contamination and ensure a clean environment. However, there are significant differences when it comes to the safety of the product inside the tube.
Chains have more of their surface area exposed to the product. Food residue tends to collect in the straight-angle connections, which is difficult to clean and sanitize.
In comparison, nylon-coated cables have a smooth surface without any crevices or components where particles could gather. A cable has minimal surface area exposed to the product compared to a chain.
Cleaning Options
As outlined earlier, cable conveyors have a wider range of cleaning options available, unlike chain systems. This makes it easier to keep the entire system sanitary and up to standards for the industry you’re in.
Strength
Cables are typically used for elevators, aircraft control systems, cranes, and bridges. They are roughly 25% stronger than chains, which find their use in transportation vehicles mostly.
Even though chain conveyors are useful in specific situations, tubular drag cable conveyors are a more cost-efficient, sanitary, and versatile option.
Choosing Success and Tailoring Your Material Handling With Cablevey Conveyors
Not every automated conveyor system is suitable for every business. However, if you are handling fragile materials, such as breakfast cereals, pellets, nuts, snack foods, and similar, you will benefit from tubular drag conveying systems.
The difference between chain and cable conveyors is important when choosing the right system. With cable conveyors, you will spend less money on energy and maintenance costs. They meet all the food safety requirements – the cable that runs through the system is not as exposed to food materials as a chain is in chain conveyors. Additionally, cable conveyors have more cleaning options than chain ones.Do you have any questions or would like more information about tubular drag conveyors? Feel free to contact Cablevey Conveyors, one of the top-notch conveyor systems manufacturers.