Specialty grains are valuable for a reason – they are in high demand, and as such, they need to be processed with minimum loss and damage. But how to avoid common issues with specialty grain conveying? The following post will discuss these issues and present solutions to the problems associated with the processing of specialty grains.
What Are Specialty Grains?
In the past, grains such as wheat, corn, and soybeans have been processed with various machines, from grinders to sieves and centrifuges. However, in recent years, there has been an increase in demand for specialty grains such as rye, oats, rice, millet, and barley. This increase in demand is primarily thanks to growing public awareness about food intolerances and food allergies.
Specialty grains represent a great alternative to wheat and soybeans for people with these intolerances. The increased demand has also been encouraged by the popularity of gluten-free diets, such as paleo or ketogenic diets. Specialty grains are fragile grains that need to be processed with care – they are expensive, and if they’re meant for direct packaging, the level of product damage needs to be dialed down to a minimum.
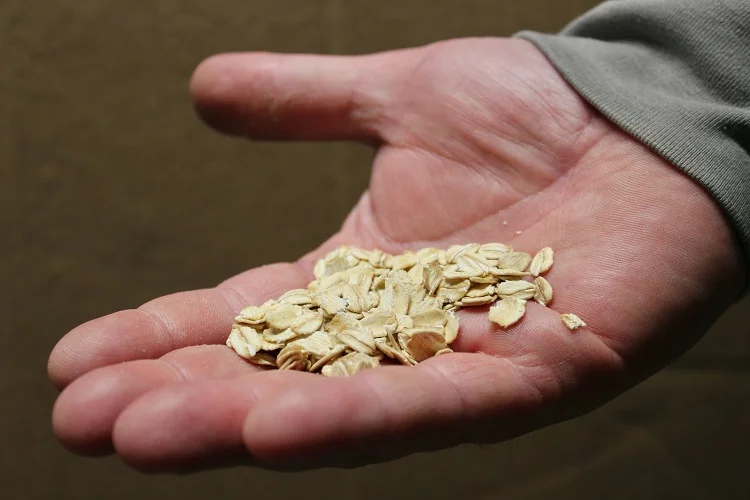
What Are the Most Common Grain Handling Issues?
Moving stored grain from one part of a facility to another may sound like a relatively simple task. However, it can be a challenging process that should not be taken lightly if the product has value and sells at a premium price point. In the following section, we will talk about the most common conveying challenges associated with grain handling and answer the following questions:
- How to reduce breakage?
- How to deal with dust hazards?
- How to monitor grain quality?
- How to minimize loss and retain value in the products?
Contamination and Cross-Contamination Are Major Concerns
In any food processing facility, contamination and cross-contamination are major concerns, and a lot of effort is put into avoiding these issues. This is especially true with sensitive products such as specialty grains that need to be handled in a cleanroom environment and can easily absorb dust and debris from the air.
In the food industry, contamination refers to the introduction of foreign substances that should not be in a product. Contaminants can be physical (such as a glass shard, wood splinter, or piece of metal), chemical (such as a pesticide), or biological (such as pathogenic bacteria).
There is also the possibility for cross-contamination, which occurs when one batch or lot becomes exposed to another during production or transportation (this may happen due to equipment failure, poor work practices, or human error). Cross-contamination can have serious consequences for product safety and could lead to a food recall.
Grain Dust Can Cause Various Problems in the Production Process
Grain dust is one of the most significant issues for grain processing facilities. It can cause respiratory problems and allergies in workers, increase the risk of fire or dust explosions, and clog machinery if not properly eliminated. According to a report from Dust Safety Science, in 2020, at least 165 fires and 60 explosions were caused by dust worldwide – they resulted in 88 injuries and 10 fatalities.
One of the biggest contributors to the dust problem in a food plant is an open belt conveyor system. For example, the use of an open custom conveyor belt system (or open bucket elevators or roller conveyors) can lead to a significant accumulation of dust in an air intake system and ductwork. This is the main reason why many food processors are reconsidering open conveyor systems and opting for an enclosed industrial conveyor belt for food instead.
Grains Are Prone to Damage – These Materials Are Fragile
Grains such as oats, rye, and other specialty grains are fragile, making them more prone to material breakage. Grains can be crushed, chipped, or broken into smaller fragments if mismanaged during the conveying process. One of the most common reasons for fractured grain is grain-on-grain impact.
This occurs when two pieces of grain impact each other and break into smaller fragments. It is more common when products are moving at very high speeds, especially if they’re not properly supported or if the bulk material handling equipment has some damage (for example, a crack).
The USDA Federal Grain Inspection Service has specific standards for kernel sizes of various grain types. Damaged grain that does not meet these requirements may be downgraded, meaning the grain quality is lower and sold at a lower market price.
