In a $11.99 trillion global food market, the processing industry faces contamination, sanitation, and product integrity challenges. A tubular conveying system is the solution, so learn more about why tubular drag conveyors are ideal for food processing. Ensure product integrity and streamline operations. We’ll now explore why tubular drag conveyors are ideal for material transport in the food processing industry.
Why Tubular Drag Conveyors Are Ideal For Food Processing?
Tubular drag conveyors are ideal for food processing due to their enclosed design, gentle material handling, and efficient, sanitary operation. Preventing contamination, ensuring product integrity, and offering versatile configurations, these conveyor technologies elevate efficiency and hygiene in the food industry, making them a perfect solution for diverse applications.
What Are the Unique Challenges of Food Conveying?
The global food market (fresh food, processed food, and pet food combined) is expected to reach $11.99 trillion by 2027, according to a report from Statista. The food processing industry is a critical part of this market, responsible for turning raw ingredients into finished products that are safe for human consumption.
The largest food market segment is confectionery & snacks, with a market size of $1.56 trillion in 2022. To better understand why these conveyor solutions and not the traditional conveyor belt systems are ideal for food conveying, it’s important first to understand the unique challenges of this type of conveying.
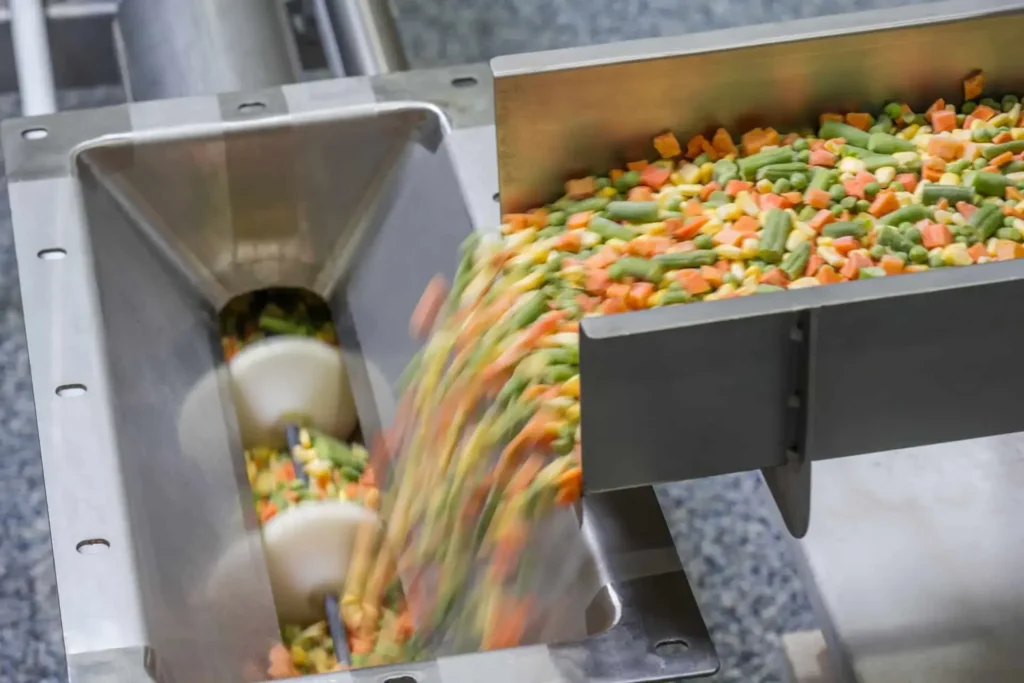
Preventing Contamination With Reliable Automated Conveyor Systems
One of the biggest challenges of food conveying is contamination. When raw materials and finished products are transported through a facility, they are at risk of contracting bacteria and other contaminants. This is a serious concern in the food industry, as even a small amount of contamination can cause foodborne illnesses. According to the FDA, over 850 foodborne illness investigations have been conducted in the United States since the start of 2022.
A particular subsection of contamination is cross-contamination. In cross-contamination, bacteria or other contaminants (such as chemical contaminants) are transferred from one food product to another. This risk intensifies the importance of implementing stringent measures in industrial conveyor systems and thorough conveyor installation supervision to mitigate the potential for product recall and safeguard a company’s reputation.
Automated Conveyor System Sanitation and Manufacturing Practices
Following closely on the heels of contamination is sanitation. To prevent cross-contamination and maintain a safe working environment, food processing facilities must be kept clean and sanitized at all times. This can be challenging, as food processors must constantly balance keeping their facilities clean enough to meet food safety standards while ensuring that production isn’t disrupted.
The conveyor sanitation standards and guidelines in the United States are put forth by agencies such as the FDA and the USDA. These standards are designed to ensure that food contact surfaces (including conveyors) are cleaned and sanitized regularly.
In the realm of conveyor manufacturing, adherence to additional standards, such as the voluntary 3-A sanitary standards, is also observed by some processors. This commitment to rigorous sanitation practices is integral to upholding the highest hygiene levels in the food processing industry.
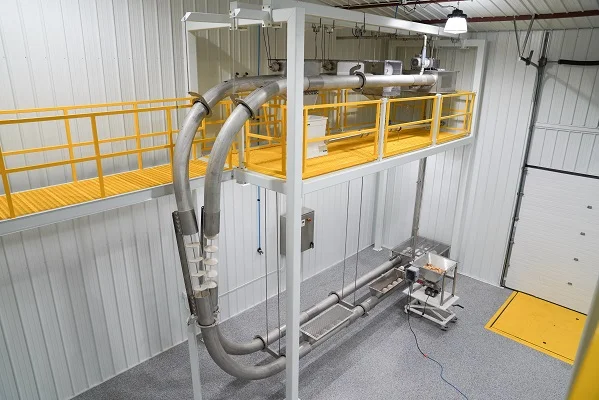
Maintaining Product Integrity With Manufacturing Conveyor Systems
Reducing the amount of material and product damage and loss is a crucial part of any production process, especially in the food industry. This is because food products are often perishable, meaning they can go bad quickly if not handled properly. They are also fragile, which makes them susceptible to damage. Product damage and loss can occur for a variety of reasons, including:
- Mechanical damage from conveyor components,
- Improper handling or packaging,
- Contamination,
- Exposure to extreme temperatures and humidity levels.