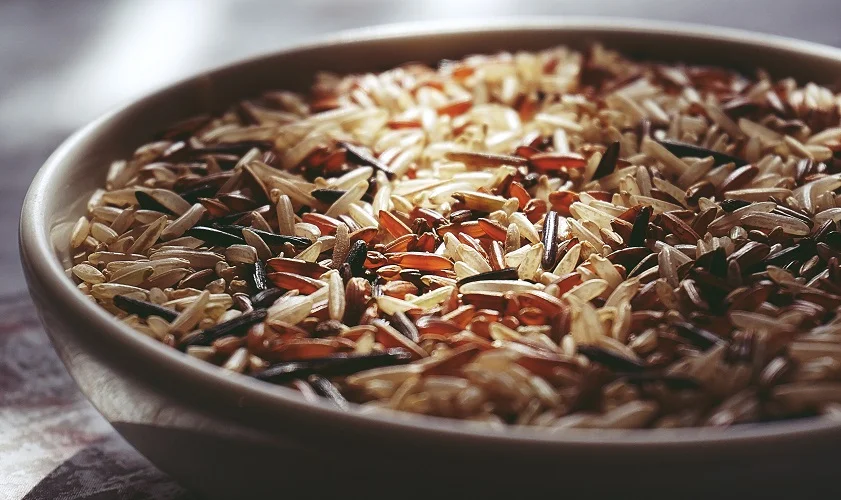
How to Avoid Common Issues With Specialty Grain Conveying?
All of the issues described above can be eliminated or drastically reduced with the right specialty grain conveying system. If you are looking to invest in a conveyor for your grain processing plant, here are some of the key features you’ll want to consider.
Enclosed Conveying System Reduces the Risk of Contamination and Cross-Contamination
Enclosed grain handling equipment will protect against external factors such as dust and ensure sanitary food processing. The closed design eliminates or reduces cross-contamination between lots/batches and minimizes exposure to contaminants in general. It also prevents material loss and improves throughput. Another advantage is that an enclosed conveyor system can be used in a cleanroom environment without compromising food safety standards.
Temperature-Control Environment Is Crucial for Maintaining Grain Quality
Temperature fluctuations can cause grains to deteriorate more quickly. This is especially true for specialty grains that are highly sensitive to moisture and require specific storage conditions (temperature, humidity). An enclosed conveyor will help you achieve stable temperatures throughout the conveying process to maintain grain quality. A temperature-controlled environment is critical if these products need to travel long distances to reach the final destination.
Speed Control Should Be Optimized for a Specific Grain Type
The conveyor speed needs to be carefully matched with your grain type and product specifications in order to reduce damage. If the grain is transported at high speeds, it can cause damage due to impact. If it is transported at very low speeds, the process may be too slow and increase the total operating costs of your facility. Grain types can vary significantly in size and shape, so an industrial conveyor system with variable speed control will allow you to optimize efficiency without compromising product quality or food safety standards.
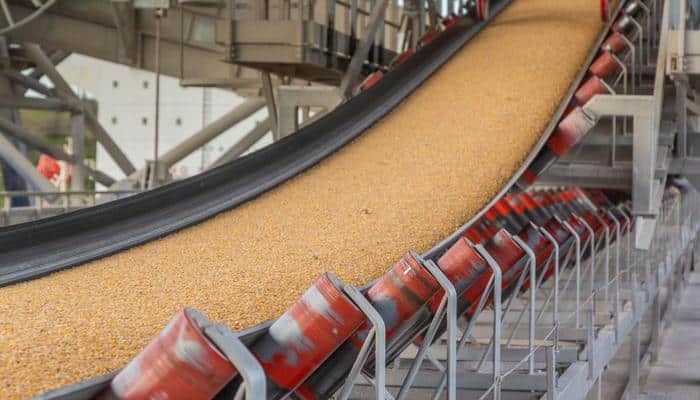
Conveying System Should Feature a Modular Design
If your facility doesn’t have a lot of floor space, a conveying solution that is easy to install and does not require much maintenance will be perfect for your processing needs. A modular design offers the benefit of being easily expandable in case you need more space later on.
It can also allow you to move within an existing facility with ease, minimizing downtime during reconfiguration or relocation projects. What’s more, if you have tight spaces or sharp corners, a modular system can easily be adapted to fit your facility’s exact needs.
Easy Cleaning and Sanitizing Will Help Keep the Facility Running Smoothly
Since you are working with food materials, it is understandable that you would want to keep your facility clean. If possible, choose a conveyor that is easy to sanitize and can be washed down frequently for maximum efficiency. Grain conveyors with Clean-In-Place mechanisms ensure that your production lines aren’t down for maintenance for too long. They allow for fast and easy washing so you can keep your facility running smoothly year-round.
Having a Scheduled Maintenance Plan Is Good for Maintaining Productivity
A scheduled maintenance plan is essential for reducing unexpected downtime and minimizing product damage due to equipment failure or wear and tear over time. You will want your conveyor manufacturer to offer a comprehensive, contractually guaranteed preventative maintenance plan.
This will include thorough cleaning and inspection of the system to remove any build-up or sediments that may lead to blockages, malfunctions, and other issues. Your conveyor contractor should perform all necessary repairs in a timely manner so your facility remains operational with minimal interruption. A comprehensive preventative maintenance plan can also help extend the overall life of your equipment.
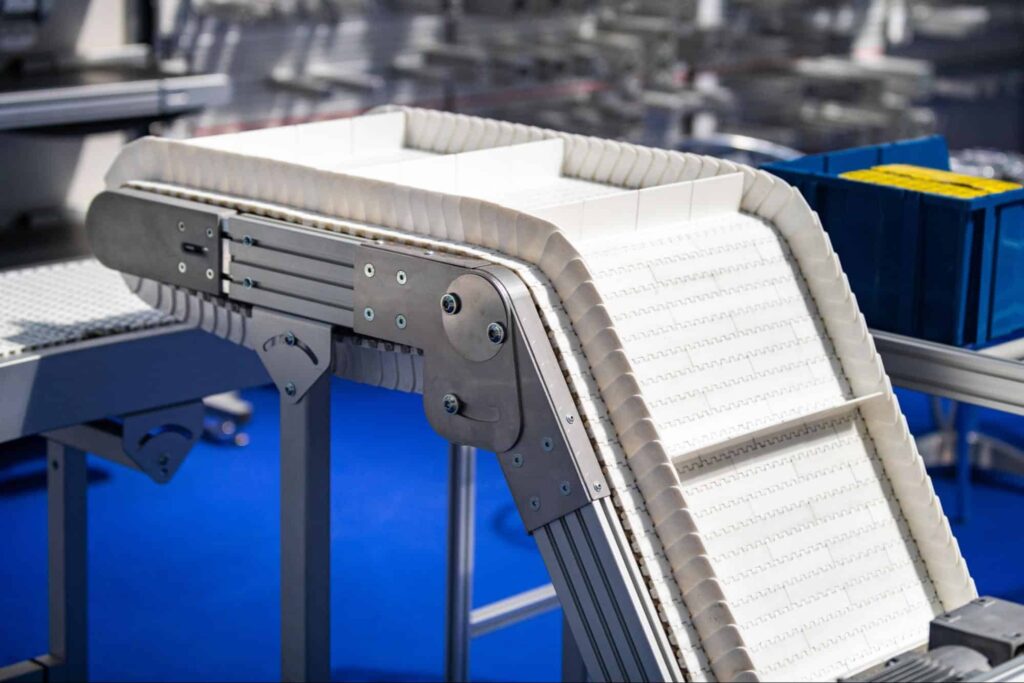
Tubular Drag Cable Conveyors – A Perfect Choice for Conveying Specialty Grains
A system that has all these properties and is specifically designed for conveying specialty grains and other fragile materials is a tubular drag cable system. Tubular drag conveyors feature protective tubing that shields the product from the environment as it travels through the process. They also allow you to control the speed of grain flow with pinpoint accuracy, ensuring your grain remains in optimal condition despite travel distances or external factors.
The drag cable is encased in nylon – it’s not in direct contact with the food material and can be easily cleaned. The enclosed design allows you to maintain stable temperatures throughout the process while minimizing workplace hazards due to dust or other contaminants. Although transporting specialty grains can be a challenge, with careful planning and a conveyor solution designed to meet your specific needs, it can be done properly.
You can minimize product damage without compromising food safety standards or the performance efficiency of your plant. Tubular cable conveyors offer all the benefits of an enclosed system with the exact level of control you need to transport fragile materials without any problems. They also feature easy installation – even in tight spaces or corners – so they don’t require a lot of retrofitting or maintenance.