To prevent product damage and loss, food processors must take special care to ensure that their conveyors are designed and operated properly.
Explore Other Possible Challenges With Food Processors
Aside from the three main challenges discussed above, food processors also face other conveying challenges. Although these may not be unique to the industry, you should know about them. Here are some of them:
- High energy consumption,
- Noise pollution,
- Dust generation,
- Downtime due to maintenance.
These issues are not unique to the industry but can be effectively addressed through meticulous conveyor engineering and selection processes. Implementing proper conveyor design strategies becomes paramount in mitigating these challenges and ensuring optimal performance in food processing facilities.
Are Tubular Drag Conveyors the Ideal Solution?
Now that we’ve explored the unique challenges of food conveying, let’s take a look at why tubular drag conveyors may be the ideal solution. This automatic conveyor system consists of a closed tube with a series of circular solid discs running through it.
These discs are evenly spaced out along a chain – thus having a tubular drag chain conveyor – or a cable. The discs are connected to the chain or cable and don’t move independently from it. Also, it’s a type of mechanical conveying system, meaning that it uses moving parts to transport materials. They are often used to transport dry, free-flowing materials such as:
- Powders,
- Granules,
- Flakes,
- Pellets.
When it comes to moving certain food products from one stage of processing to the next, tubular drag conveyors are a clear choice. They are ideal for moving:
- Breakfast cereal,
- Snack foods,
- Nuts,
- Spice blends,
- Coffee beans,
- Tea blends,
- Granular pet food,
- Frozen food,
- Specialty grain.
In addition to their benefits in food processing, they can also be configured to fit pretty much any floor plan and can be built to meet the specific needs of your operation.
Reasons Why Tubular Drag Conveyors Are the Best Solution for Your Material Handling
Because of their characteristics, these conveyors are well-suited for use in the food industry. Some unique features and benefits make these conveyors the preferred choice for industries seeking superior performance, contamination-free transport, and streamlined operations. Here are some of the most important features to be aware of:
Enclosed Systems
Tubular drag conveyors are enclosed systems. This means that the materials being conveyed are completely sealed off from the outside environment. This is important in the food industry as it helps to prevent contamination and product damage or loss.
This also helps to keep dust levels down. Dust can be a health and safety hazard in any workplace, but it’s especially dangerous in food processing facilities, as it can also contaminate the food.
Extremely Gentle Conveying
Compared to a traditional belt conveyor system, such as a pneumatic or screw conveyor, tubular drag conveyors are much gentler on materials. The discs inside the tube create “pockets” where the material being conveyed can sit.
These pockets protect the material from being damaged during transport. With a tubular drag conveyor, you can expect little to no product damage or degradation. The pockets also help to control the flow of material, preventing it from moving too quickly and becoming damaged or degraded.
Sanitary Design
Tubular drag conveyors are designed with sanitation in mind. They are made of stainless steel, which is easy to clean and sterilize. The smooth, enclosed surfaces of tubular cable conveyors make them easy to clean.
Tubular cable and disc conveyors are infinitely more sanitary than tubular chain conveyors. This is because the cable in cable and disc conveyors is encased in sealed nylon – the cable doesn’t accumulate or adversely affect the material being conveyed. This isn’t the case with the chain in chain conveyors, which occupy more space within the tube and can become contaminated with the material accumulation being conveyed.
Clean-In-Place Mechanisms
Cablevey cable and disc conveyors, in particular, are outfitted with clean-in-place (CIP) mechanisms. What does this mean? CIP mechanisms enable the conveyor to be cleaned without having to disassemble it, and the reason is cleaning conveyor belts. This helps to reduce downtime for cleaning and makes for fast changeovers between products.
Efficient Operation
Tubular drag conveyors are highly efficient systems. They have low energy consumption and require little maintenance. This is partly because they have very few moving parts. The chain or cable in the system has to be tensioned, but it can be done with the simple turning of a knob – no tools, no mess, and no fuss.
Another reason for their efficiency is that they can move relatively large volumes of material quickly and easily. Of course, the exact volume will depend on the specific system’s capacity, among other factors.
Flexible Design
Finally, tubular drag conveyors are very versatile and can be designed to meet the specific needs of any food processing facility. For example, they can be configured to operate in horizontal, vertical, or incline applications. They can also be designed with multiple inlets and outlets.
This flexibility means that they can be used in a wide variety of food processing applications, from conveying raw ingredients to packaging finished products.
Tubular drag conveyors are also capable of multi-directional operation – if your processes demand it, they can even be designed to change direction mid-conveyance. This makes them very versatile and allows them to be used in a variety of food processing applications.
Cablevey Conveyors Is One of the Best Conveyor Systems Manufacturers in the Market
The food processing industry has unique material handling needs, including minimizing contamination and keeping the production lines sanitary. Tubular drag cable conveyors are ideally suited for this industry, as they are enclosed, gentle on materials, easy to clean and sanitize, and highly efficient.Although we’re one of the belt conveyor manufacturers with top-notch conveyor belt system options, our innovative tubular conveyor is ideal for food processing. For more information on tubular drag conveyors and how they can benefit your business, contact Cablevey Conveyors today. We would be happy to answer any questions you may have.