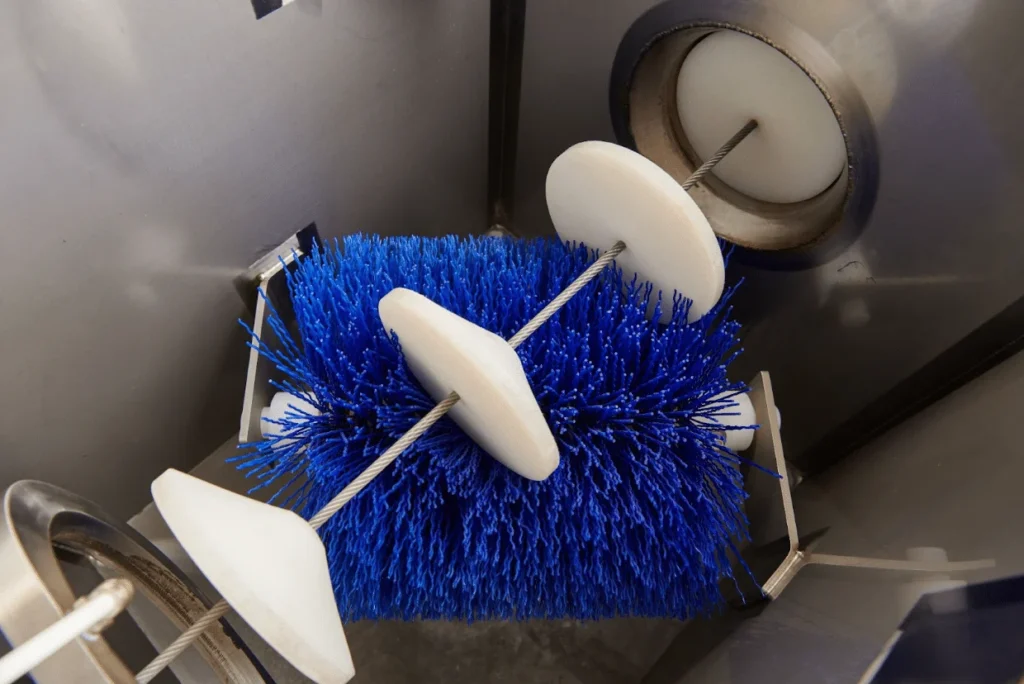
Reach Out to Cablevey Conveyors for Conveyor Solutions of the Highest Quality
Cablevey Conveyors offers a wide range of outstanding conveyor systems for specialty grains, from enclosed systems with optimal control speed to a classic conveyor belt for the warehouse. We specialize in providing expertly crafted, safe, and efficient conveying systems that will increase your productivity and make the production process simpler. Contact us today if you need help choosing the right system for your facility!
FAQ
What Are Specialty Grains and Why Are They in Demand?
Specialty grains, including rye, oats, rice, millet, and barley, have seen a surge in demand due to rising awareness of food intolerances and allergies and the popularity of diets like paleo and ketogenic. These grains are a suitable alternative for those intolerant to wheat and soybeans and require meticulous processing due to their fragile nature.
What Challenges Arise in Handling Specialty Grains?
Transferring stored grain within a facility can be complicated, especially for valuable specialty grains. Challenges include reducing breakage, managing dust hazards, maintaining grain quality, and retaining product value while minimizing loss during conveyance.
What Is the Significance of Contamination in Grain Processing?
Contamination involves unwanted foreign substances in a product. It can be physical (e.g., glass), chemical (e.g., pesticide), or biological (e.g., bacteria). Cross-contamination, where one batch contaminates another, is especially concerning in the food industry as well, leading to potential recalls and safety issues.
How Does Grain Dust Impact the Production Process?
Grain dust can lead to worker respiratory issues, heightened fire or explosion risks, and machinery clogging. An open belt conveyor system, for instance, can lead to substantial dust accumulation. In 2020, dust caused 165 fires and 60 explosions globally, leading to 88 injuries and 10 fatalities.
Why Are Specialty Grains Prone to Damage?
Specialty grains like oats and rye are delicate and can easily fracture during conveyance. Damage often arises from grain-on-grain impact, especially when grains move quickly or if equipment is damaged. Compromised grains may not meet USDA Federal Grain Inspection Service standards, resulting in downgrading and reduced market value.
What Features Are Essential in a Specialty Grain Conveying System?
Essential features include an enclosed design to mitigate contamination risks, temperature-controlled environments for grain quality, speed control tailored to grain type, modular design for adaptability, easy cleaning mechanisms, and a robust maintenance plan to maintain productivity and equipment longevity.
How Do Enclosed Conveying Systems Benefit Grain Handling?
Enclosed systems protect grains from external contaminants like dust and reduce cross-contamination risks between batches. They prevent material loss, enhance throughput, and can operate in cleanroom settings, upholding food safety standards.
Why Is Temperature Control Crucial in Grain Conveying?
Temperature fluctuations can expedite grain deterioration, especially for moisture-sensitive specialty grains. An enclosed conveyor maintains stable temperatures, ensuring grain quality remains intact, particularly when conveyed over long distances.
What Advantages Does the Tubular Drag Cable Conveyor Offer?
This conveyor is specifically designed for fragile materials like specialty grains. It features protective tubing, offers precise grain flow speed control, and ensures grains remain optimal. Its enclosed design minimizes dust hazards and maintains consistent temperatures. The drag cable, encased in nylon, avoids food contact and is easy to clean.
Who Provides High-Quality Conveyor Solutions for Specialty Grains?
Cablevey Conveyors specializes in top-notch conveyor systems for specialty grains. From enclosed systems with speed control to classic conveyor belts, Cablevey Conveyors offers efficient, safe, and expertly crafted solutions to streamline production processes.